From products from other materials plastic pipes differ in relatively low cost, as well as ease of assembly. They are widely used for pipelines of hot and cold water supply, sewerage, heating systems, ventilation. The most common are products made of polypropylene and polyvinyl chloride. A pipeline of plastic elements is assembled by soldering. You can mount the system yourself if you follow the necessary recommendations.
Content
Characteristics of plastic pipes
Plastic pipes differ in the type of polymer from which they are made: polyethylene, polypropylene, polyvinyl chloride. They can be used for cold water (with a pressure of 10 atm. And a working temperature of 20 ° C) or hot (with a pressure of 10 atm. And a temperature of 60 ° C) of water supply.
Also, some types of plastic pipes are applicable in heating systems at a pressure of 6 atmospheres and an operating temperature of 80 ° C with its maximum value of 90 ° C.
Polymer pipes have a long service life, no deposits or condensation, low noise, low weight, corrosion resistance, ease of installation, strength, resistance to aggressive environments and water hammer. In addition, they do not need painting and thermal insulation. The service life of such pipes is 50 years.
Note! Plastic pipes can be reinforced with fiberglass or perforated aluminum to increase strength, reduce thermal and thermal expansion.
For heating, polypropylene pipes are used, characterized by flexibility and resistance to pressure and temperature drops.
Elements required for installation work
Do-it-yourself installation of plastic pipes may require the use of components:
- adapter;
- coupler;
- couplings with internal or external thread;
- branches 90 and 45 °;
- tee;
- crosses;
- plug connector;
- bushings and plugs;
- clamps.
The adapter is used to make the transition between pipes of different diameters. When soldering pipe segments of the same diameter, a connection sleeve is necessary, which, in the case of a threaded connection, is equipped with an internal or external thread. The turns of the pipeline are carried out by bends. For soldering into a knot of three pipes, tees are used, four - crosses. The tee is also equipped with thread.
If necessary, a detachable connection can be created. Pipelines are usually closed by plugs or plugs. Pipes are attached to walls or structures with clamps. They are plastic and metal.
Based on materials used in production fittingsdistinguish between combined and monolithic samples. In combined fittings, part of the structure is made of polymer, and the other part is made of metal. They come with a fixed and movable threaded connection. Monolithic fittings are made entirely of polymer.
Accounting for thermal expansion of pipes
Installation of plastic pipes both for cold water supply and for the sewer system begins with the design and calculation of the required number of components. For a hot water supply, account must be taken of the thermal expansion of the products.
Important! If the maximum possible temperature difference is 80 ° C, then the elongation of each meter of a plastic homogeneous pipe is 1.2 cm, of the combined one - 0.2 cm.
In pipelines with a length of more than 2-3 m, elongation at the joints may occur when elongating with increasing temperature or compression when cooling the pipes. This situation is especially dangerous when using homogeneous pipes made of polypropylene. To combat thermal elongation in hot water systems, flexible compensation loops or temperature compensators are installed. They are P and Z-shaped bends.
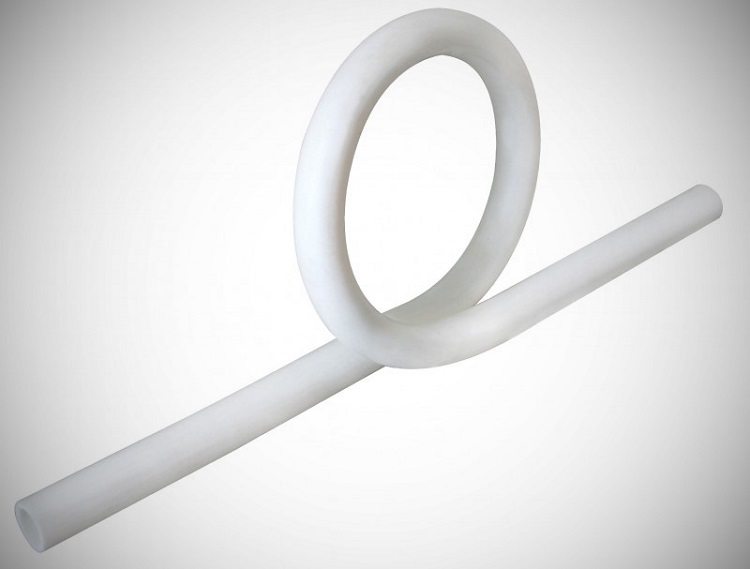
The easiest option for the temperature compensator is a flexible loop from a regular polypropylene pipe
When installing plastic pipes should provide for the possibility of unhindered temperature movement of products. To do this, at bends near welded pipe joints, cavities are left that are filled with soft material, or air pockets to compensate for thermal expansion.
Soldering a plastic pipe
For pipe soldering you need a machine for manual welding with a set of nozzles, a roller pipe cutter or scissors, a tool for cleaning the ends of products. For pipe connections with a diameter of 16-50 mm, a device with a power of 650 W is used, 63-110 mm - 1600 W.
First, pipe sections of the required length are cut. For this, sharp scissorsthat do not deform a thin-walled product. Before soldering the combined pipes, a stripping is performed, in which the upper plastic layer and the middle aluminum are removed.
Depth welding indicated in accordance with the table.
Table 1
Pipe diameter mm | Welding depth mm |
16-25 | 13-15 |
32-50 | 16-20 |
63-110 | 24-32 |
Welding should be done with gloves to protect against burns. The temperature of the soldering iron is about 250 ° C. The heating time is also determined by the table.
table 2
Pipe diameter mm | Heating time, s |
16-25 | 5-7 |
32 | 8 |
40 | 12 |
50 | 18 |
63 | 24 |
75 | 30 |
90 | 40 |
110 | 50 |
Welding must be done at a fast pace, because if the surface of the melt cools, the connection will not be strong enough. It is necessary to monitor the alignment of the elements. At the final stage, the connection is fixed and a certain period is maintained (connection up to 10 s, cooling - up to 8 minutes).
Features of the wiring of the plastic line
The wiring is collector, serial, with bushing outlets. The latter option is extremely rare.
Do-it-yourself installation of plastic pipes should begin with a detailed scheme of the future pipeline, trying to minimize the number of bends and parts. The layout of the open type trunk involves vertically installing pipes in the corners, and horizontally - just above the floor. This placement makes the water supply network less visible.
Covert cabling is difficult to install and requires accurate calculation. Only a solid pipe can be walled into the wall, and the joints should have free access.
Fittings are used to connect plastic products. They are detachable and one-piece, threaded and without thread. One-piece connection connects flexible hoses.
Important! It is not recommended to bend plastic pipes.
Couplings are used to transfer the trunk to a different diameter or to merge straight sections. To create branches, tees are used. If the highway has turns, then they are carried out by angles.
Pipeline Installation Steps
The installation of plastic pipes involves the following steps:
- Pipes are cut into pieces of the required length.
- The ends of the products are cleared of burrs and crumbs.
- The marker indicates the depth of the pipe entry into the fitting and the place of their connection.
- Heated nozzle soldering iron, the fitting and pipe are put on it.
- After heating, the elements are interconnected.
Work should begin from the most remote place from entering the apartment. When cutting fragments, it must be remembered that the use of fittings will lengthen the areas by 3-5 cm. The pipe inlet depth depends on the dimensions of the fitting. He should not push forward all the way. Otherwise, the pipe will narrow at the junction. It is also required to provide simultaneous heating of the elements. They should be mounted without turning in the centerline and with some effort.
If the diameter of the product is more than 50 mm, it is recommended to chamfer before welding at an angle of 45 °. For hot water, plastic pipes are fastened more often than for cold water. The pipes are fixed to the wall using clips that are installed at a distance of less than 1 m along the entire length of the pipeline.
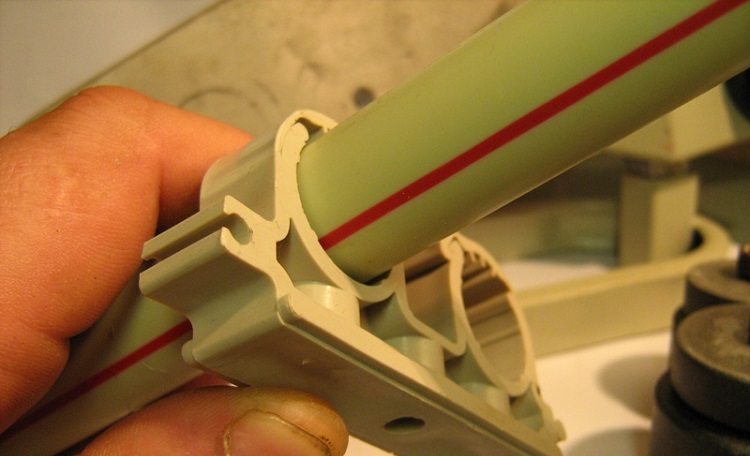
Pipes are fixed to the walls with clips, which make it possible to quickly dismantle the pipe if necessary
Features of installing PVC pipes
Docking using a sleeve assumes the presence of PVC pipes and fittings for them. The easiest way is to connect to the bell. Each pipe at the end is equipped with a bell and rubber ring, into which it is necessary to insert the smooth end of the next pipe to a special convex strip. When using cold welding to connect PVC pipes, products are treated with a chemical composition.
Installation of PVC pipes includes the preparation of the ends of the connected products and the gluing procedure itself. First, a check is made to see how the elements fit together.
Note! PVC pipe should freely enter the socket for 2/3 of the seat.
The surfaces to be glued must be roughened. To do this, the inner part of the socket and the end of the pipe are treated with sandpaper. It is recommended that you use the adhesive designated by the pipe manufacturer.
Bonding is carried out in the following order:
- The cloth is moistened with a cleaner (usually methylene chloride), which is sold with glue, and the surfaces are rubbed with it (during processing, they are degreased and softened).
- Using a swab or brush, glue is applied.
- The pipe is covered with a thick layer of glue, the inner surface of the socket is thin.
- The fitting is put on a PVC pipe so that between the marks on the products there is a distance of 2-3 cm.
- Parts rotate and hold motionless for about 30 seconds.
If glue is correctly applied, then an even roller is formed around the pipe near its entrance to the socket.
Plastic pipes are used for installation of almost all types of engineering networks. The simplicity of assembly and installation allows you to do the installation work yourself.