The connection of individual elements of pipelines is carried out by various methods, however, the most popular of all is welding. This method is used both in everyday life and at various industrial enterprises when connecting pipe parts from different materials (metal, plastic). Pipe welding technology allows joining parts on the pipeline in any position, which is very convenient. In addition, welded joints are characterized by increased strength and tightness, unlike threaded ones.
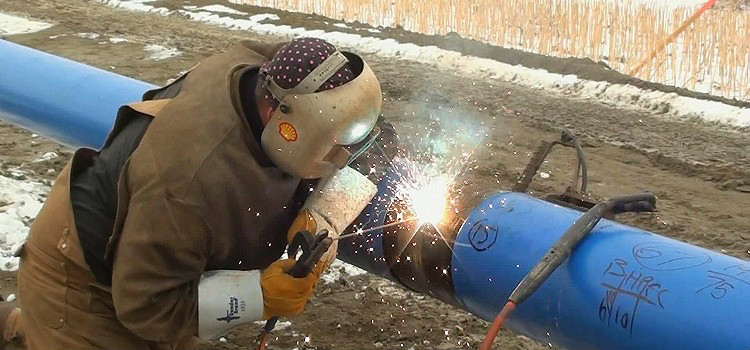
Welding - the most reliable and durable connection used in the installation of pipelines for various purposes
Content
Features of the connection of pipelines by welding
The connection of individual elements of pipelines or household branches is carried out according to uniform standards. The master uses special equipment regulated by GOST, which affects the pipe in one way or another (depending on the specific case).
Helpful information! The whole process consists in connecting individual sections of the pipeline through a seam. After completion of the work, a check of the welded elements (the so-called quality control) is mandatory.
According to the type of applied effort, pipe welding is divided into four types:
- thermal;
- thermomechanical;
- mechanical;
- cold.
With the thermal method, the edges of the pipe are heated. With thermomechanical - the connection of pipes is carried out by heating a special wire. The mechanical method is used, as a rule, for industrial purposes and can be carried out due to the friction force or directed explosion. And there is also cold welding, which is performed using special chemical compounds. The tool is applied to the edges of the pipes intended for welding, and they are pressed, as a result of which after a while a rather strong seam is formed.
Welding pipes of different diameters is performed using special conductors. This can affect the reliability of the connection, however, if all the work is done correctly, then the joint will be strong and tight and will last a long time.
Types of welding and their differences
Welding is a physicochemical method of joining segments of a pipeline that forms a tight connection between two sections of a structure. This occurs either through fusion or through plastic deformation under pressure. The technology for forming a weld may be different depending on the type of welding:
- hot;
- cold.
According to the execution method, this process can be:
- manual;
- automatic.
The manual method implies that all stages of welding work are performed by a person. The automatic method is performed using special machines. In automatic welding, all stages are mechanized and do not require human intervention, however, at the stage of preparation, the wizards make the necessary settings by setting the welding program.The price of such machines is quite high and, therefore, they are used extremely rarely, as a rule, at large enterprises that perform large volumes of work.
Today, there are about 50 types of welding and a huge variety of welding equipment. The most common types today are:
- electric welding;
- cold
- gas;
- diffuse.
Electric welding
Today, the use of electric welding is the most popular method. Although a few years ago, priority was given to gas burners. Such popularity of electric welding is due to the simplicity and low cost of work. Often it is called an arc or contact. According to the type of applied efforts, it is referred to the arc group of thermomechanical works.
To do this, an inverter or transformer is required. This equipment performs the following function - delivers a charge to the electrode. The edges of the element to be welded are treated with an electrode. When materials come into contact, an electric arc of enormous power is formed. This reaction is accompanied by the release of high temperatures, which makes it possible to engage in pipe processing.
The layer of coating (coating) of the electrode allows you to maintain during operation special conditions that prevent the flow of oxygen to the melting point.
Consider what factors the width of the seam depends on:
- from the thickness of the electrode;
- from the material of the welded products;
- welding devices may include different welding modes, which also affects the characteristics of the weld;
- from the speed of the arc and the voltage in the network.
The above parameters determine not only the characteristics of the weld, but also on the amount of slag formed during welding.
Important! It is worth remembering that the formed slag must be removed.
Electric welding of pipes is considered cheaper than gas, however, it takes more time to create a seam in this way. Other advantages of electric welding include:
- functionality;
- universality.
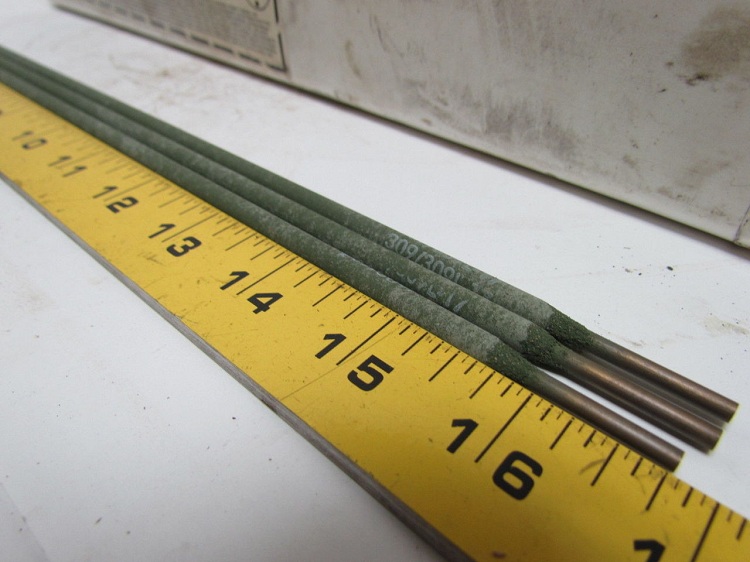
It is impossible to carry out electric welding without electrodes, the size of which is selected depending on the type of pipes processed
Electrode selection
Welds can be different, as a rule, their quality depends on which electrode was used for welding pipes. The choice of electrode depends on several important factors:
- material of which the pipe is made;
- pipe cross section indicator;
- wall thickness.
Helpful information! For thin-walled pipes, electrodes with a thickness of 2-3 mm are used. Welding of thick-walled pipes is carried out by electrodes with a diameter of 4–5 mm.
All electrodes differ depending on the thickness of the coating. The percentage ratio of the mass of the coating to the total mass of the electrode can range from 3 to 20%. A coating layer deposited on the electrode rod creates the necessary environment in which the process takes place without oxygen. There is a certain pattern - the amount of slag that affects the quality of the seam depends on the thickness of the coating layer.
When choosing an electrode, all of the above parameters must be taken into account. To obtain a high-quality weld, attention should be paid to many factors affecting the compatibility of different types of electrodes with pipes.
Cold welding
Cold welding for pipes is regulated by the relevant documentation and is a method of obtaining permanent, tight joints. This method eliminates the heating of the welded parts, and the joining itself is performed due to deformation. Cold welding is carried out due to the pressure exerted on the part. As a result of such welding, the oxide layer is destroyed and the connection is performed at the atomic level (atom diffusion).
Such welding is divided into three types depending on the technology:
- point;
- suture;
- butt.
Cold spot welding is carried out using a punch. The punch is a device that performs the pressing of materials. The second type - seam welding, is performed in two ways: welding along the entire length and performing weld points, which subsequently form a continuous seam. The joint option is performed due to the strong compression fixed in the clamps of the elements.
Consider the main areas of use of the cold method:
- connection of parts made of one metal;
- the production of metal, which has several layers represented by different metals;
- when reinforcing aluminum wires. Reinforcement is made of copper.
The cold welding method is quite popular today. Its popularity is due to the following advantages:
- during cold welding, deformation of metal parts is excluded. This is due to the fact that the workpieces are not heated;
- Using this method allows you to get a very neat seam, characterized by high strength and tightness. In addition, he does not need additional processing;
Note! There are cases when cold welding is the only way out. For example, the combination of aluminum and copper can only be performed by cold welding.
- after performing this process, no waste remains (electrode residues, metal spatter, etc.);
- work is done without the use of electricity;
- this method, among other things, is environmentally friendly, since the work is carried out without the release of toxic substances, as well as without radiation harmful to human eyes.
- the ability to connect large areas when using explosion welding.
Gas welding
The connection of different types of pipes using a gas burner is a very old, but also a reliable way of installing communications. For these purposes, special gas burners are used that are able to heat the pipe to high temperatures.
Due to the heating of the edge with the connecting wire, it quickly reaches the melting point. As a result, the metal floats on top of each other and a durable one-piece connection is obtained, which is resistant to mechanical stress.
Consider the main advantages of using gas welding for the installation of pipelines of different directions:
- high efficiency of the method;
- the use of a gas burner allows you to get a neat, high-quality seam;
- the process is not particularly complex;
The disadvantages of this method include:
- work with a gas burner should be carried out only by a specialist who has certain skills in this area;
- gas welding is a rather expensive method, as it uses expensive resources.
Diffuse welding
All previous methods of welding pipes are used to connect metal pipes, but today such products compete in the construction market with plastic parts. To connect the individual elements of plastic communications, a special method is used, which has gained great popularity - diffuse welding.
The main advantages of such welding include:
- obtaining an aesthetic seam;
- minimum required tools;
- high installation speed;
- attractive price.
To obtain a permanent connection of two plastic pipes, special devices are used that heat the plastic. Such devices are equipped with various nozzles. All nozzles have their own diameter, suitable for the size of the cross section of a particular pipe.
Consider the main stages of connecting two plastic pipes using such an apparatus:
- Focusing on the diameter of the connected pipes, the desired nozzle is selected.
- Pipes are laid inside the device.
- The material of the pipes is heated and their ends are squeezed inside the apparatus.
- After the connecting seam is formed, the device turns off.
After a few hours, the resulting compound can already be operated. This method is quite simple and fast, and the pipe welding line is durable and accurate.
Types of welded joints
For different types of pipes (in terms of material and purpose), the application of various welding methods is the norm. However, in almost all cases, electrical alternating current is required. This is due to financial benefits, since the use of other options for electric energy entails more costs. Welded joints are two or more parts that are joined together by means of welds.
Consider the main types of welded joints:
- butt;
- angular;
- overlapping.
Important! When welding pipes with a wall thickness of more than 3 mm, cutting their edges is necessary. The joint opening angle should be no more than 60–70 °. When cutting pipes for welding, it is necessary to remove the chamfers from the ends. This can be done mechanically or in any other suitable way.
Butt. This type of welded joint is very common due to the fact that practically no deformation occurs during the cooking process. In addition, such joints have the lowest internal stresses. They also differ in increased strength characteristics under both static and dynamic loads. Seams during such welding can be:
- single (for pipes with cross-sectional indicators up to 500 mm);
- double (for pipes with a cross section above 600 mm).
Corner Corner joints are a subspecies of butt welding and, as a rule, are used for joining pipes with any additional parts at an angle. Pipe welding at an angle is performed in two ways:
- with bevelled edges;
- without bevel.
The strength characteristics of the corner joints are not as good as those of the butt joints, however, they are still quite good.
Overlap. Such a connection is not used for welding metal pipes. As a rule, they are joined by individual parts or plastic pipes. This is due to the fact that such a connection is the most unreliable.
Technology for welding thick-walled pipes
Welding of thick-walled pipes is carried out if the wall thickness of the pipe exceeds 20 mm. Such welding is carried out in layers of increased thickness. This allows you to increase the strength of the connection by 10-15%. This type of work is usually done by two welders at the same time. The first welder applies a regular seam, and the second a thick layer.
How to weld pipes with thick walls:
- Welding begins in the ceiling position with a gradual increase in weld thickness (the line for welding thick-walled pipes should be as even as possible).
- Next, you need to go into a semi-vertical position.
- Using the electrode, a horizontal platform is carried out.
- Then welding is performed in the lower position. This allows the use of electrodes with a thickness of up to 5 mm.
Clearance pipe welding
Many people wonder: how to weld pipes under clearance? And even some experts do not fully understand how to cook pipes using this method. This is especially true for young people who have just graduated from technical schools and vocational schools.
First of all, when welding pipes under clearance, it is necessary to grab the pipes. This eliminates the possibility of deformation of the root. How many sticking points must be performed - determined based on the size of the pipes. Parts are caught so that the gap at the junction does not converge.
After performing a junction of the joint, it must be cleaned. In addition, it is very important to remember that if you found defects at the root (for example, cracks) during welding under the lumen, you need to remove them. After the surface is cleaned, the seam is filled. As a rule, filling a seam is considered the easiest step, however, in some cases, it takes up to 30% of the root to fill it.
It is recommended to leave a small recess when filling the seam. A depth of 1.5 mm will be sufficient. This is necessary to perform the cladding. If you do this, the facing material will lie very neatly in this small furrow and you will get an aesthetic seam. It is very important to remember two rules: when filling the seam, it is necessary to maintain the working angle, and also cook on a short arc.