A chimney is an important part of a cottage or a country house. Smoke ducts contribute to the removal of toxic gases from the heating system and provide home safety from fire. Thanks to high-quality and properly designed chimneys, it is also possible to reduce the amount of fuel consumed in the system. Chimneys are very popular with buyers, respectively, and the scope of their production is widely developed.
Content
- 1 Organization of production of stainless steel chimneys
- 2 Cutting equipment: selection criteria
- 3 Machines for rolling stiffeners for steel products
- 4 Stainless Steel Folding Machines
- 5 Mobile bending machine for the production of stainless steel products
- 6 Electromechanical or manual folding machines
- 7 Resistance spot welding machine
Organization of production of stainless steel chimneys
The first thing to do when organizing a release company chimneys for boilers and different types of furnaces - selection of the optimal working room that meets the basic technical standards.
One of the main criteria for choosing a room will be its area - at least 50 square meters. In such a workshop, it is possible to install a basic amount of the necessary equipment and place jobs. The minimum air temperature in the workshops will be +18 degrees, the presence of sewage and water supply is mandatory.
Typically, the production of flue gas exhaust systems involves the manufacture of ventilation ducts or ducts. Therefore, the technical equipment for these types of industries will be identical.
So, the production of chimneys is possible with the following equipment:
- machine for cutting metal;
- equipment for rolling stiffeners;
- folder rolling machine;
- mobile walk-through bending machine;
- folding machine;
- equipment for welding.
Chimneys can be connected by means of corrugated elbows, and if such a possibility is provided for in production, a machine will be needed to manufacture these stainless steel parts. They are available in automatic and semi-automatic formats. When using the latter option, the worker must manually reinstall the corrugation blank and reboot the machine.
Next, we will consider factors that may affect the choice of an entrepreneur in the purchase of each piece of equipment.
Cutting equipment: selection criteria
In the manufacture of stainless steel products, both guillotines and laser machines are used for cutting. For small enterprises, manual guillotines are the best choice - their price is acceptable, and the dimensions allow you to install equipment in limited areas.
Manual guillotines do not require an electrical connection, but operate at the expense of the physical strength of the employee.
Important! The manual unit is not quite suitable for not too thin sheets of metal (from 1.5 mm), since often the force does not allow an even cutting.
This disadvantage is not observed in other relatively low-cost guillotine models equipped with a pneumatic drive. Their operation is possible only in rooms with a pneumatic line.If the production of chimneys reaches a mass level, there is a need for mechanical guillotines. Units with an electric drive work seamlessly with sheets up to 10 mm thick, while hydraulic units are designed for cutting even thicker metal plates.
Mechanically driven guillotines usually have several functions that greatly simplify the cutting process:
- support complex;
- automatic conveyor accepting waste products;
- control of hydraulic clamps.
The productivity of all the listed types of guillotines is the same - about 5 sheets per hour. Only the thickness of the workpiece varies.
Machines for rolling stiffeners for steel products
To strengthen chimneys and ducts, as well as parts for them, machine tools for applying stiffeners are used. By bending the walls of the seal are applied in the transverse direction, observing a given step (usually 20-30 cm).
The machine consists of two main parts that ensure smooth profiling: from a welded bed and rollers with rollers (forming device). Knurling of the set number of stiffeners is carried out simultaneously along the entire length. The machine can apply as many stiffening ribs as there are pairs of rollers installed in it.
The peculiarity of this unit is that during profiling the main product is not deformed.
Stainless Steel Folding Machines
Folding is considered a more economical way to obtain metal compounds than welding, and more effective than gluing.
The main purpose of this equipment for the production of chimneys from stainless steel is a perfectly smooth matching of product segments. Folding machine allows you to create single, double and other compounds. The principle of operation of the device is as follows: the forming device stretches a sheet of metal along the machine, forcing double folds, with the help of which a strong locking connection of the elements will be ensured.
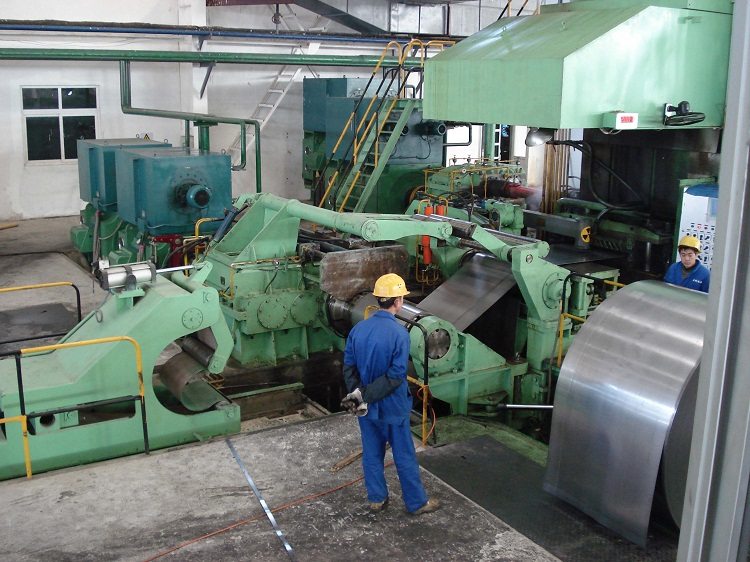
Using a folding machine, a more reliable and economical option for connecting pipe segments to each other is obtained
When choosing folding machines, as well as other units, one should rely on indicators of the thickness of the stainless steel sheet that is acceptable for processing. Easy to maintain and operate mobile devices. Some of them are able to change the configuration of rollers for profiling, forming up to 5-6 varieties of folds. There are also models that include the function of creating connectors and rails. The cost will depend on the number of operations performed by the machine.
Important! The folding equipment includes interchangeable rollers, sometimes allowing you to create additional types of folds.
Manual folding machines mainly work with thin sheets of stainless steel, up to 0.7, and are only suitable for forming folds on downpipes. More powerful models work with almost all types of metal, including copper and galvanized steel.
For bending the fold, folding bending machines are used. Choosing between manual control and an electric drive, it is worth stopping at the latter. The productivity of electric folding machines is 2 times higher than the capabilities of manual ones: 50 elements per hour with manual control and 100 parts with an electric drive. During a shift, the electric folding tool allows you to produce up to 1000 steel billets.
Mobile bending machine for the production of stainless steel products
The listogib choice will be based on the following principles:
1. The equipment must have a power reserve. So that the machine does not become unusable quickly, and during the production process there are no unexpected failures, the equipment should be able to process metal sheets 30-50% thicker than expected.
2. The budget for the acquisition of the unit. The cost of equipment will depend on the listogib category. These devices are divided into three large groups:
- manual bending machines;
- electromechanical;
- hydraulic.
The category of manual bending machines includes all equipment that does not have a mechanical drive. In turn, hand held have several more subgroups: they are stationary and mobile. For chimneys and ducts, walk-through mobile manual bending machines are suitable. Some manual pipe benders have cutting knives that allow the machine to perform two functions: bending and metal cutting.
Hydraulic and electromechanical machines have a significantly higher cost, but only with their help it is possible to establish large-scale production. The simplest equipment in this category is suitable for thin-walled products (up to 1.5 mm, with a minimum chimney thickness of 1 mm), and machines with powerful hydraulics can process sheet metal with a thickness of up to 20 mm. Equipment with electric and hydraulic drive is sometimes equipped with a set of programs - CNC. For small enterprises, the cost of such machines will be too high (from 18,000 cu), and more qualified personnel will have to be involved in working with mechanical equipment.
For those who are looking for the most budget option for the manufacture of chimneys or other types of pipes, it is worth paying attention to sheet bending machines of Russian or Chinese production.
Electromechanical or manual folding machines
The folding machine is designed for upsetting the fold in the manufacture of hollow cylindrical parts of air ducts. Devices are both manual and electric. For the longevity of this equipment, it is important that the pressing rollers in the unit are made of hardened steel. Electromechanical models typically include a clamp level control system.
Folding machines are available in a wide range. The differences between them will be as follows:
- type of drive for moving the forming roller (manual, electric);
- installation method: mount to the floor or wall;
- the length of the upsetting fold;
- performance;
- cost.
For machines with the same length of the rebate lock, the performance is practically the same. Using this machine, it is possible to process about 50 parts per working hour.
Resistance spot welding machine
Sometimes enterprises prefer spot welding, which replaces folding or soldering. Electric current during welding heats the metal sheets, causing them to melt. Workpieces are compressed, connecting together at the molecular level. In butt welding, required when connecting stainless steel pipes and flues, current flows through the entire cross section of the elements being welded.
It is worth remembering that the production of chimneys also requires special software for the PC - this is necessary for more accurate product design. With the proper organization of the workshop, the availability of high-quality equipment and comfortable working conditions, it is possible to produce 400-450 finished products in one shift.