Deposits form on the walls of process pipelines over time. This process does not depend on the method of operation of the system and leads to a decrease in its throughput. And for this reason, emergency situations arise. To minimize the risk of equipment damage and localization of problem areas, pipelines are diagnosed. Today, methods have been developed to carry out this procedure without dismantling and opening equipment.
Content
The reasons for the need to assess the condition of pipes and diagnostic methods
In general, pipeline diagnostics are performed in the following cases:
- when planning repair work with their subsequent implementation;
- as a prevention of possible malfunctions;
- to assess the condition of the pipes after the repair.
It follows from this that when servicing technological engineering communications, this procedure is mandatory.
It is also necessary to verify the condition of pipelines of this type when they are already in use, and not just before commissioning. Before starting them, experts check the degree of conformity of the welds to the requirements of GOST and SNiP, examine the quality of the joints and find out whether the internal integrity of the pipes is preserved.
There are currently four diagnostic methods.
1. Magnetooptical flaw detection. Allows you to see using magnetic flux defects present in the ferrimagnetic material. It is impossible to determine their depth with sufficient accuracy in this way.
2. Ultrasound diagnostics. This method checks the quality of the connection of components of pipelines operating under high pressure and at nuclear power plants. This is due to the absolute safety of ultrasound tube products. The principle of detection of defects implies the ability of the waves of the ultrasonic range to easily penetrate homogeneous material. If there are obstacles, the waves are reflected.
3. Pressure testing with high pressure. Such pipe inspection has been used for quite some time. The low cost of work is one of the undoubted advantages of this method. Inert gases, gas mixture or water vapor are pumped into the pipeline so as to create a pressure inside it, 5 times the working pressure. Then, the joints, seams and joints of the boiler equipment and pipes are inspected. The determination of the areas in which steam leaks occurs by the presence of condensate on them.
Note! This is how diagnostics are carried out in apartment buildings of domestic heating and water supply systems during the scheduled repair and maintenance work during the summer season.
4. Video diagnostics. Its other name is telediagnostics. This method allows you to visually assess the condition of the pipeline. For analysis, information recorded by special cameras mounted on a pushed fiberglass rod or on robots is used.Robots, moving inside the highway, remove everything that they meet on their way. Then the image is analyzed. This technique is able to detect gross violations of the integrity of pipes, leaks on segments in soils or closed tunnels, and places where large blockages and mud deposits have formed. Many specialized construction companies have adopted this technique, and therefore this diagnostic method deserves a separate discussion.
When do you need video diagnostics
Inspection of pipelines by this method is relevant in the following cases:
- when commissioning new systems, including sewage. Then, for all parameters of sewage disposal systems, a video document is attached confirming the compliance of pipelines with SNiPs operating in the territory of our country .;
- damage has occurred in the system or a blockage has formed (to solve the problem, you must find the source);
- a piping check is required. The need for such work arises when the circuit is lost.
In-line diagnostics are performed using special equipment. It includes:
- camcorder head with sapphire lens. All this element is placed in a stainless steel case;
- push cable. He wraps himself on a drum;
- camcorder control unit.
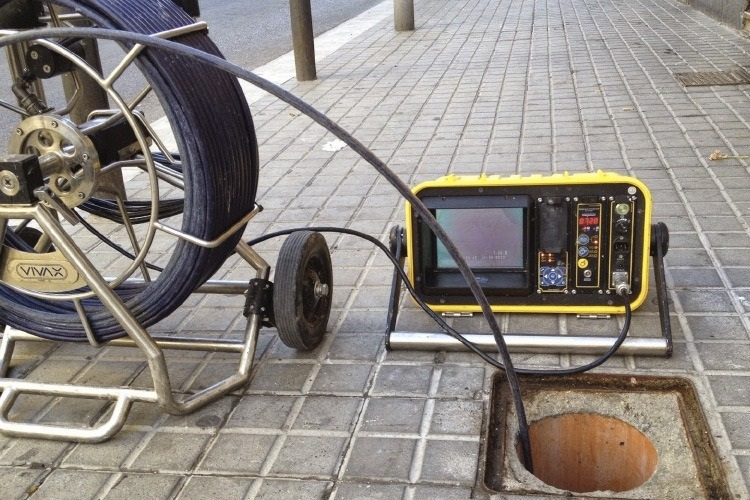
Pipeline inspection is carried out using a camera on a long cable that transmits the image to the monitor
The camcorder moves along the length of the collector under the influence of force from the push cable. The image formed by it is transmitted to the control panel display. To ensure proper functioning of all elements of the system, a powerful (usually LED) light source is moved with the camera. It is installed on a special movable module.
You can detect the following problems:
- defects in the decoupling of the system;
- leakage and leakage of joints;
- foreign objects stuck inside and clogging;
- the presence of defects in the pipe material.
Pipeline inspection can be carried out in pipes of different diameters and configurations, only equipment is changed - it can be floating or portable. The latter applies when pipelines are not yet connected to the water supply system. Floating equipment is used when there is possible water in the network. Most of these systems are equipped with a winch with an electric meter. These devices allow you to determine the depth of immersion and the location of the camera.
Today, there are four types of systems used to diagnose pipelines:
- Portable push system. It has a rigid cable with which the operator pushes the video camera through the element of engineering communication.
Good to know! This cable is also a means of supplying power to the camcorder, and information is transmitted to the operator’s display through it.
- Remote control camcorder. Such a device has a large viewing angle, powerful backlight and high resolution, allowing you to get a high quality image. After all, only then will it be possible to verify the fact of compliance of the state of the studied design with the requirements of SNiP. The movement takes place through an operator-controlled self-propelled conveyor.
- Satellite cameras. These are auxiliary cameras present in the device along with the main one. With their help, a tele-inspection of the branches in the pipes is performed.
- Special equipment. These include devices that allow you to inspect deep wells, as well as wireless equipment.
Features of video diagnostics and its results
The diameter of the pipes in which it is allowed to carry out this procedure varies in the range of millimeters. The camera can be mounted on a cable with a length of about 250 meters, which allows you to explore fairly long sections of pipes and objects at a depth. However, the latest technological developments are aimed at providing video diagnostics at a distance exceeding 500 meters!
The designers foresaw the need to change the viewing angle of the camera and the configuration of the equipment used in pushing wheeled systems. This is realized by the possibility of using wheels with different diameters. Recommended power used for lighting LEDs - from 500 lumens.
At the end of the video diagnosis, you can get results that allow you to:
- with a high degree of accuracy to localize sections of engineering communications susceptible to corrosion;
- pinpoint the causes of blockages and take the necessary preventive measures to prevent them from occurring;
- timely detect leaking points of the trunk branch.
- the ability to choose an effective method of cleaning pipelines from blockages that meets the requirements of SNiP for non-violation of the integrity of the system design.
Pipeline Industrial Safety Expertise
In addition to the main pipelines, today there are several types of pipeline transport. These include technological pipelines located on the territory of enterprises and ensuring the carrying out of the technological process, as well as the operation of equipment. In addition, these include field pipelines through which gas and oil are transported, etc.
An industrial safety review (EPB) is necessary for those that fall under the scope of the Federal Law No. 116-FZ.
Important! Organizations that have the appropriate license have the right to perform this procedure.
EPB begins with a careful study of engineering communications documentation. Having determined the “most dangerous sections” by “papers”, comparing the design and actual location of the pipeline, and finding out whether the operating conditions met the requirements of SNiP, the specialists proceed to the technical diagnosis of the investigated object.
First, an external and (if possible) internal inspection is carried out. At this stage, pipe sections with an irregular shape, metal and insulation defects are identified, the condition of the welds is determined. According to statistics, most cases of failure of process pipelines are due to corrosion processes. All of the above methods can be used to identify internal defects.
Upon completion of the diagnostics by means of non-destructive testing, it is possible to carry out pneumatic and hydraulic tests (by air under pressure or water). However, their feasibility is the subject of controversy among experts in the industry. Some say that hydrotesting worsens the fracture toughness and ductility of a metal. Others argue that without conducting functional tests and without comprehensive monitoring, it is impossible to obtain reliable information about the design's compliance with SNiP requirements. After all, the equipment can fail, for example, if the flaw detector is incorrectly set up or because of the incorrect selection of the piezoelectric transducer. Therefore, there is a danger that after starting the pipeline will again leak.
It must be understood that the testing is associated for pipeline owners with technical problems associated with stopping the production cycle. For this reason, controversial issues may arise between the customer and the implementing organization during the electronic safety procedure.Therefore, one of the priority areas for the development of industrial safety expertise technologies is the adaptation of non-destructive testing methods to the conditions of the diagnostic process without the need to decommission the pipeline.