Due to its high performance characteristics and low cost, galvanized steel is universally used for laying pipelines and creating structures for various purposes. The traditional way of joining metal products is welding of galvanized pipes. This process has a number of features that must be taken into account.
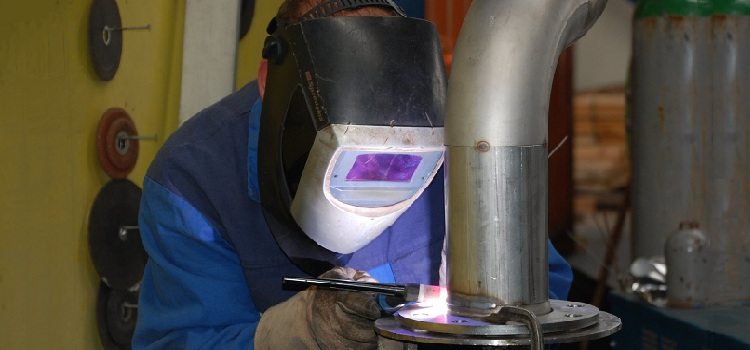
Welding galvanized pipes is a simple process, but you need to know the intricacies of working with such material
Content
Is it possible to weld galvanized pipes? Welding methods
When thermally bonded, the metal surface at the seam location is exposed to a temperature of about 1200 degrees, while zinc boils at 906 degrees Celsius. Therefore, during the welding process, the zinc coating burns out. The following negative phenomena are associated with this aspect:
- Zinc in a gaseous state is very harmful to health. Without high-performance ventilation, the likelihood of poisoning the welder and temporary suffocation is high.
- In the weld, the zinc coating is broken and corrosion protection is lost.
- Intensive evaporation of zinc during welding contributes to the appearance of pores and intercrystallization cracks. The resulting compound will be unreliable due to its low strength.
Given the above, the welder must necessarily observe increased security measures. During cooking, a special respirator and a protective mask made of dielectric materials are put on the face. Hand protection is provided by rubber gloves coated with a heat-insulating cloth. To prevent unnecessary foaming of the zinc layer, allows the processing of the joint surface with hydrochloric acid. For a high-quality work result, the evaporation of the zinc layer must be avoided. This condition can be provided by several welding options.
The first way is to mechanically clean the zinc weld zone with an abrasive emery wheel or brush on metal. In this case, then galvanized is welded like ordinary black pipes. The negative point is that the seam without zinc is deprived of corrosion protection, and this negatively affects the product's service life. As a result of moisture, the pipe will quickly rust and the affected area will need to be replaced. This means that in the future there will be additional cash costs and time costs for the alteration of the structure.
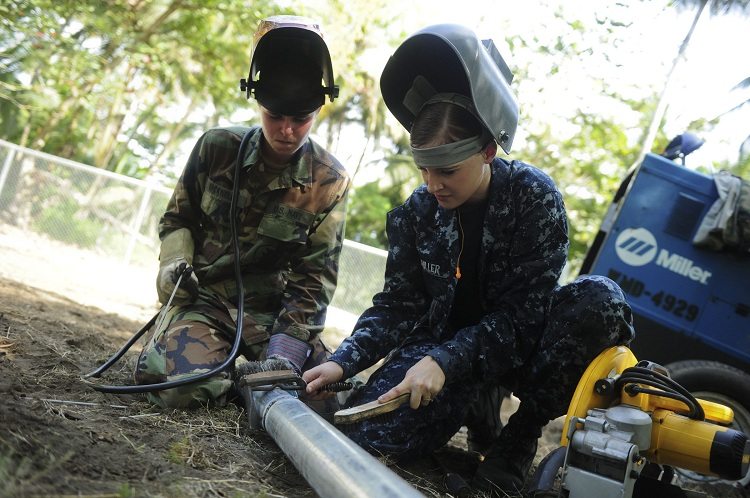
Cleaning the weld area before starting work will prevent the evaporation of zinc from the pipe surface
Note! A small surface area without an anticorrosive layer can be protected by the cathode path (zinc is transferred to the exposed zone by the electrochemical method).
It is possible to achieve high-quality welded joints without damaging the anti-corrosion coating by applying special fluxes when soldering. This technology is applicable in cases where cleaning joints from zinc is technologically impossible. When connecting, HLS-B flux and UTP 1 alloy are used. The method is optimal when cooking utilities in the water supply. Flux is not harmful to health, because it completely dissolves in the aquatic environment without the formation of harmful compounds.
How to cook galvanized pipes using flux
The edges of the pipes prior to connection are degreased and cleaned to a state of metallic luster. Cleaning should be carried out not only on the outside, but also on the inside. The preforms are preheated 20-30 cm long on each side of the planned joint. For efficient welding of products with wall thicknesses up to 3 mm, there is no need for specific edge preparation. The width of the gap between the ends is equal to 2-3 mm. With thicker pipes, an opening angle of 80-90 degrees and a blunting height of 1-1.5 mm are performed. The gap width is similar.
The flux is heated to a medium between liquid and solid and is applied in a thick layer to the surface of the compound. The amount of material used is twice as large as for welding ordinary steel products. The purpose of the flux is to take excess heat from the welding machine, which prevents the evaporation of zinc from the edges.
When heated, the flux changes its color from yellow to white, and when the joint reaches the soldering temperature it transforms into transparent. Thus, the state of the flux can determine the time to start soldering.
Selecting the size of the nozzle of the burner for soldering, you need to start from the wall thickness of the galvanized product. The size ratio is shown in table No. 1.
Table 1
Nozzle size mm | Galvanized pipe |
1 -2 | diameter up to 250 mm, wall thickness 2-6 mm. Filling seams in products of any kind |
2-4 | diameter over 250 mm and thickness over 2-6 mm |
When soldering galvanizing, the rule applies: the nozzle of the burner should be one size smaller than when joining a conventional steel pipe of similar dimensions.
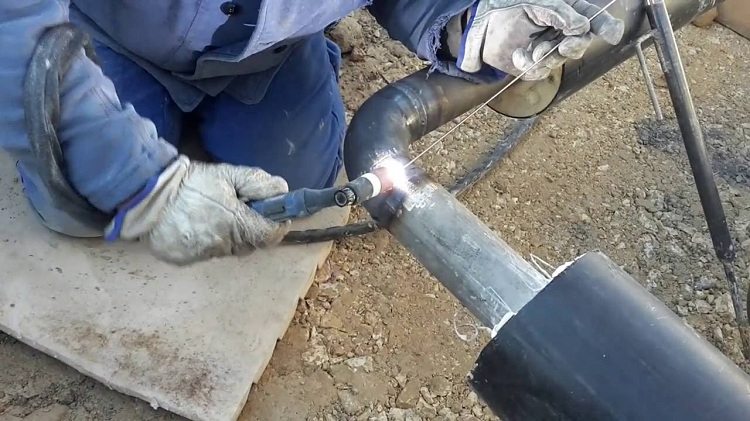
For high-quality welding of a galvanized pipe, it is extremely important to choose a torch of the appropriate size and correctly adjust the flame
Why is it important to choose the right nozzle? Using an overly large version will overheat the workpiece, and the zinc will evaporate. This means that its corrosion resistance and strength characteristics will deteriorate (molten zinc will lead to the formation of pores). If the nozzle is not large enough, the metal surface will not heat up to the required temperature, which will cause the solder to adhere to it.
During soldering, an acetylene-oxygen flame is used, which is exposed to excess oxygen. An excess of oxygen is necessary so that, when the solder is melted, its oxide is formed as a result of reaction with silicon. It is silicon oxide that prevents the thermal evaporation of zinc.
Important! It is necessary to adjust and ensure the stability of the flame of the burner. Heat should be focused on the edges and in the gap between the workpieces. Unstable flame leads to overheating of the pipe section near the connection.
For welding with a gas torch, it is best to use the "left" technique, that is, place the bar in front of the flame. In this case, the fire will fall on the solder bar, and not on the metal surface. When performing a remelting seam, the burner should be tilted at an angle of 70-75º. For the filling passage, the angle should be 15-30º. The torch can be positioned in any spatial position, but the most convenient is the lower one; it is convenient to monitor the weld pool with it. Pipe joining up to 4 mm thick occurs in one pass. If the thickness value is higher, multi-pass welding is used.
After the connection is completed, the welded joint is cleaned of excess soldering material. Outside, the pipe is washed with water and held with a wire brush. It is important not to overdo it so as not to damage the zinc surface. The inner shell must be filled with water for a day and rinsed.
Properly performed soldering of galvanized pipes allows you to get connecting seams that do not require additional corrosion protection.
Manual arc welding of galvanized pipes
Reducing the welding speed and increasing the current avoids the formation of pores in the fillet and butt welds.The use of specialized electrodes can provide such conditions. It is especially important to make the right choice of how to cook a galvanized pipe depending on the type of steel. When connecting galvanized carbon blanks by manual arc welding, you need to stop on the rutile coated electrodes. For low alloy steels, basic coated electrodes can be used. Rutile electrodes have several advantages:
- The electrode contains titanium oxide, which allows you to quickly and easily ignite the arc, both for the first time and repeatedly.
- The resulting welding arc provides high-quality, tight welds without cracks, with high fatigue strength.
- Loss of fused material due to spatter is minimal.
The rutile coating of the electrode may contain some iron powder. This allows you to reduce the specific gravity of carbon in the zinc layer and increase the resistance to cracking.
Electric welding of galvanized profile pipes requires at least minimal experience with the welder. In addition to coating the electrode, its thickness is of great importance. The arc power directly depends on the size of the electrode. Choosing an electrode too thick can lead to burning, and too thin to weak strength characteristics of the compound. The most common wall thickness of profile products is 1.5-5 mm, so you should choose an electrode with a diameter of 2 or 3 mm.
In the welding process, the speed of movement of the electrode through the metal is of particular importance. At a slow pace, there is a risk of burning the pipe, too fast pace will not provide the necessary quality of the connecting seam. Suitable speed is developed during training.
Note! After welding, the joint and the heat-affected zone must be treated with an anti-corrosion compound.
The protective agent should have the following qualities:
- high adhesion to the metal surface;
- corrosion resistance at zinc level;
- ease of application without high-tech expensive equipment.
As a protective layer, paint, which includes at least 94% zinc dust, has worked well. Unsaponifiable synthetic binders are used for its manufacture, so it is held on vertical surfaces and is easy to apply.
Another way to restore the surface is surfacing 99.99% zinc wire containing 99.99% zinc. Zinc-cadmium rods are also suitable for this role.
Alternative galvanized pipe joining methods
Thermal zinc-free galvanizing can be joined by threading. Due to the complexity of application, it is used only on pipes of small diameter. The negative point of such a connection is the high cost of work compared to traditional welding. It is also worth noting that at the junction during the cutting process, the zinc layer will be damaged. Consequently, the pipe at the junction will be more susceptible to corrosion.
In water supply, heat supply and other engineering networks, factory-welded systems that are assembled according to the principle of the designer can be used. A factory-made kit includes a sleeve with a seal that bolts to a groove at the edges of the pipe. This method is quite new for the CIS countries; its main advantages are high installation speed and reliable connections.
In conclusion, we note that with a welded joint, high-quality seams are possible with strict observance of all the rules. First of all, overheating and evaporation of zinc should be prevented, which is achievable only with the use of special rutile electrodes and flux. The qualifications of the welder play a large role in both electric arc and gas welding. Other pipe methods are not so popular, due to the lowest cost of welding.