The classic floor heating is a concrete layer with integrated heating pipes. It provides the highest level of aesthetics and comfort compared to other types of heating in a private house. When arranging such a system, in addition to knowing the fundamentals of the design, it is also important which pipe to choose for a warm floor. There are different options, so knowing the nuances will help you make the most rational decision.
Content
The principle of operation of space heating systems
The main type of heat transfer when heating a working or residential building with traditional systems (fan coil units, convectors and radiators) is convection. From the heating element, warm air rises to the ceiling. As it cools, it goes down, where it is drawn into the radiator. Next, the cycle repeats.
Note! With such a heating system, the air temperature at the floor level is lower than that of the ceiling. Such a temperature distribution creates an unsatisfactory state of comfort, because it does not meet the physiological requirements of a person.
Underfloor heating systems, namely the pipes underlying them, do not create convection. The air warms up over the entire surface and is warmer below than at the ceiling. Another difference from radiator heating is the low temperature of the coolant. Heat flow 0.04-0.15 kW with 1 m2 the area can be obtained at a coolant temperature of about 30-50 degrees.
The benefits of underfloor heating
The pipes used to install underfloor heating may be of various materials. In any case, a properly organized system has these important advantages compared to traditional ones:
- increased comfort;
- lack of dust circulation;
- hygiene;
- safety;
- convenience;
- modernity;
- profitability;
- durability.
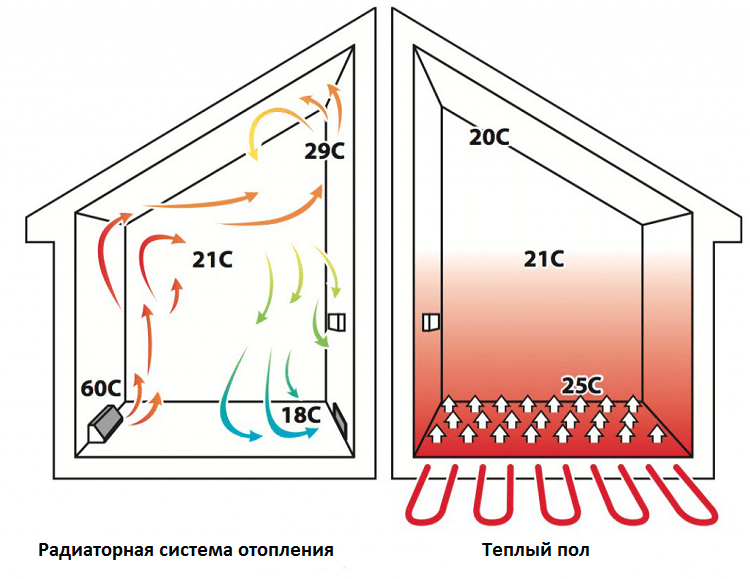
The underfloor heating system contributes to a more uniform heating of the room and savings on the coolant
Comfort is provided by the emission of thermal energy, which contributes to uniform heating of the room. Since the floor is constantly dry, there is no formation of mold, and nutrient media for dust mites and bacteria are also destroyed. At the same time, air retains a natural level of humidity.
Using such systems, those rooms that are characterized by increased requirements for cleanliness (for example, in medicine, the food industry, in highly clean industries and others) can be quickly and conveniently disinfected and washed. An important advantage is the lack of the possibility of getting bruises, burns or scratches as when touching a convector or radiator, since the pipes of the heated floors are hidden.
The system is characterized by the effect of self-regulation - determining the amount of energy supplied depending on the difference in air temperature in the room and the floor surface. Energy savings of up to 20-30 percent.
Pipes for underfloor heating
To date, such pipes for underfloor heating are available:
- copper;
- from metal plastic;
- polypropylene;
- made of cross-linked polyethylene.
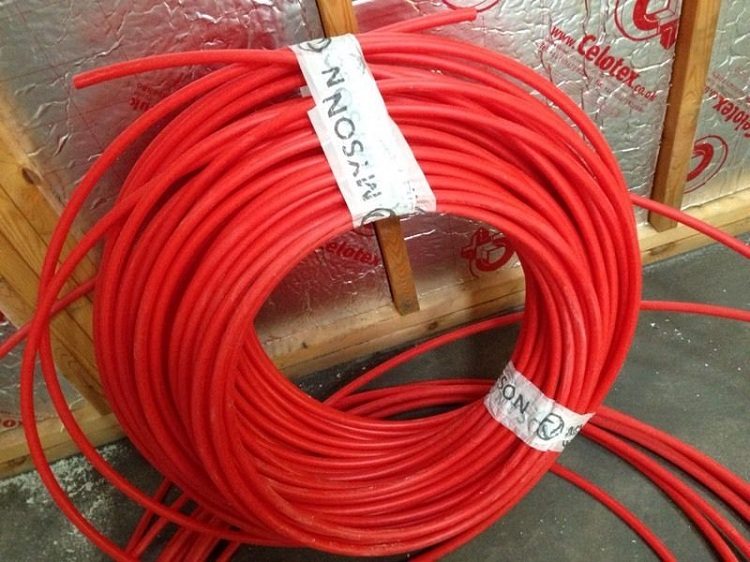
The most popular type of pipe for installing underfloor heating is cross-linked polyethylene products
The first type of pipes for underfloor heating is one of the best. Copper has excellent durability and thermal conductivity. The only, but very significant drawback is the price. Not only the cost of the products, but also their installation, are quite expensive, since it requires the use of special equipment.
Pipe for underfloor heating is the most common option. Of all the advantages that the system provides - balance, performance due to high efficiency and durability.
The aluminum layer of a metal-plastic pipe for a warm floor gives the product good thermal conductivity, and thanks to the inner and outer polymer layer, the product is resistant to overgrowing and damage. In addition, the material is quite affordable.
Pipes for underfloor heating made of polypropylene are rare.
Note! A significant drawback of products is a very large bend radius (at least eight diameters).
The latter type of pipe has a fairly good wear resistance, thermal conductivity and affordability. During installation, rigid fixing of the elements is required, otherwise the pipes will be unbent.
Varieties of systems
The determination of which pipes are needed for a warm floor is affected by the choice of its type. Thus, a concrete, light and thin version of the system device is distinguished. The first type is laid on very strong load-bearing floors (for example, reinforced concrete). In this case, the pipes for the warm floor are covered with a sand-cement screed, which ensures maximum heat transfer and comfort. This design is attractive with good performance and low cost.
A light floor is divided into wooden or polystyrene. It has a minimum load on the floors, while the weight of a concrete system with a screed thickness of 50 mm is 250-300 kg / m2. The main field of application of the light floor is wooden housing construction.
Particularly interesting are thin warm floors, pipes on which small diameters are selected. The height of the entire structure is 2.4 cm.
Pipe layout rules
When planning the layout of pipes, it is necessary to take into account such nuances:
- It is not rational to stack products at a distance of less than 10 cm from each other;
- more dense laying of pipes allows to obtain higher thermal power;
- the maximum permissible distance between the pipes is 25 centimeters;
- the indentation of heating products from the outer walls - not less than 15 centimeters;
- it is forbidden to lay pipes at the joints of floor slabs.
To ensure the given efficiency, the laying of heating pipes near the outer walls should be more dense than in the middle of the room. In the event of a wiring at the joint of the plates, it is recommended that two circuits be executed on its different sides. At its intersection, a metal sleeve 3 cm long is used.
Note! The maximum allowable length of the contour (loop) of a pipe with a diameter of 16 mm is 80 m, and 20 mm is 120 m. Exceeding these values leads to a high value of hydraulic losses.
The shape of the heating contours is meander (snake, zigzag) and bifilar (spiral, snail). The serpentine shape of the pipe installation leads to uneven distribution of heat. You can solve the problem either by increasing the power of the pump, or by laying loops with a double snake. The shape of the cochlea involves the alternation of return and supply pipes. This creates the same temperature background.
Fixing pipes with mounting rails
The easiest way to fix heating pipes is to use anchor brackets. This fixation has two drawbacks:
- Loss of some part of the heating surface by the pipe and, as a result, heat transfer.
- The absence of guides and marks makes it difficult to lay products with a certain step.
It is more technologically advanced to fasten pipes using fixing tires (fixing strips, mounting rails, fixing tracks, etc.). Such elements specify the step of laying products and raise them above the insulation to a height of 2 to 5 mm. Thus, the screed covers the entire area of the heating surface.
Usually the straps are 2 meters long, and the latches are arranged in increments of 5 cm. They have notches that allow you to shorten the part to the required size without the use of a tool.
Fastening to thermal insulation can be performed in various ways. When using foil foam, on which there is a metallized waterproofing film, it is enough to apply an adhesive layer on it. Otherwise, U-shaped brackets are set. There are special holes on the tires for them. Mounting rails are fixed to the floors by dowels.
Checking system build quality
Before pouring concrete screeds, the pipes are crimped. At this point, a distribution manifold for underfloor heating must be installed, and all heating circuits must be connected to it. Further, each of the circuits individually is filled with water until all the air is expelled.
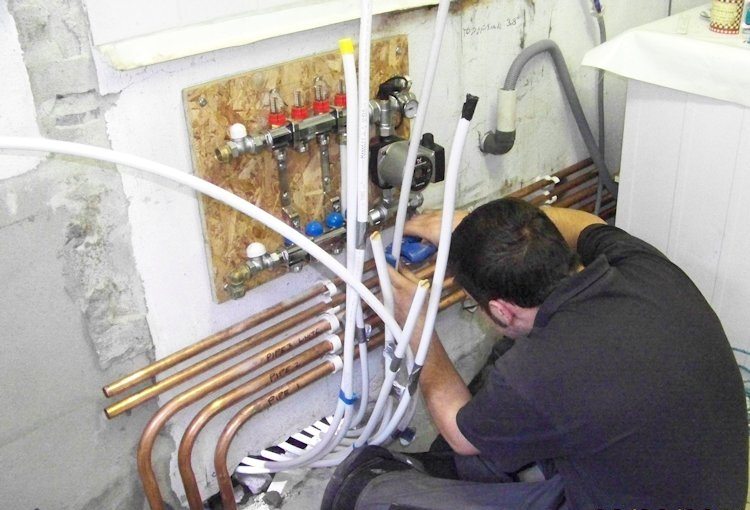
All contours of the future system are reduced to a collector; it is mounted after the pipes are fixed to the floor
Note! For the entire crimping period and when filling the system, automatic air exhausters must be closed, since debris and dust from the exhaust air can damage them.
If the warm floor is assembled on the basis of metal-plastic pipes, then the pressure test is performed for 1 day with cold water with a pressure of 6 bar. If the pressure value remains constant, the test is considered to have passed the test. Filled pipes can be poured with concrete.
If the system is assembled from pipes made of cross-linked polyethylene, then it is loaded with a pressure that is 2 times higher than the working one, however, not less than 6 bar. At the same time, its value begins to fall. After 30 minutes, the pressure should be restored. The procedure is carried out 3 times, and after the last resume, the system is left for a day. The test is considered successful if, after 24 hours, the pressure drop is not more than 1.5 bar and there are no leaks.
Whatever pipe is used for the underfloor heating, a system check can be performed at the maximum operating temperature. To do this, you need to warm it up to 80-85 degrees for half an hour. The procedure is applicable after cold water pressure testing.
Some features of light warm floors
For the supporting layer of a light warm floor, sheets of polystyrene plates or strips of chipboard (or wood) are used. Heat-separating plates of metal are laid on the base, which have grooves for laying heating pipes. The supporting final layer is made of gypsum fiber sheets (GVL).
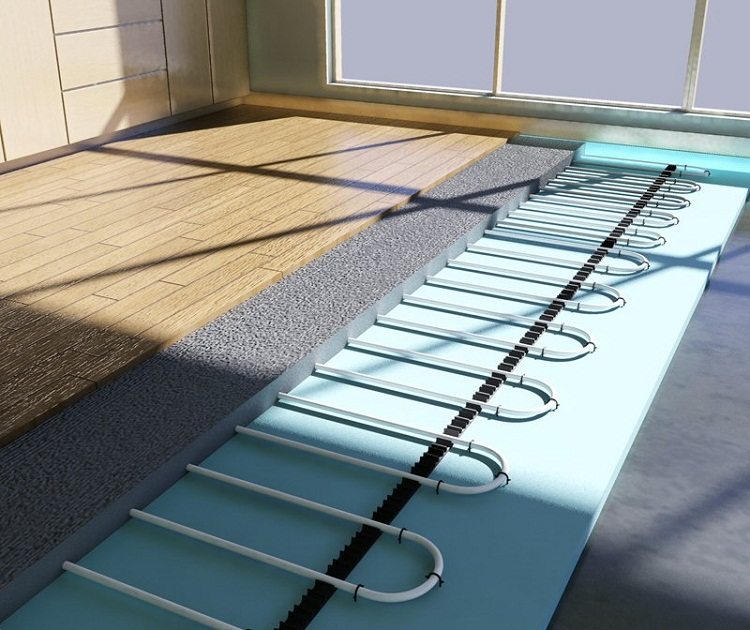
For laying the "light" floor there is no need to use a cement screed: the pipes are covered with ready-made slabs of artificial materials
The advantages of the system are:
- fineness: from 3.5 to 6.0 cm;
- lightness: up to 30 thousand g / m2;
- speed: no need to wait for the screed to solidify;
- lack of labor for pouring concrete;
- the ability to install in temporary rooms;
- ease of assembly / disassembly.
Similar systems find application in:
- reconstruction (when it is necessary to lay a new coating on the old one);
- limited height of the premises;
- critical deadlines for installation work;
- inaccessibility of installation sites for concrete delivery;
- restrictions on the loads on existing floors.
Consumers still prefer the traditional concrete screed floor because lightweight systems are characterized by low heat dissipation and high installation costs.
So, the heat transfer indicators do not exceed 50-60 W / m2. In most cases, this is not enough to fully heat the room. Only the floor remains warm, and the heating function must be shifted to another source. In addition, the installation of the system requires the possession of certain skills, which leads to a costlier process.
Underfloor heating is today a fairly common method of heating a house. From which pipes are used for its device depends on the durability, efficiency and effectiveness of the system.