The finned tubes are provided with metal ribs, so that their outer surface increases. This leads to an increase in heat transfer efficiency by one and a half times. Finned products are used in industry and in everyday life. They are used to equip heat exchangers and coolers, heating systems, industrial refrigerators, metal communications.
Content
Device and applications of ribbed pipes
Finned tubes are monometallic or bimetallic structures, consisting of two elements:
- Inner pipe. This is a supporting element, along the inner cavity of which the working medium moves. They make it from metal, most often from steel. Cast iron and non-ferrous metals are used much less frequently. The material from which the internal part of the structure is made, is resistant to temperature extremes and high pressure, anti-corrosion properties.
- Outer ribs. They can also be made of steel, cast iron and non-ferrous metals. The outer ribs efficiently transfer heat from the carrier element.
Finned tubes are used in various fields of human activity:
- the engineering industry uses them in refrigeration units, oil coolers and compressors;
- chemical, oil refining and petrochemical - in condensers, gas heaters and gas coolers;
- nuclear energy - in gas coolers, intercoolers, steam air heaters, drying towers;
- in equipment for air conditioning;
- in heat exchange units.
Production and characteristics of finned tubes
The method of production of products depends on their purpose and related technical characteristics.
Basically, a fully automated spiral fin is used, in which a spiral welded with a continuous seam passes around the inner pipe. It can be carried out in three ways:
- Knurled.
- Aluminum wound.
- Welding with welding.
Further processing is not required, the product has the following features:
- half-increased heat transfer coefficient;
- increased resistance to stress;
- preservation of the specified characteristics with increasing pressure, temperature differences and other sudden changes in operating conditions;
- increasing the productivity of the equipment that was equipped with it.
Important! Spiral fins can reduce pipe consumption while reducing the weight of heat exchangers.
Coating a pre-defatted finned tube with magnesium oxide and subsequent annealing allows it to be given a heat-resistant coating. Such products have:
- more than one and a half times increased heat transfer coefficient;
- increased resistance to various corrosion;
- increased productivity;
- long service life;
- increased resistance to pressure and temperature drops;
- the possibility of use in aggressive environments.
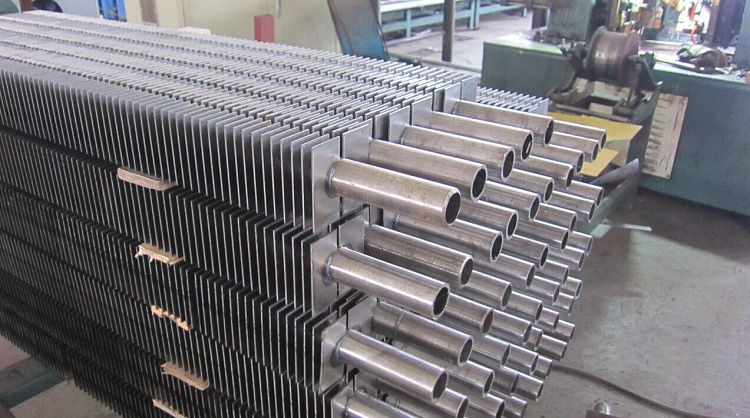
The method of production of pipes, the shape of the ribs and the method of their fastening are reflected in the technical characteristics of the products and determine the scope of application
Advantages of using heat-resistant finned tubes
Heat-resistant finned products obtained as a result of the use of new technologies have a number of advantages that have made them widespread. They differ:
- high manufacturability. The use of resistance welding does not require a large amount of energy, nor special consumables, nor sophisticated equipment;
- increased intensity of convective heat transfer. In the space of the intercostal canals, turbulization of the flow of the working medium takes place, and all sections of the fins work equally well;
- excellent thermal contact between the structural member and the ribs. The use of resistance welding made it possible to achieve an almost perfect thermal contact;
- lower thermal resistance to heat transfer. As the thickness of the condensate film decreased, the level of condensation of the vapors of the process fluid flowing through the pipeline decreased. This is due to the presence of heat-resistant coating.
Cast iron ribbed pipe
Technological progress has made possible the production of ribbed cast iron structures. This allowed the use of cast iron finned heating pipes. After all, heating systems are literally an ideal environment for using ribbed cast-iron products. They have the following advantages:
- high resistance to corrosion caused by both the action of the working fluid from the inside and the external environment;
- ease of installation;
- high heat transfer coefficient;
- compactness;
- low cost.
Ribbed cast iron products are not without flaws. They are:
- tend to accumulate poorly cleaned dust between ribs;
- weigh a lot;
- brittle under mechanical stress.
Note! The listed disadvantages make it possible to use ribbed cast-iron pipes to create heating registers in industrial and warehouse premises.
Ribbed cast-iron pipes are specially made for the registers in the form of hollow radiators, sometimes equipped with connecting threads or flanges at the edges to ensure alignment with other elements of the heating system.
And cast-iron radiators for residential premises continue to be in high demand, as they withstand temperatures of one and a half hundred degrees. In the design of heating systems, a cast-iron starting pipe is often built in. Thanks to this, the heating furnace warms up the surrounding area faster.
Pig-iron economizer pipe
In the production of industrial heat exchangers, ribbed cast-iron pipes are simply irreplaceable. For industrial registers (economizers), cast-iron pipes with ribbed walls are available with either round ribs or rectangular shapes. The inner diameter is seventy millimeters, the outer is 175 mm. The large difference between the values of the inner and outer diameters allows you to get a relatively low temperature on the surface, despite the fact that the coolant will be very hot.
Economized cast iron pipes go on sale two or three meters long. They are equipped with two blind plugs and two plugs with holes - left-sided (marked as “L”) and right-sided. The inconvenience associated with the transportation of heavy and weakly resistant to mechanical damage economizer cast-iron structures more than pays for their proper operation. Using economizer elements, it is recommended:
- to expose the mounted structures to a minimum external impact;
- avoid exceeding the temperature of the coolant. Economizer pipes are able to withstand short-term heating of the coolant to a half hundred degrees, but it is advisable not to raise the temperature above 95º C;
- apply a constant working pressure of six to ten atmospheres. Although it is possible to connect to steam boilers with a working pressure of up to 24 atm;
- coat the outer surface with a special primer;
- making installation, pay attention to the fact that the distance from the middle axis of the register to the side wall is more than 130 mm, and to the floor - more than two hundred millimeters;
- By setting the registers in two rows and connecting them together using a special arc, they maintain a distance between the median axes of 250 mm.
Adhering to the rules of operation, it is possible to achieve the most efficient functioning of economical cast-iron pipes.
Casting iron pipes
Since the external sewer networks are made mainly of cast iron, it is impossible to do without carrying out caulking and caulking. Caulking is carried out during the assembly of a system including cast-iron pipes to seal gaps arising at the place where the transition to another cast-iron pipe is made. It is produced using:
- Resin compactor and cement mortar.
- A slightly moistened mixture of cement and asbestos fiber.
- Gray fill.
Important! Making caulking, the pipes are gently tapped with a hammer so that the bell moves freely.
If it was not possible to release the bell, then a gray fill was applied. They carefully burn it out, always wearing a respirator. Having released the bell, it is thoroughly cleaned. A seal ring coated with special grease is inserted into the socket, and a new part is inserted into it.