Aufgrund seiner hohen Leistungseigenschaften und geringen Kosten wird verzinkter Stahl universell zum Verlegen von Rohrleitungen und zum Erstellen von Strukturen für verschiedene Zwecke verwendet. Die traditionelle Art, Metallprodukte zu verbinden, ist das Schweißen von verzinkten Rohren. Dieser Prozess weist eine Reihe von Funktionen auf, die berücksichtigt werden müssen.
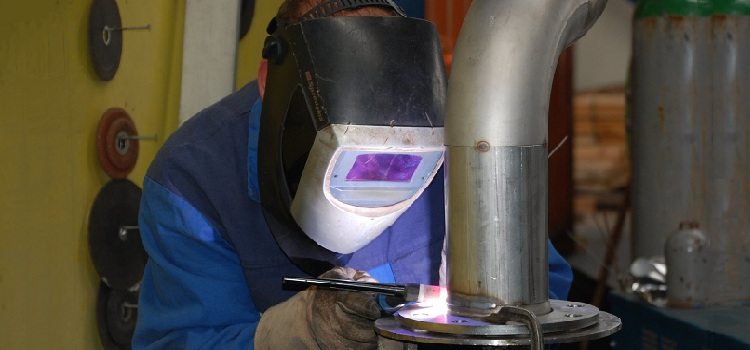
Das Schweißen von verzinkten Rohren ist ein einfacher Vorgang, aber Sie müssen die Feinheiten der Arbeit mit solchen Materialien kennen
Inhalt
Ist es möglich, verzinkte Rohre zu schweißen? Schweißmethoden
Bei thermischer Bindung ist die Metalloberfläche an der Nahtstelle einer Temperatur von etwa 1200 Grad ausgesetzt, während Zink bei 906 Grad Celsius siedet. Daher brennt während des Schweißprozesses die Zinkbeschichtung aus. Die folgenden negativen Phänomene sind mit diesem Aspekt verbunden:
- Gasförmiges Zink ist sehr gesundheitsschädlich. Ohne Hochleistungsbeatmung ist die Wahrscheinlichkeit einer Vergiftung des Schweißers und eines vorübergehenden Erstickens hoch.
- In der Schweißnaht wird die Zinkbeschichtung gebrochen und der Korrosionsschutz geht verloren.
- Das intensive Verdampfen von Zink während des Schweißens trägt zum Auftreten von Poren und Interkristallisationsrissen bei. Die resultierende Verbindung ist aufgrund ihrer geringen Festigkeit unzuverlässig.
In Anbetracht dessen muss der Schweißer unbedingt erhöhte Sicherheitsmaßnahmen beachten. Während des Kochens werden ein spezielles Atemschutzgerät und eine Schutzmaske aus dielektrischen Materialien auf das Gesicht aufgebracht. Der Handschutz wird durch Gummihandschuhe gewährleistet, die mit einem wärmeisolierenden Tuch beschichtet sind. Um unnötiges Aufschäumen der Zinkschicht zu vermeiden, kann die Fugenoberfläche mit Salzsäure bearbeitet werden. Für ein qualitativ hochwertiges Ergebnis ist es unbedingt erforderlich, die Verdunstung der Zinkschicht zu vermeiden. Dieser Zustand kann durch verschiedene Schweißoptionen bereitgestellt werden.
Die erste Möglichkeit besteht darin, die Zinkschweißzone mechanisch mit einem Schleifrad oder einer Bürste auf Metall zu reinigen. In diesem Fall wird dann verzinkt wie gewöhnliche schwarze Rohre geschweißt. Der negative Punkt ist, dass der Naht ohne Zink der Korrosionsschutz entzogen ist, was sich negativ auf die Lebensdauer des Produkts auswirkt. Aufgrund von Feuchtigkeit rostet das Rohr schnell und der betroffene Bereich muss ersetzt werden. Dies bedeutet, dass in Zukunft zusätzliche Bargeld- und Zeitkosten für die Änderung der Struktur anfallen werden.
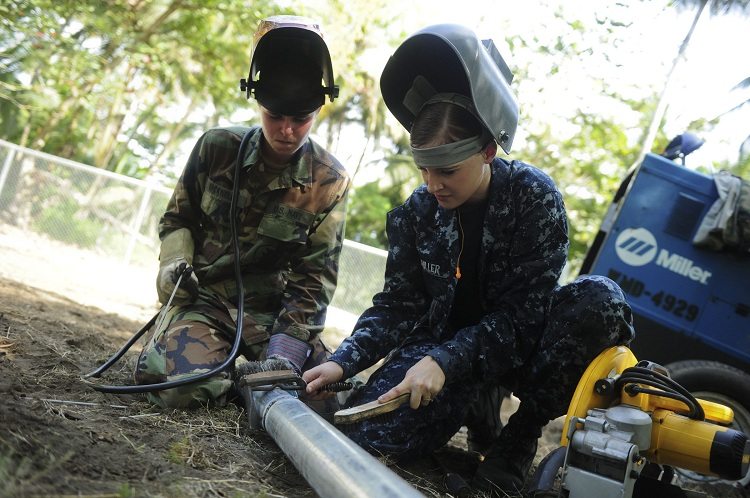
Durch Reinigen des Schweißbereichs vor Arbeitsbeginn wird die Verdunstung von Zink von der Rohroberfläche verhindert
Beachten Sie! Eine kleine Oberfläche ohne Korrosionsschutzschicht kann durch den Kathodenweg geschützt werden (Zink wird durch das elektrochemische Verfahren in die exponierte Zone übertragen).
Durch Aufbringen spezieller Flussmittel beim Löten können hochwertige Schweißverbindungen erzielt werden, ohne die Korrosionsschutzbeschichtung zu beschädigen. Diese Technologie ist in Fällen anwendbar, in denen das Reinigen von Fugen von Zink technologisch unmöglich ist. Beim Anschließen werden HLS-B-Flussmittel und UTP 1-Legierung verwendet. Die Methode ist optimal, wenn Dienstprogramme in der Wasserversorgung gekocht werden. Flussmittel sind nicht gesundheitsschädlich, da sie sich in der aquatischen Umwelt vollständig auflösen, ohne dass sich schädliche Verbindungen bilden.
Wie man verzinkte Rohre mit Flussmittel kocht
Die Kanten der Rohre werden vor dem Anschließen entfettet und bis zu einem metallischen Glanz gereinigt. Die Reinigung sollte nicht nur außen, sondern auch innen erfolgen. Die Vorformlinge sind auf jeder Seite der geplanten Verbindung 20 bis 30 cm lang vorgewärmt. Für ein effizientes Schweißen von Produkten mit Wandstärken bis zu 3 mm ist keine spezielle Kantenvorbereitung erforderlich. Die Breite des Spaltes zwischen den Enden beträgt 2-3 mm. Bei dickeren Rohren werden ein Öffnungswinkel von 80-90 Grad und eine Stumpfhöhe von 1-1,5 mm durchgeführt. Die Spaltbreite ist ähnlich.
Das Flussmittel wird auf ein Medium zwischen flüssig und fest erhitzt und in einer dicken Schicht auf die Oberfläche der Verbindung aufgetragen. Die Menge des verwendeten Materials ist doppelt so groß wie beim Schweißen gewöhnlicher Stahlprodukte. Der Zweck des Flussmittels besteht darin, dem Schweißgerät überschüssige Wärme zu entziehen, wodurch das Verdampfen von Zink von den Kanten verhindert wird.
Beim Erhitzen ändert das Flussmittel seine Farbe von gelb nach weiß, und wenn die Verbindung die Löttemperatur erreicht, wandelt sie sich in transparent um. Somit kann der Zustand des Flussmittels die Zeit bestimmen, zu der mit dem Löten begonnen werden soll.
Wenn Sie die Größe der Düse des Brenners zum Löten auswählen, müssen Sie von der Wandstärke des verzinkten Produkts ausgehen. Das Größenverhältnis ist in Tabelle Nr. 1 gezeigt.
Tabelle 1
Düsengröße mm | Verzinktes Rohr |
1 -2 | Durchmesser bis 250 mm, Wandstärke 2-6 mm. Füllnähte in Produkten jeglicher Art |
2-4 | Durchmesser über 250 mm und Dicke über 2-6 mm |
Beim Löten von Verzinkungen gilt die Regel: Die Düse des Brenners sollte eine Nummer kleiner sein als beim Verbinden eines herkömmlichen Stahlrohrs mit ähnlichen Abmessungen.
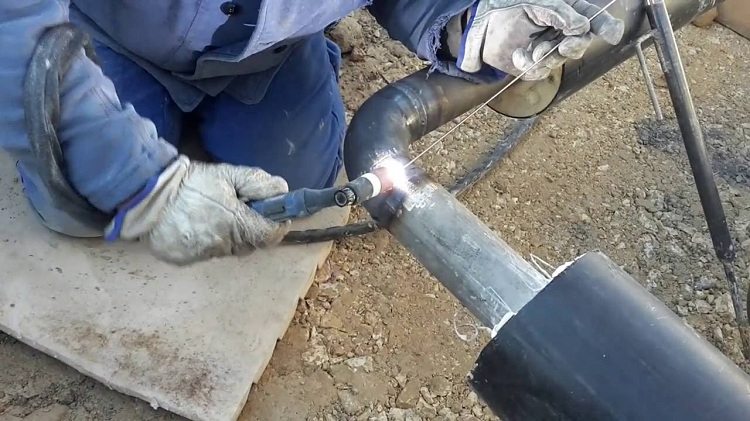
Für das hochwertige Schweißen eines verzinkten Rohrs ist es äußerst wichtig, einen Brenner der entsprechenden Größe zu wählen und die Flamme richtig einzustellen
Warum ist es wichtig, die richtige Düse zu wählen? Bei Verwendung einer zu großen Version wird das Werkstück überhitzt und das Zink verdunstet. Dies bedeutet, dass sich seine Korrosionsbeständigkeit und Festigkeitseigenschaften verschlechtern (geschmolzenes Zink führt zur Bildung von Poren). Wenn die Düse nicht groß genug ist, erwärmt sich die Metalloberfläche nicht auf die erforderliche Temperatur, wodurch das Lot daran haftet.
Während des Lötens wird eine Acetylen-Sauerstoff-Flamme verwendet, die überschüssigem Sauerstoff ausgesetzt ist. Ein Überschuss an Sauerstoff ist notwendig, damit beim Schmelzen des Lots durch Oxidation mit Silizium dessen Oxid entsteht. Es ist Siliziumoxid, das die thermische Verdampfung von Zink verhindert.
Wichtig! Es ist notwendig, die Stabilität der Flamme des Brenners einzustellen und sicherzustellen. Die Wärme sollte auf die Kanten und den Spalt zwischen den Werkstücken konzentriert werden. Eine instabile Flamme führt zu einer Überhitzung des Rohrabschnitts in der Nähe der Verbindung.
Zum Schweißen mit einem Gasbrenner verwenden Sie am besten die "linke" Technik, dh platzieren Sie die Stange vor der Flamme. In diesem Fall fällt das Feuer auf die Lötstange und nicht auf die Metalloberfläche. Bei der Durchführung einer Umschmelznaht sollte der Brenner in einem Winkel von 70-75 ° geneigt werden. Für den Fülldurchgang sollte der Winkel 15-30º betragen. Der Brenner kann in jeder räumlichen Position positioniert werden, am bequemsten ist jedoch die untere, und es ist zweckmäßig, das Schweißbad damit zu überwachen. Das Verbinden von Rohren mit einer Dicke von bis zu 4 mm erfolgt in einem Durchgang. Wenn der Dickenwert höher ist, wird Mehrfachdurchlaufschweißen verwendet.
Nach Abschluss der Verbindung wird die Schweißverbindung von überschüssigem Lötmaterial gereinigt. Draußen wird das Rohr mit Wasser gewaschen und mit einer Drahtbürste gehalten. Es ist wichtig, es nicht zu übertreiben, um die Zinkoberfläche nicht zu beschädigen. Die Innenschale muss einen Tag lang mit Wasser gefüllt und gespült werden.
Durch ordnungsgemäßes Löten von verzinkten Rohren erhalten Sie Verbindungsnähte, die keinen zusätzlichen Korrosionsschutz erfordern.
Manuelles Lichtbogenschweißen von verzinkten Rohren
Durch Verringern der Schweißgeschwindigkeit und Erhöhen des Stroms wird die Bildung von Poren in den Kehlnähten vermieden.Die Verwendung spezieller Elektroden kann solche Bedingungen bereitstellen. Je nach Stahlsorte ist es besonders wichtig, die richtige Wahl für das Garen eines verzinkten Rohrs zu treffen. Wenn Sie verzinkte Carbonrohlinge durch manuelles Lichtbogenschweißen verbinden, müssen Sie an den mit Rutil beschichteten Elektroden anhalten. Für niedriglegierte Stähle können basisch beschichtete Elektroden verwendet werden. Rutilelektroden haben mehrere Vorteile:
- Die Elektrode enthält Titanoxid, mit dem Sie den Lichtbogen sowohl zum ersten Mal als auch wiederholt schnell und einfach entzünden können.
- Der resultierende Schweißlichtbogen liefert hochwertige, dichte Schweißnähte ohne Risse mit hoher Dauerfestigkeit.
- Der Verlust von verschmolzenem Material durch Spritzer ist minimal.
Die Rutilbeschichtung der Elektrode kann etwas Eisenpulver enthalten. Auf diese Weise können Sie das spezifische Gewicht von Kohlenstoff in der Zinkschicht verringern und die Rissbeständigkeit erhöhen.
Das elektrische Schweißen von verzinkten Profilrohren erfordert mindestens minimale Erfahrung mit dem Schweißer. Neben der Beschichtung der Elektrode ist deren Dicke von großer Bedeutung. Die Lichtbogenleistung hängt direkt von der Größe der Elektrode ab. Die Wahl einer zu dicken Elektrode kann zu Verbrennungen und zu dünnen bis schwachen Festigkeitseigenschaften der Verbindung führen. Die häufigste Wandstärke von Profilprodukten beträgt 1,5 bis 5 mm. Wählen Sie daher eine Elektrode mit einem Durchmesser von 2 oder 3 mm.
Beim Schweißprozess ist die Bewegungsgeschwindigkeit der Elektrode durch das Metall von besonderer Bedeutung. Bei einem langsamen Tempo besteht die Gefahr, dass das Rohr verbrannt wird. Ein zu schnelles Tempo liefert nicht die erforderliche Qualität der Verbindungsnaht. Während des Trainings wird eine geeignete Geschwindigkeit entwickelt.
Beachten Sie! Nach dem Schweißen müssen die Verbindung und die Wärmeeinflusszone mit einer Korrosionsschutzmasse behandelt werden.
Das Schutzmittel sollte folgende Eigenschaften haben:
- hohe Haftung an der Metalloberfläche;
- Korrosionsbeständigkeit auf Zinkniveau;
- Einfache Anwendung ohne teure High-Tech-Geräte.
Als Schutzschicht hat Farbe, die mindestens 94% Zinkstaub enthält, gut funktioniert. Für die Herstellung werden nicht verseifbare synthetische Bindemittel verwendet, daher wird es auf vertikalen Oberflächen gehalten und ist leicht aufzutragen.
Eine andere Möglichkeit, die Oberfläche wiederherzustellen, besteht darin, 99,99% Zinkdraht mit 99,99% Zink zu beschichten. Für diese Rolle eignen sich auch Zink-Cadmium-Stäbe.
Alternative Methoden zum Verbinden von verzinkten Rohren
Das thermische verzinkungsfreie Verzinken kann durch Gewindeschneiden verbunden werden. Aufgrund der Komplexität der Anwendung wird es nur bei Rohren mit kleinem Durchmesser verwendet. Der negative Punkt einer solchen Verbindung sind die im Vergleich zum herkömmlichen Schweißen hohen Arbeitskosten. Es ist auch erwähnenswert, dass an der Verbindungsstelle während des Schneidvorgangs die Zinkschicht beschädigt wird. Folglich ist das Rohr an der Verbindungsstelle anfälliger für Korrosion.
In der Wasserversorgung, Wärmeversorgung und anderen technischen Netzwerken können werkseitig geschweißte Systeme verwendet werden, die nach dem Prinzip des Konstrukteurs zusammengebaut werden. Ein werkseitig hergestelltes Kit enthält eine Hülse mit einer Dichtung, die an den Rändern des Rohrs mit einer Nut verschraubt wird. Diese Methode ist für die GUS-Länder recht neu. Ihre Hauptvorteile sind hohe Installationsgeschwindigkeit und zuverlässige Verbindungen.
Zusammenfassend stellen wir fest, dass mit einer Schweißverbindung hochwertige Nähte unter strikter Einhaltung aller Regeln möglich sind. Zunächst sollte eine Überhitzung und Verdunstung von Zink verhindert werden, was nur mit speziellen Rutilelektroden und Flussmitteln möglich ist. Die Qualifikationen des Schweißers spielen sowohl beim Lichtbogen- als auch beim Gasschweißen eine große Rolle. Andere Rohrmethoden sind aufgrund der niedrigsten Schweißkosten nicht so beliebt.