How to connect plastic pipes depends on the material and the specific operating conditions of the water supply. Distinguish between detachable and one-piece connections. The latter are divided into welded butt and socket. The detachable connections of the plastic pipes make it possible to disassemble the pipeline. Flange docking is the most time consuming.
Content
The main types of polymer pipes
Currently, the most common are pipes made of such materials:
- polyethylene;
- polypropylene;
- polyvinyl chloride (PVC);
- crosslinked polyethylene.
There are also metal-plastic pipes having a structural internal aluminum component.
Polymer pipes have a smooth inner surface, which prevents the accumulation of sediment, reduces noise during fluid movement and is resistant to rust. Such products should be protected from mechanical damage - shock or sharp compression.
Note! During transportation of water with high temperature, the pipe can expand, which reduces the risk of breakthrough.
In the case of significant heating, it can lengthen, and this leads to loosening of threaded joints. For polypropylene, the critical temperature is 140 ° C. From the choice of how to connect plastic pipes, the durability of the operation of the water supply depends.
Methods for joining plastic products
Plastic pipe joint can be carried out in many ways. The main ones are:
- into the bell;
- using adhesive;
- threaded connection;
- diffuse welding;
- flange connections;
- docking with collets;
- welding with electrofusion.
Do-it-yourself pipe connection of pipes with do-it-yourself is more often used in systems with gravity media, for example, sewer. It can also be used for a non-pressurized water supply. For joints of plastic pipes, standard adhesive or cold welding is applicable, which involves dissolving the top of the polymer under the action of a specific component of the adhesive and bonding the two parts at the molecular level. So the pipes of sewer, water supply systems and networks transporting gas are connected.
Plastic pipes are connected to metal products by both threaded and flanged methods. Diffuse (high-temperature) welding is characterized by preliminary heating of parts in a special apparatus, and then their joining. When the pipes are flanged with their own hands, metal patch flanges or welded bushings under them are used.
The connection for plastic pipes using collets is characterized by the installation of crimp fittings. In this case, the teeth of a metal pipe, crashing into the product, form a joint. For welding with an electric coupling, parts are cleaned and degreased. After connecting the current, the pipes are heated and the connection is formed.
PVC pipe joint
There are such ways of connecting PVC pipes with your own hands:
- bell-shaped;
- using adhesive.
PVC pipes have a bell at one end in which a rubber seal is installed. At the initial stage of the connection, the pipe is cut with a pipe cutter or a hacksaw for metal into the necessary segments. Further, there is a cleaning of the connected end and the inner surface of the socket. The smooth end of the plastic pipe is inserted all the way into it, which is lubricated with a silicone compound. The pipe must be removed by 7-10 mm by pulling on it. It is better to pre-label to control the degree of extraction.
To connect PVC pipes using an adhesive, you must:
- sandpaper the outer surface of the plastic pipe and the inside of the bell;
- degrease glued surfaces;
- apply glue to the entire part of the pipe that will be inserted into the socket;
- insert the prepared pipe all the way into the socket and turn it 90 degrees;
- press the parts to be glued and hold for about a minute.
Degreasing, applying glue, joining parts should take less than three minutes, which will ensure high-quality adhesion.
Helpful advice! For degreasing, it is better to use methylene chloride.
Full glue hardening occurs within a few hours.
Cross-linked polyethylene pipe joining methods
How do-it-yourself pipes made of cross-linked polyethylene are:
- compression fittings;
- press fittings;
- electric welded fittings.
The latter method is rarely used because it requires special equipment. In the case of a pressing fitting, an important role is played by the property of cross-linked polyethylene to restore shape after some deformation, in which the polymer molecules on the fitting completely fill the gaps and recesses.
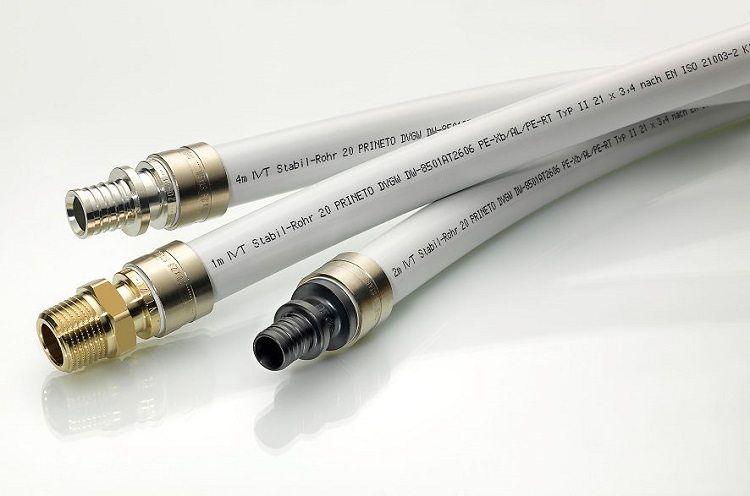
For the installation of pipes made of cross-linked polyethylene, compression and press fittings can be used
In order to properly carry out work on the coupling connection with your own hands, you will need two mounting sleeves, an equal bore coupling, a tool for expanding plastic pipes.
Using a pipe cutter, 5 cm of its length is cut from the end of the pipe, the chamfer is removed at the end. A sleeve is put on the prepared part of the pipe. In it, the end of the pipe is flared using a hydraulic or hand tool. Next, a sleeve is inserted on which the sleeve is slid. Similar actions are carried out for the other end of the pipe made of cross-linked polyethylene.
The coupling method for connecting plastic pipes is leakproof and reliable.
Features of the connection of polypropylene pipes
With their own hands, pipes with a diameter of up to 6.3 cm are mainly connected by a bell-shaped method or by socket welding. For large pipe diameters, butt welding is recommended. Polypropylene pipes with a diameter of up to 4 cm can be welded with a manual welding machine, more than 4 cm with a centering device. The heating element (nozzle) is a sleeve and mandrel, which melt the outer surface of the pipe and the inner part of the socket.
Standard Teflon nozzles have a diameter of 16-40 mm and are cleaned after each welding case.
Important! The cold nozzle must not be cleaned from the plastic layer.
The welding machine with the necessary nozzles is installed on a flat surface and fixed. The welding temperature of polypropylene pipes is about 260 degrees. Socket welding is performed in the following sequence:
- a pipe is cut at a right angle;
- the socket of the fitting and the end of the pipe are cleaned of dust and dirt;
- a mark is applied to the pipe at a distance of 2 mm more than the depth of the socket;
- a pipe is inserted into the sleeve, and a bell is put on the mandrel;
- withstand the necessary heating time, remove the parts and dock them.
Polypropylene pipes can be joined by compression fittings. No special equipment is required for installation.
Polyethylene pipe joint
The most reliable ways to connect polyethylene pipes with your own hands are butt and thermistor welding. Non-pressure structures can be glued. For butt welding, the ends of the pipes to be connected are installed in the machine centralizer. The ends are fixed, leveled, cleaned and mechanically processed with a crosscutter.
Further, the surfaces to be joined are heated with a special tool, which is removed after fusion of the surfaces to be welded. The connection is formed by closing the ends of the plastic pipes with the necessary force. The pressure of the clamp gradually increases to the desired value. For some time, the joint is cooled and the connection is ready for operation.
Butt welding is applicable for pipes with a diameter of more than 63 mm. Polyethylene pipes can be connected using couplings with embedded electrical heating elements. Such a joint is designed for a pressure of 16 atm.
Plug-in connections of polyethylene pipes of small diameter (up to 50 mm) can be obtained using fittings. The collet crimp connection is designed for a pressure of 25 atm. Thanks to the rubber o-ring, the joint is sealed, and by cutting the teeth of the plastic sleeve into the pipe, it is resistant to mechanical stress.
Joining of metal-plastic pipes
Welding is not applicable to metal-plastic pipes, since the temperature used is not enough for the melting of aluminum. A pipeline of similar materials is going to fittings. Do-it-yourself connection of plastic pipes with a metal layer produced using:
- press fittings;
- crimp fittings;
- push fittings.
The latter method provides simple and quick installation, a high degree of reliability, the ability to disassemble the joint if necessary. In addition, a minimum number of tools — a calibrator and a cutter — are required to complete the connection.
Installation of press fittings provides an integral connection. The crimp assembly is formed by a special device. The pipe is first cut off and the end processed by the calibrator. A crimp sleeve is put on the pipe. After inserting the fitting, it is crimped with electric or manual press pliers.
Important! Repeated crimping of the coupling by press pliers is prohibited.
The permissible maximum pressure at the connection is 10 bar.
The choice of elements and methods for docking is wide enough. This allows you to find the most suitable solutions when installing the pipeline, how to properly connect plastic pipes.