Concrete drainage trays are products that are made of concrete and are used to drain water from roads, pedestrian walkways, parking lots, park areas, etc. Structures made of reinforced concrete products, removing water from roads, increase the operational life of the road surface in general, which determines the popularity of their use. Such trays differ in the manufacturing method, shape and other parameters that are worth paying attention to.
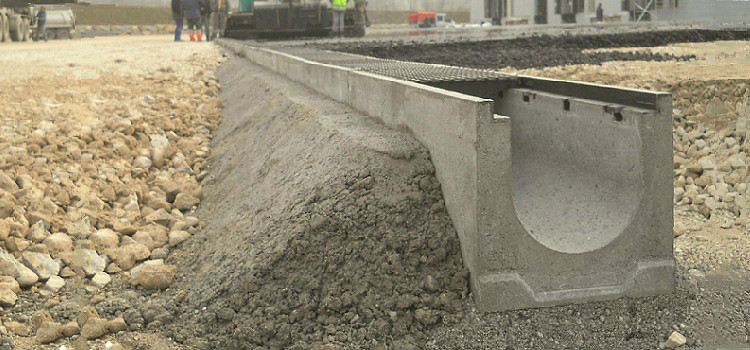
Drainage trays made of concrete are strong and durable, they are used to drain storm drains at a variety of objects
Content
What are drainage trays made of?
Concrete drainage systems are made of various types of special material - fiber-reinforced concrete. Polypropylene fibers are added to the finished fiber concrete solution during the production process, as a result of which polymer concrete parts are obtained. Thanks to the addition of polypropylene, drainage trays (admixture of polypropylene fibers) polymer concrete gain deformation resistance and resistance to bending.
Special fibers of metal fiber can be added to concrete mortar. This allows you to increase the resistance of the product to abrasion, tension, mechanical stress, etc. Reinforced concrete trays are very popular and are used almost everywhere.
To date, concrete trays made of cement material, the marking of which is not lower than M 500, are very popular. In addition to the cement material, one of the reinforcement options listed above is used.
Helpful information! Channels mounted from concrete drainage elements include auxiliary products - gratings. Lattices are equipped with even vertical drainage systems. These products are necessary to protect the channel from large debris: branches, stones, etc.
Such lattices are made of different materials depending on the specific situation. They can be made of metal material or of modern polymer combinations. The grilles are mounted on concrete parts using special fixing screws. If necessary, grilles can be removed for cleaning.
Methods of manufacturing concrete drainage systems
Today, two popular methods are used to make concrete drainage trays. Consider them:
- vibrocompression;
- vibration casting.
The vibropressing method for the production of reinforced concrete products is not particularly difficult:
- First, the cement mortar is poured into a special form.
- After that, air bubbles and excess moisture are removed from the mixture. To do this, use the press.
The solution itself includes two main components:
- cement;
- ground filler.
The filler is fixed with special fibers, which can consist of different materials:
- metal;
- polymer;
- fiberglass.
Before starting the production process, all metal parts that will subsequently be included in the structure of the drainage trays undergo rust treatment.
Consider the advantages of trays made using vibrocompression:
- affordable cost;
- high coefficient of moisture resistance;
- resistance to mechanical stress;
- a smooth inner surface that increases channel throughput and eliminates the accumulation of debris in the system;
- resistance to temperature differences.
However, like any other product, such trays have their drawbacks:
- large mass, which complicates the transportation of these products;
- quite complicated installation.
Vibration casting is the second popular method of manufacturing drainage trays. The manufacturing process of concrete products using vibrocasting is not particularly difficult, however, it is rather slow and costly. Products obtained in this way come out of lower quality than analogues made by means of vibropressing.
Let us consider in stages the manufacturing process of concrete drainage products using vibrocasting:
- First of all, the concrete solution is poured into a special form.
- Next, the form with the solution is placed on a special table that creates vibrations. Due to the vibration effect, the concrete mortar is formed and compacted.
Vibration does not reach the inside of the solution, acting, as a rule, only on the outer zones. As a result, an insufficiently high-quality product is obtained, which quickly deteriorates during operation.
Operational Overview
Drainage concrete parts are used only for hard coatings, since the removal of excess moisture from the soil is performed by a completely different system - drainage. Trays for storm sewer communication are operated in such cases:
- near highways;
- on the streets of the city;
- on footpaths (asphalt, tiled);
- on concrete sites.
- inside various production halls;
- in car parks;
- near a variety of objects related to the infrastructure of the city.
Important! It is not recommended to mount a concrete channel near a private house. In such cases, usually the trays are laid in dug trenches without taking into account the degree of heaving of the soil. Fouling of the soil is a characteristic that reflects the deformation shifts in the soil during its transition from thawed to frozen state. As a rule, own-hand laying of the channel from concrete trays leads to their displacement due to heaving of the soil in the winter.
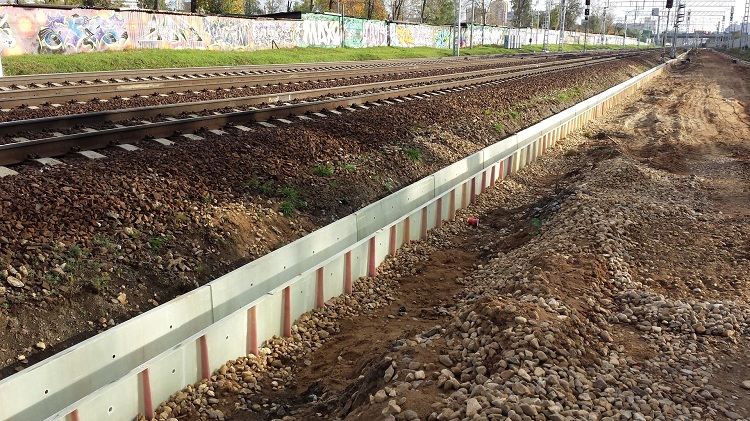
Trays are laid along roads or railways, parking lots and other facilities where outflow of storm and melt water is required.
Such products in combination with a special blind area produce high-quality removal of thawed, waste and rain moisture. Thanks to concrete channels from drainage trays, the service life of road and other hard coatings is significantly increased.
Benefits of Concrete Trays
Let us consider in more detail the main advantages of concrete drainage parts:
- concrete has good resistance to harmful corrosive effects, which affects its operational life. In normal use, concrete trays can last several decades;
- concrete trays have a good coefficient of frost resistance. They easily tolerate temperature fluctuations. These characteristics allow the use of concrete gutters in all regions, regardless of climatic conditions;
- the wear resistance of these products eliminates their destruction during operation, and additional reinforcement with polymer fibers or metal fiber allows you to achieve high strength and resistance to mechanical stress;
- the heavy weight of these parts can be interpreted not only as a minus, but also as a plus. During operation, the displacement of the trays due to the influence of heavy precipitation is excluded;
- concrete drainage trays are environmentally friendly products and do not emit substances harmful to human health;
- from a structural point of view, such parts are simple and do not require special care. Periodically, they need to be cleaned of debris that interferes with normal sanitation;
- The low cost of concrete drainage trays makes them popular. Channels from these parts pay off pretty quickly.
Types of drainage concrete trays
According to the laying option, two main types of concrete drainage channels are distinguished:
- ordinary (horizontal);
- with a spillway located vertically.
Lattices to concrete channels are made of different materials, namely:
- cast iron;
- steel;
- high strength polymers.
The surface of cast iron gratings may have a protective layer of galvanization, which protects the product from corrosion. Steel gratings, as a rule, are made of stainless steel. Plastic grilles are used much less often than the above analogues, however, they can be found in the absence of large loads on the product.
In addition, all lattices for structural design are divided into two types:
- cellular;
- slotted.
Concrete trays are used in different situations. Depending on the operational features and purpose, they can be:
- for drainage of melt and rainwater;
- for the organization of a protective case in which cabling is laid;
- for installation of heat-conducting communications.
Installation of concrete drainage structures can be carried out in two ways:
- under a certain bias (for high-quality water removal);
- without bias.
Note! On the market you can buy another type of product - water trays. These parts are made of concrete and various additives and are used to collect and remove moisture. Such water receivers as well as drainage channels are equipped with protective grilles and are used to remove moisture from parking lots, pedestrian walkways, etc.
All reinforced concrete drainage trays (reinforced concrete) can be divided into classes according to the load that they can carry, into four categories:
- C250. Such gutters are used to divert rain and melt water from roads, which are notable for their low traffic intensity. They are also mounted in parking lots for cars.
- D400 Products that belong to this load class are laid near highways with high traffic density, near gas stations.
- E600. Devices belonging to this class of load are mounted for the removal of rain and melt water from main roads, as well as in large industries.
- F900 The most reliable concrete trays that are used for drainage at airports.
The dimensions of the drainage concrete trays can be different, however, there is a standard length of the gutter - 1 meter. Section sizes can vary from 100 to 500 mm. The volume of the tray is calculated based on its size individually.
Installation of drainage trays
Before proceeding with the laying of the drainage concrete channel, it is imperative to draw up a preliminary plan for the future design. The project must include such moments:
- location of drainage channels and their components;
- number of parts and auxiliary components;
- final estimate of the construction event.
The preparatory phase is necessary to calculate all the nuances of the installation of concrete drainage products, their preparation, and in order to rent the necessary equipment.
Consider the phased installation of concrete gutters:
- First of all, you need to dig channels of the right size. The channel size must exceed the corresponding tray setting. This is necessary to strengthen the soil at the location of the structure.
- At the second stage, the soil is compacted in trenches.
- Further, in the trench, it is necessary to fill up a layer of sand, which will serve as a "pillow".
- A concrete layer is laid on the sand cushion, which will act as a support for the gutters.
- Using special equipment, concrete trays are laid in prepared trenches on a concrete layer.
- Further, the sides of each drainage concrete goods tray are strengthened with a liquid cement mortar.
- At this stage, the trays are docked using the grooves. To increase the tightness, the joints are treated with a special sealant based on bitumen or acrylic.
- Installation of protective gratings on top of concrete gutters.
- Ready drainage channel is joined with storm sewer communication.