Polyethylene pipes for gas pipelines are products that are manufactured by continuous extrusion. Such pipes are used when laying a variety of highways for gas transportation. Today, due to its technical characteristics and the relative cheapness of PE products, they have gained great popularity in various industries (including gas supply).
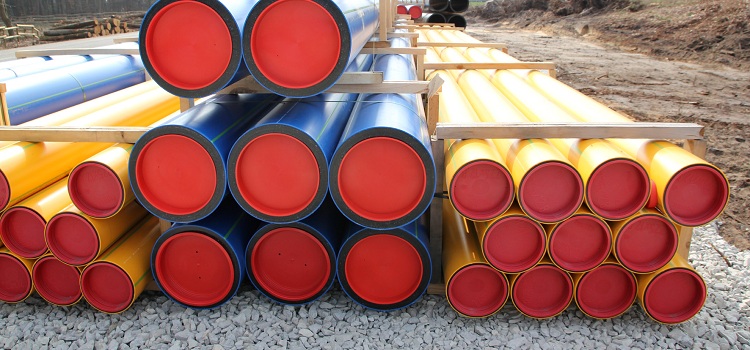
Polyethylene pipes are applicable for the installation of various communications, including gas networks
Content
The main advantages and disadvantages
Like any other product, a gas pipe PE differ in a number of positive qualities, which determine their effectiveness. Consider the main advantages of this product:
- have resistance to corrosion, unlike many metal pipes;
Note! The low weight of such products makes it possible to simplify their transportation, storage and installation. Steel pipes, due to their weight, are difficult to install and transport, and therefore PE products are increasingly preferred.
- installation of such pipes is simple. In addition, the speed of installation work of polyethylene parts is higher when compared with metal pipes;
- polyethylene is resistant to aggressive chemicals and does not need additional electrochemical protection;
- do not need to install waterproofing materials, since they themselves have excellent characteristics;
- polyethylene parts comply with all state quality standards;
- smooth walls of such products provide high throughput rates. Unlike metal parts, salt deposits and other particles narrowing the lumen of the pipe and particles do not settle on their walls;
- polyethylene pipelines are environmentally friendly and do not emit harmful substances that can cause harm to human health.
- the service life of polyethylene pipelines is significantly higher than that of metal counterparts. Under normal use, it can reach 50 years, and in some cases more;
- the cost of such products is lower than for metal products, which is a fundamental factor for many construction companies.
- It is also worth mentioning that they have low air and gas permeability rates. This is a very important point, given the fact which medium is transported through polyethylene gas pipelines.
Now consider the main disadvantages of plastic products:
- communications from polyethylene should be installed only by underground (closed) method;
- such pipes have good resistance to temperatures, however, with sharp temperature changes, their use is not recommended. This is especially true for low temperatures;
- in addition, there are restrictions on the depth of the laying of such pipelines - at least 1 m;
- Under a canal or other engineering structure, a gas pipeline made of polyethylene pipes is laid using special protective cases.Such cases are usually made of steel;
- Installation of HDPE pipes should be carried out by specialists who have permission to do this and have construction skills in this area.
Scope of polyethylene pipes
Communications such as gas pipelines made of polyethylene (including HDPE) are used quite often, however, due to the large number of requirements put forward to them - their scope is not so numerous.
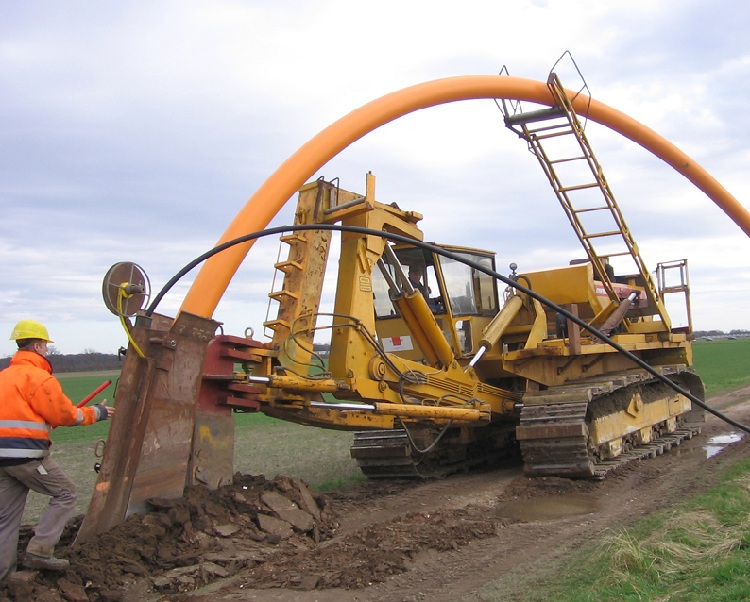
The low resistance of PE pipes to ultraviolet radiation determines the way these products are laid - only by the underground method
The fact that such pipes have poor resistance to ultraviolet rays prevents them from being installed indoors. But if you still perform an open installation, then they will quickly lose their qualities and become worthless. This should not be allowed, since the working medium in such structures is a combustible explosive gas. Therefore, such communications are mounted, as a rule, underground, in a closed way.
It is also worth noting that pipes for low pressure gas pipelines that belong to categories 1 and 2 are strictly forbidden to lay in places where crossings through any obstacles in cities and other settlements can be laid.
Characteristics of PE pipes for gas pipelines
Polyethylene pipes for the gas pipeline are made from special grades that belong to the pipe. As a rule, these brands are two main: PE 80 and PE 100. The class of pipes is established by pressure tests. Such checks are carried out for more than 1 year, which allows you to accurately determine the class of polyethylene products, as well as the maximum operating pressure at which the product will last at least 50 years.
Thus, a pipe that is made of polyethylene 100 is able to withstand (even with the same wall thickness) pressure indicators higher than parts marked 80.
Puseful information! The polyethylene pipes used for gas supply are made only using primary polyethylene. This is due to increased safety requirements for gas pipelines.
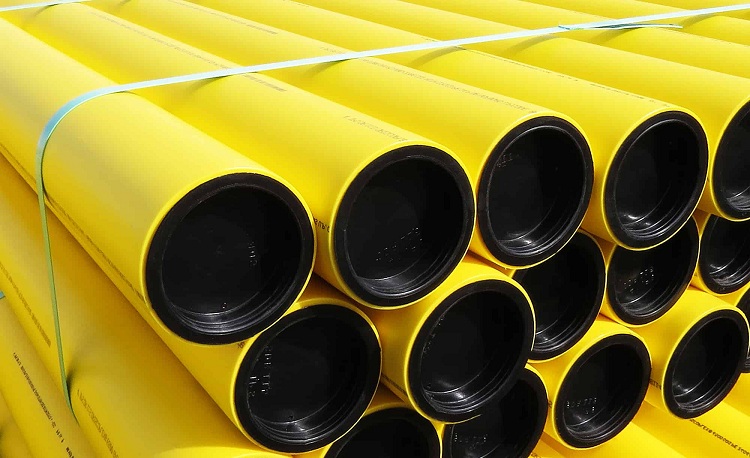
In gas systems, only products capable of withstanding the pressure characteristic of the gas supply line are used
The diameter of polyethylene pipes for gas pipelines ranges from 20 to 630 mm, and for underground gas consumption and gas distribution lines reach 1200 mm. This range allows you to expand the scope of use of polyethylene pipelines.
Another important indicator of polyethylene gas pipes is SDR. This indicator determines the ratio of the size of the pipe section to the wall thickness. The lower the SDR, the correspondingly the greater the wall thickness and the greater the pressure the product can withstand.
In addition, there is another rather important indicator - MRS. This indicator indicates the possibility of the PND pipe to withstand the pressure, which is expressed in megapascals. For pipes PE 80 MRS is 8 MPa, for PE 100 - 10 MPa.
In addition, plastic products may vary in color. The most common colors for such details:
- the black;
- blue;
- Orange;
- yellow.
Each pipe has its own marking, which is applied to the surface. Labeling is repeated through each meter of the product and contains the following information in a compressed form:
- material of which the pipe is made;
- product size;
- appointment;
- manufacturer and information about him;
- the consignment;
- Date of issue.
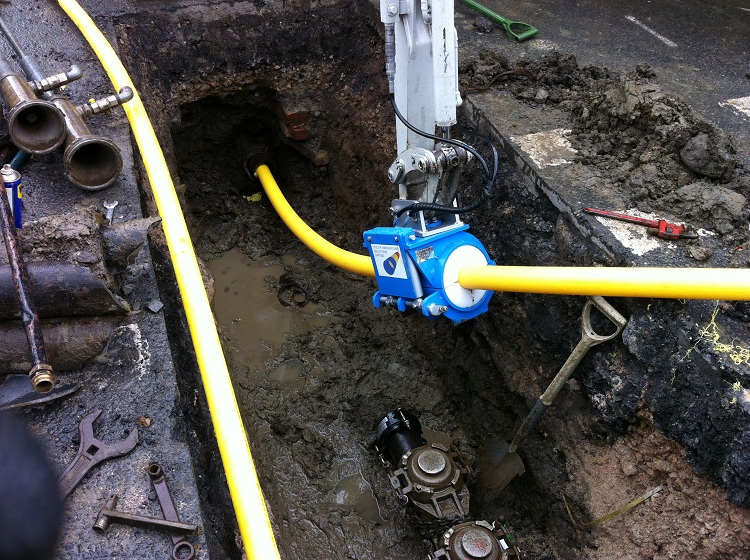
An important advantage of polyethylene pipes is their flexibility, which is why they are used when installing underground gas pipelines in unstable soils.
HDPE pipe properties
HDPE pipe is highly flexible, so it can be laid in moving soils. Such a useful property allows you to mount it in seismically active areas.The bending radius of the PND parts is equal to 25 of its diameters, which reduces the number of welded joints. The lower the number of joints, the more reliable the communication is considered and HDPE pipelines in this sense are incredibly beneficial.
In addition, PND products with cross-sectional indicators up to 180 mm are stored and transported in special coils. This greatly simplifies the transportation and laying process.
Note! The operational capabilities of PND pipelines make it possible to use them as a replacement for old communications. Such trenchless reconstruction is very popular today. And also for their installation using the modern method of horizontal directional drilling (HDD).
HDPE products are characterized by limited resistance to ultraviolet radiation and their installation is allowed to be carried out only underground. The fire resistance of such material is also quite weak, so the installation of such communications indoors is prohibited.
How gas pipelines are classified
Which pipeline will transport the combustible gas depends on the working pressure in the communication. The higher the pressure level in the system, the more stringent requirements are put forward when selecting individual elements for a gas pipeline. It is also worth noting that polyethylene pipes may not be used in all systems. There are systems with unacceptable gas pressure indicators for them.
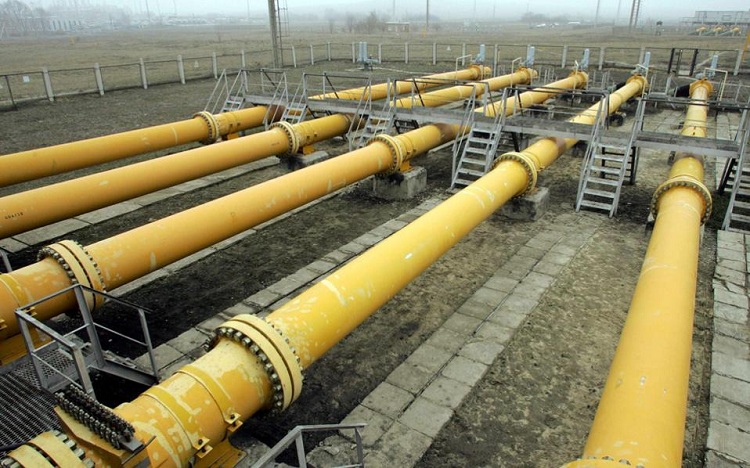
In gas pipelines of category 1, the use of polymer pipes is prohibited, for the installation of such pipelines it is permissible to use only steel products
Communications transporting gas to end consumers are divided into 4 main categories. Consider them:
- The first category includes gas pipelines that can withstand pressure from 6 to 12 atmospheres. For the transfer of liquefied hydrocarbon gases (LPG), the normal pressure is 16 atmospheres. The laying of such communications can be carried out both underground and above ground, as they are made only of steel material. The use of plastic pipes for gas pipelines belonging to category 1 is strictly prohibited.
The choice of the type of pipe for the line with a particular pressure can be made based on the data in table No. 1.
Table 1
SDR indicator | Type of pipe | |
PE 80 | PE 100 | |
Pressure, atmosphere | ||
17,6 | 3 | 6 |
17 | 3 | 6 |
9 | 10 | 6 |
11 | 6 | 6 |
13,6 | 6 | 6 |
- Gas pipelines that belong to category 2, as a rule, transport the working medium under pressure from 3 to 6 atmospheres. For these purposes, polyethylene pipes SDR 17 and SDR 17.6 are perfect. Such systems transport gases between city stations, which perform a gas distribution function.
- The third category includes gas pipelines that transport the working medium under a pressure of 0.005–0.3 MPa. They perform the function of delivering the medium to the distributors.
- The fourth category is represented by pipelines that distribute gas directly through separate, utility lines. Pressure indicators in such a system, as a rule, are less than 0.005 MPa.
Installation of a polyethylene gas pipeline
The polyethylene gas pipeline is mounted taking into account building codes and regulations (SNiP), as well as the necessary safety measures. All this is necessary to avoid unforeseen emergencies during the use of the gas pipeline.
Docking of two separate polyethylene parts is carried out by means of special connecting elements - fittings. Fittings are connecting elements of various configurations and are mounted by butt or electrofusion welding.
Important! During welding, all parts must be well fixed to prevent them from shifting.Reliable fixation is a very important parameter for arranging the tight connection of individual pipes.
The nozzles that are used for welding are mounted on pipes, after which the parts are heated and joined. After welding, the joint cools quite quickly (5-7 seconds). After the connection hardens, you must wait at least 20 minutes and the communication can be put into operation.