Steel bends are products that are used to change the direction of various pipelines. They are pipe segments bent at the right angle. They are performed, as a rule, on special pipe bending machines, and are mounted on the pipeline by butt welding. The operational field of these parts is incredibly wide, but most often they are used in the installation of oil, gas and water pipelines.
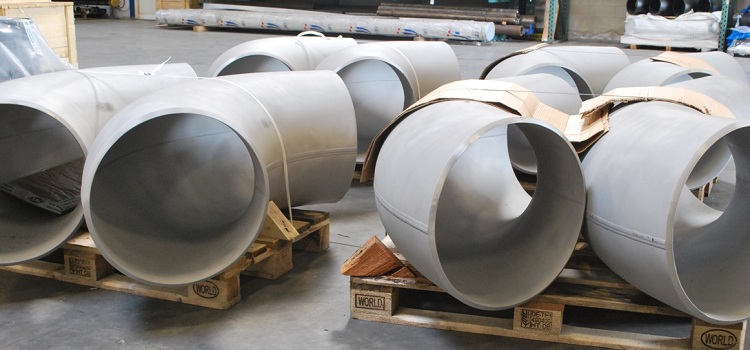
Branches for steel pipes are made of stainless steel, alloy steel, they can also have a protective zinc coating
Content
Scope of use of steel branches
Consider the main areas in which these products are operated:
- plumbing systems;
- heating communications;
- industrial highways for various purposes;
- oil and gas industry;
- chemical industry;
- pumping stations.
Such products are used in wiring communications for any purpose, however, not all of their types are suitable for certain pipelines. For example, for laying backbone networks, as a rule, they use steeply curved seamless, die-welded, as well as bent stainless steel products, alloyed, as well as galvanized elbows. This is due to the fact that such communications have large cross-sectional sizes and can operate at high pressure of the working medium.
Helpful information! Welded bends are used for various communications. The pressure in such pipelines does not exceed 2.5 MPa. Section indicators in such pipelines are usually greater than 1000 mm.
For household communications, steeply bent or bent varieties of bends are an excellent solution. And point products are very popular in the installation of pipelines in enterprises that produce various mineral fertilizers.
As mentioned above, such a product provides a rotation of the structure. Outlets are used not only in pipelines, but also in communications responsible for cleaning indoor air. The most popular in this case is the ventilation galvanized branch.
Benefits of Steel Bends
Pipe fittings are widely used in any installation, and steel turning parts are considered the foundation of any pipeline. Along with tees and transition elements, they play an important role in connecting communication and in increasing its strength.
Consider the main advantages of these products:
- with the help of these products a smooth rotation of the pipeline structure is made;
- characteristics of metal branches allow them to be used in difficult operating conditions - they have high strength characteristics, and can also be operated at high pressure;
- steel products are resistant to temperature fluctuations;
- the cost of such bends is quite affordable;
- have a high service life when used in aggressive industrial conditions.
The most popular models today are those that are bent at an angle of 45 and 90 °.
Materials
In order not to make a mistake when choosing a material, experts advise the operational features, as well as the type of working environment for which it will be used.
On sale you can find the following bends:
- carbon products;
- alloy parts;
- from stainless steel;
- elbows galvanized.
For general-purpose communications, parts made of carbon steel are perfect. If the working medium in the system is represented by aggressive chemicals, then in this case it is recommended to use stainless or alloy bends.
Alloy steel products can be used at temperatures from −60 to +40 ° C. The pressure that they can withstand reaches 7.4 MPa. They are often used in the installation of pipelines in cold climatic zones, as they have high resistance to corrosion at low temperatures.
Stainless steel bends are used in pipelines that transport hot media (water, steam), as well as chemically active substances with both alkaline and acidic environments. Stainless steel is highly resistant to the harmful effects of corrosion and therefore is excellent for such purposes.
Today galvanized bends are quite common. The material for such products is galvanized steel. Products made of galvanized steel are coated at the production stage with a protective anti-corrosion layer.
As a rule, this layer is represented by zinc, however, others can also act as protective elements (chromium, nickel, etc.). The galvanized steel outlet can carry a fairly high pressure and is resistant to aggressive environments.
Types of bends
The range of metal bends is incredibly wide, which is due to their design features and various fields of use. Consider the main types of these products:
- steeply curved;
- stamp welded;
- welded sectional;
- welded sector (segment);
- bent;
- point.
Steeply curved. All the main parameters of such products are described in the relevant documentation (GOST 17235–2001, GOST 17235–83). They are made by pulling a pipe. The broaching is carried out through a special form on pipe bending equipment, resulting in a high-quality part.
Steel bends for steeply bent pipes are usually made of carbon and stainless steel. The angle of the steeply bent branch can be: 30, 45, 60 and 90 °. The cross-sectional dimensions of such branches vary from 18 to 426 mm. The pressure to which such a tap is resistant is up to 16 MPa.
Stamped. Such parts are made of sheets by welding. This production method allows to obtain a thick-walled product with high strength characteristics. Stamped products can have cross-sectional sizes up to 1420 mm. They are exploited in the main communications of the oil and gas industry. Die-welded parts are made of alloyed or stainless steel and are regulated by technical specifications (TU).
Welded sectional. They are made from separate sections of pipes that are welded to each other, resulting in a finished part. The price of such bends is quite small, however, their strength and reliability indicators are less than other types. Made from carbon or low alloy steel. The cross-sectional indicators of such parts vary from 108 to 1620 mm.
Note! As a rule, welded sectional products are used in the installation of pipelines that have a small working pressure (up to 2.5 MPa). The temperature in such communications should not exceed +425 ° C.
Welded sector. Such bends are operated in pipelines that have a large cross-sectional size. Such communications have a certain angle of rotation of the flow of the working medium, which is transported under low pressure. The angle of such a product depends on operational features and can be: 30, 45, 60 and 90 °.
Chiseled. This type is performed from special cast billets on a lathe. It is worth noting that point products have the highest cost. This is due to the very complex manufacturing process.
Their main advantages are:
- are made with any indicator of wall thickness;
- resistant to high pressure (up to 100 MPa).
Bent. Such bends are usually used in cases where it is not possible to install a steeply curved version of the product on the pipeline. Bent parts do not have such a large bending radius as steeply bent, and are also equipped with a straight section. The angle of such products varies from 2 to 90 °. Their use is regulated by relevant documentation (GOST and TU). Bent bends are mounted in communications, the temperature of which ranges from −50 to +510 ° C.
Pressure indicators for such branches reach 100 MPa. Bending of such products is done on special pipe bending equipment. They can be bent both in cold and in a hot state.
Dimensions of steel bends
The angles of these products may be different, as well as the diameter dimensions, however, all products comply with certain standards. Standard angles are usually:
- 15°;
- 30°;
- 45°;
- 60°;
- 90°;
- 180°;
The mass of the part can also be different and depends on its diameter. This relationship is shown in the table below.
Table 1
Mm | Weight kg |
820 | 376 |
720 | 275 |
630 | 219 |
530 | 138–153 |
426 | 78–97 |
377 | 61–75 |
325 | 39–56 |
273 | 27–35 |
219 | 13–20 |
159 | 6,1–11 |
133 | 3,3–5,7 |
114 | 2,2–3,8 |
108 | 2,5–3,6 |
89 | 2,3 |
Part selection is based on the size of the pipeline. There are bends of various cross-sectional indicators (from 89 to 2000 mm). It is also worth noting that, if necessary, in production, you can make an individual order for the rotary element, which will differ in diameter or have a non-standard angle.
Branch Welding
The process of mounting the rotary element on the pipe is a rather difficult event and requires special skills in this area. Such welding is carried out only by specially trained welders.
Installation of an outlet to the pipeline is carried out in compliance with the necessary standards set out in the relevant instructions (for example, VSN – 006–89).
Important! Before starting welding work, make sure that the surfaces to be welded do not contain any defects. If flaws are found, they must be eliminated.
It is worth remembering that you need to control the displacement of the inner edges. There is a rule in this regard: when welding a pipe and an outlet with equal cross-sectional indicators, the displacement should not exceed 2 mm. Alignment of products is carried out using special devices - rotators.
In manual arc welding, the treatment of the first root seam is carried out by direct current. In case of a break, it is necessary to maintain the desired temperature at the weld site. After completing the first welding line and after grinding, proceed to the second seam. The time between these two events should not be more than 5 minutes. This is due to the fact that the second line should run along the unrefined root suture. After both lines are completed, filling grooves and facing seams are performed. The facing seam must protrude 1-3 mm above the surface of the pipeline.
Pipe rotator
At production facilities, welding of bends to pipes is carried out using special equipment. As a rule, these special equipment are rotators.The parts to be welded are clamped in the device and rotate around its axis, which makes it possible to perform high-quality welding of the elbow.
Consider the main advantages of using a rotator when welding a rotary product with a pipe:
- allow you to weld pipes with large diameters;
- the use of an autonomous drive rotator design allows you to adjust the speed of rotation of the part;
- provide exact alignment of pipes;
- can work not only with direct parts, but also with more complex, from a structural point of view, elements (for example, tees).
Today, there are many varieties of bends that can solve any problem when installing pipelines. At the same time, a wide range of these products requires specialists to study a large amount of information in order to know and comply with the features and rules of use of all such products.