Laying a gas pipeline is a rather complicated, from a technical point of view, process that should be carried out by specially trained people. Today, there are several ways to install gas pipelines. Gas pipelines themselves are classified according to some important parameters that are worth considering.
Content
- 1 Varieties of gas pipelines
- 2 Underground gas pipelines
- 3 Overhead gas pipelines
- 4 Laying of external and internal gas pipelines
- 5 Which way to choose: underground or aboveground?
- 6 Advantages of gas pipelines made of polyethylene
- 7 In which cases the use of polyethylene pipes is not allowed?
- 8 Stages of laying gas communications
Varieties of gas pipelines
Gas pipelines, as a rule, are divided into types according to two main indicators:
- location;
- pressure.
Consider what indicator of gas pressure these communications can have:
- low;
- middle;
- tall.
The maximum allowable gas pressure in a low pressure gas pipeline communication is up to 5 kPa. Structures with a maximum pressure of up to 0.3 MPa are classified as medium pressure gas pipelines. High pressure pipelines can withstand a maximum pressure of up to 1.2 MPa. High pressure communications are used to supply gas to large industrial enterprises or gas distribution facilities. Such designs are called trunk.
Pipelines with average pressure indicators supply gas to the gas distribution points of residential buildings. Low pressure communications deliver gas directly to consumers.
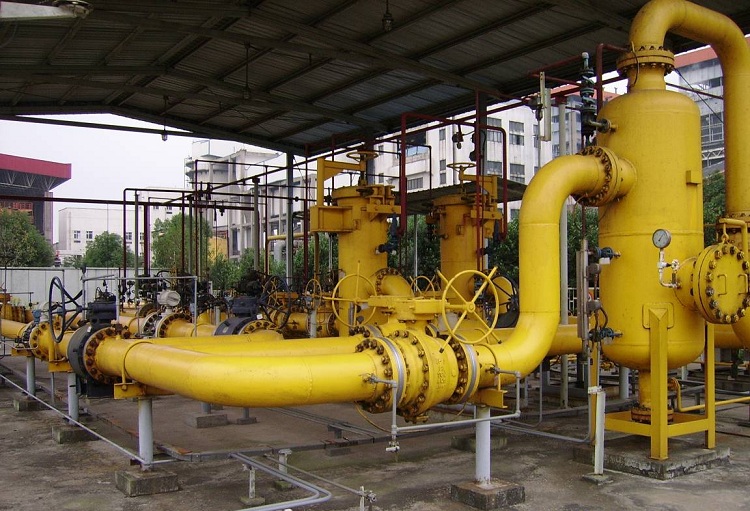
All gas pipelines have their own working pressure, its highest indicator - 1.2 MPa - is characteristic of a high pressure gas pipeline
And also all gas pipelines are classified according to their location on:
- laid underground (underground);
- mounted above ground method;
- outdoor;
- internal.
The installation of each of these types differs in its features and nuances.
Underground gas pipelines
As a rule, during the installation of the gas pipeline by the underground method, pipes are laid in pre-prepared channels (trenches). It is very important to remember that the depth of the communication wiring must correspond to the figure indicated in the project.
Today, the trenchless method of laying such structures is increasingly being used. For the trenchless method, equipment is used that performs horizontal directional drilling (HDD). This option is more budgetary and reduces the financial costs of gasification by 2.5–3 times. Consider the remaining advantages of this method:
- The HDD method allows to reduce not only the financial costs of arranging the gas pipeline, but also reduces the installation time;
- thanks to the HDD, there is no need to dig trenches, therefore, there is no need to violate the integrity of the roadway (if the pipe passes through the road), and the well can easily go around various obstacles, including existing pipelines.
Note! In addition, after laying gas pipelines using HDD, it is not necessary to restore green spaces.Therefore, we can conclude that this method is the most environmentally friendly.
After the preliminary (pilot) well has been equipped, its diameter is expanded to the required size. The walls of the well necessarily require strengthening. For these purposes, a special solution is used, after the solidification of which, gas pipes are pulled through the well.
In some cases, with HDD, a special case is used in which the pipeline is pulled. The case is used to protect the inner pipe from mechanical influences, as well as from stray currents in the soil. Protection against mechanical stress is necessary in cases where the gas pipe passes under the roadway or railway.
For good protective performance, steel pipes that have high strength values are used as a case. In addition, it is worth noting that the small cases are mounted when the gas pipe leaves the ground, as well as when it enters the building.
Overhead gas pipelines
The costs of installing the gas pipeline above the ground, as a rule, are much lower when compared with the underground option. In some cases, savings can reach 60%, which is undoubtedly a big plus. But pipes made in this way should have maximum protection against environmental influences.
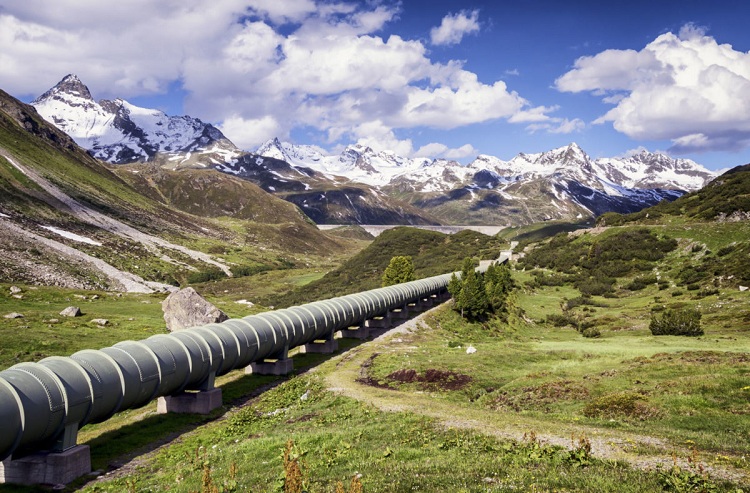
Construction of an onshore gas pipeline is a less costly method, although pipes require additional protection
Elevated gas pipelines must be equipped with insulation from temperature extremes, precipitation, etc. The type of protection is selected depending on the climatic conditions of a particular region.
In addition, such communications require constant security monitoring in order to exclude the possibility of unauthorized connection to the network. Based on all of the above factors, the reliability of such a pipeline is lower than that of a pipeline laid in the soil.
However, if the gas pipes pass above the ground in your area, which is well guarded, then this option is acceptable. It is also worth noting that such a gasket is popular in cases where it is not possible to lay pipes underground due to the dense communications network.
Laying of external and internal gas pipelines
Consider two options for the location of gas pipelines in relation to residential or industrial buildings:
Outer. Such laying, as a rule, is carried out in the courtyard of a private house or in the case when the pipe adjoins the facade of the building. The location of the gas pipeline communication by an external method should limit as much as possible access by unauthorized persons to it. For this, structural elements are located at a considerable height.
Fixing pipes to the facade of the building is a very important point. The fixing elements must be reliable in order to exclude the possibility of a gas pipe falling.
Important! Laying a gas pipe should be carried out only by highly qualified specialists. Installation is carried out in accordance with building codes and regulations (SNiP), as well as all the necessary technical documents.
Interior. Internal pipelines include all gas pipelines conducted directly inside buildings. There is one important rule that you need to remember: during the installation of gas pipelines, any decoration of pipes, as well as their location inside the walls, is excluded. This is due to the fact that such communication should be located so that it always has free access for routine inspections or repair activities.
Which way to choose: underground or aboveground?
The choice of laying method depends on the specific case, namely: on the characteristics of the soil, climatic conditions, built-up area, etc. Therefore, it is impossible to give an unambiguous answer to this question.
Consider the main tips for choosing a method of laying a gas pipeline:
- if the soil on the site has a high corrosion coefficient, then it is recommended to carry out the gas pipeline above the ground.
- if there is a high-voltage power line near the site where the installation will take place, pipes are laid by the underground method.
- if the gas pipeline is supposed to be installed in neighboring areas, then it must be done in an open way (above ground).
- in addition, if the gas pipeline is to be run through the autowork, it is advisable to choose a combined option for installing pipes. The combined version includes: underground laying under the canopy and above-ground on the territory of the site. Thus, an optimal solution to the problem is obtained.
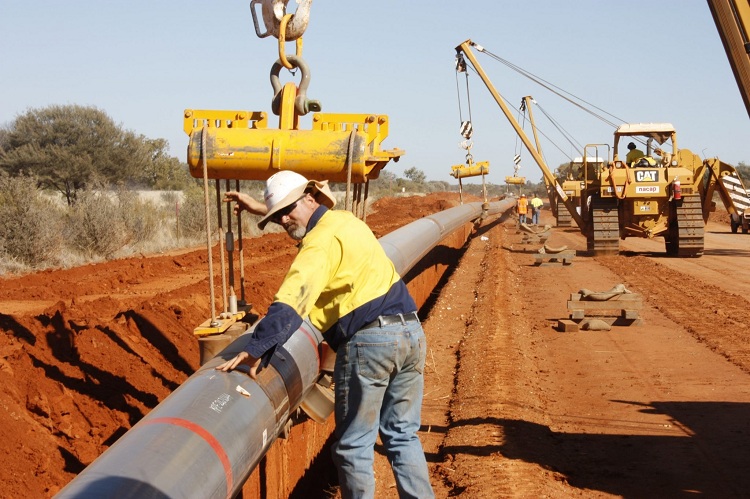
In most cases, an underground pipe laying method is used to protect the trunk from the effects of various negative factors
Depending on which of the gas pipeline installation methods will be carried out, pipes from various materials are used. There are two types of gas pipes according to the material of manufacture:
- steel;
- polyethylene (PE);
Steel pipes are versatile - they can be used for any installation (aboveground and underground), but modern plastic products are used for underground installation of gas pipelines. This is due to the fact that polyethylene has a weak resistance to ultraviolet radiation. Under the influence of ultraviolet rays, polyethylene loses its properties and collapses. However, it has a number of useful advantages, which are worth paying attention to.
Advantages of gas pipelines made of polyethylene
Polyethylene pipes for gasification are in great demand in the modern construction market. This is due to the fact that they have a number of advantages, in comparison with other analogues:
- have resistance to the harmful effects of corrosion and aggressive chemical compounds;
- polyethylene pipes are easy to handle during installation (cutting, fitting);
- the inner walls are phenomenal smooth, so their throughput is very high;
- the polymer does not enter into chemical reactions with any substances;
- polyethylene products do not conduct electric current, so they are ideal for underground installation, because stray currents in the ground are not afraid of them;
Important! polyethylene products are much cheaper than steel analogues, which in some cases is a determining factor.
- the weight of polyethylene pipes is 7 times lower than products made of steel, which simplifies their storage, transportation and laying;
- such products have good resistance to temperature extremes;
- the operational life of plastic products is 50 years under normal use.
In which cases the use of polyethylene pipes is not allowed?
However, despite all its advantages, polyethylene products have limitations. Consider cases where the use of polyethylene pipelines for gas transportation is unacceptable:
- polyethylene gas pipelines are not allowed to be used in cases where the conditions of a specific climatic region, the temperature of the wall of the pipeline can drop below -15 ° C. Such indicators can be achieved if the ambient temperature drops below -45 ° C;
- it is strictly forbidden to use polyethylene pipes for transporting liquefied petroleum gas, as this will destroy their walls and lead to an emergency;
- in seismically active areas, if the magnitude of the earthquake exceeds 7 points. However, if it is possible to establish ultrasonic control of welds, the use of polyethylene pipes is allowed at 7 or more points;
- during installation of elevated gas pipelines;
- when laying communications, transporting gas, external and internal appearance;
- when installing pipelines inside tunnels, channels, etc.
- It is also worth noting that the laying of polyethylene pipes is strictly forbidden if the gas pipeline construction passes over roads or railways.
Stages of laying gas communications
Consider the main 3 stages of laying gas pipeline communications:
- Preparatory stage. At this stage, the development of the project. Installation of the gas pipeline should be carried out strictly according to the project, which is prepared in advance by specialists. It should include the necessary equipment that will be used to install the gas line. The project should indicate the gas pipeline path, as well as all possible buildings and other facilities located in the immediate vicinity of the gas pipeline. In addition, the project should include: features of the soil on the site through which the gas pipeline will pass, the location and amount of groundwater, climatic conditions of the area, etc.
- Installation work. At the second stage, all installation work of the gas pipeline communication is carried out. Depending on the specific case, the range of installation work may vary. There are cases (for example, when laying a gas pipe on an overpass) when many construction equipment is used for installation.
Helpful information! Each gas pipeline construction includes a set of welding operations that are aimed at connecting individual steel or polyethylene parts into a single communication. Subsequently, each joint is numbered and marked.
- Stage of control. At the last stage, the installed gas pipeline is checked. As a rule, verification includes two stages:
- test of strength;
- verification of the sealing performance of the structure.
Tests are carried out only after installation of all auxiliary elements: fittings, measuring equipment, etc. The finished gas pipeline structure is subjected to hydraulic tests (pressure check). To do this, use compressed air.
All of the above work should be carried out only by highly qualified specialists in the gas field in accordance with all safety standards and rules.