The electromagnetic solenoid valve for gas is an economical electromechanical device used to regulate the flow of gas supplied through the gas pipeline. At the time of supply or shutdown of power by the device, the valve opens or closes the passage section. Depending on the operating characteristics of a particular section of the gas pipeline system, a certain type of valve is selected.
Content
Purpose, principle of operation and valve design
Electromagnetic devices are used to quickly remotely control the gas pipeline system as control and shutoff valves. They provide security that is recognized to be quite adequate for the transportation and use of natural gas. The ubiquity of electromagnetic automatic solenoid devices as shutoff and control valves affected not only industrial facilities and gas pipelines, but also the domestic sphere. They are installed on household appliances such as gas water heaters and boilers, as well as on gas cylinders and when installed on a HBO car.
It is possible to install filters inside the solenoid devices, which allow additional purification of natural gas from impurities contained in it. If a natural gas leak occurs, when the pressure in the system changes instantly, the automation will instantly shut off the flow of the working medium, eliminating the spread of toxic substances that pose a huge threat to health.
Note! You can also use the solenoid device as a cutoff device: having placed it at the place of the gas pipeline inlet, they seek to stop the supply of natural gas, if necessary.
They work this way. Until electrical voltage is applied, the device remains static, the coil is de-energized, and the membrane or piston of the valve and the valve seat are tightly sealed by mechanical action of the spring. By applying electric voltage to the coil, we achieve the opening of the valve, which occurs under the influence generated by the magnetic field arising in the coil, on the plunger that is drawn into it.
Electromagnetic devices for adjusting the gas supply are composed of such elements:
- body;
- a lid;
- membrane (piston);
- plunger;
- stock;
- spring;
- electric coil (solenoid).
For the manufacture of cases and covers can be used in various materials:
- metals and alloys (accepted use of cast iron, stainless steel, brass);
- polymers (resort to the use of nylon, polypropylene, ecolone, etc.)
The manufacture of plungers and rods requires special magnetic materials. For coils, a housing is provided that is protected against dust or completely tight.To wrap the solenoids, use a high-quality enameled wire, which is electrotechnical copper.
Electromagnetic devices are connected to the gas pipeline by a threaded or flange connection. Connection to the mains is via a plug.
Classification of solenoid valves according to device features
Solenoid valves are characterized by a significant variety of design features, and therefore there is an extensive field for classification.
They differ in the working environment used in systems where the devices are installed:
- water
- air;
- gas;
- a couple;
- fuel, for example, gasoline.
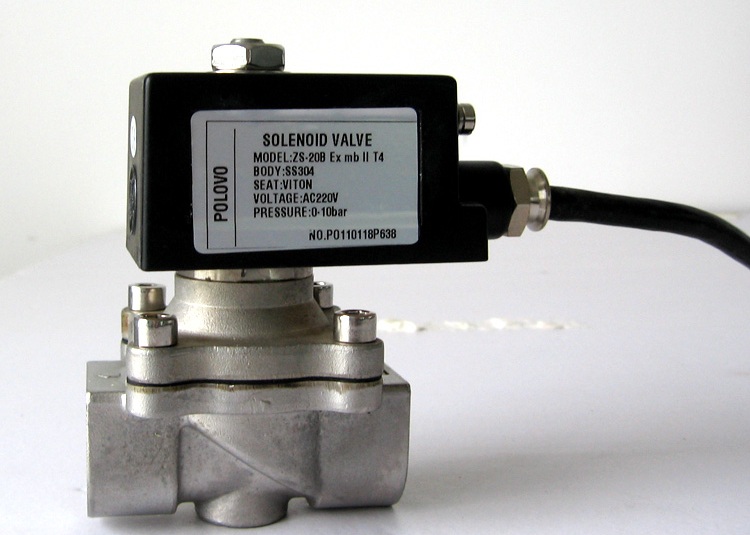
In difficult conditions, where there is a probability of emergencies, explosion-proof valve models are used
The composition of the working environment and the features of the room determine the performance features:
- ordinary;
- explosion proof. Adaptations of this kind are usually installed at facilities that are explosive and fire hazardous.
According to the control features, there is a separation of electromagnetic valves into devices:
- direct action. This is the simplest design, which is characterized by reliability and speed. There is no pilot channel. When the membrane rises instantly, the device opens. In the absence of the action of a magnetic field, the spring-loaded plunger lowering presses the membrane. The direct-acting valve does not require a minimum pressure drop, it creates the necessary effect on the spool rod due to the traction force of the coil located at the top of the device;
- having membrane (piston) reinforcement. In contrast to direct-acting devices, they use the transported medium itself to function as an additional energy supplier. These valves have two spools. The purpose of the main spool is to directly cover the hole, for accommodating which the body seat is reserved. The control spool closes the discharge opening (s) through which pressure is released from the cavity above the membrane (piston). This leads to the rise of the main spool and the opening of the main passage.
According to the location of the locking mechanism at the moment when the coil is in a de-energized state, it is customary to separate the so-called pilot devices as belonging to a certain type:
- normally closed (NC). In the case of NC valves, when the solenoid is de-energized, the passage for the working medium is closed. That is, a static position implies the absence of voltage on the solenoid, the closed state of the device. Due to the difference in diameter between the pilot and bypass channels in favor of the first, a decrease in pressure over the membrane occurs. The pressure difference ensures the lifting of the membrane (piston) and the opening of the valve, which remains in this position while voltage is applied to the coil;
- normally open (BUT). On the contrary, in valves belonging to the normally open type, when the coil is in a de-energized state, the working medium can move along the passage in a given direction. Keeping the HO valve closed, ensure that the coil is continuously energized.
Note! A number of modern modified models provide that the device, if necessary, can be reconfigured, turning it, if necessary, into either an open type valve or a closed type.
There are also models of the device in which, when a control pulse is applied to the coil, switching from open to closed and in the opposite direction is provided. Such an electrovalve was called bistable.To ensure functioning, such a solenoid device needs a differential pressure and a constant current source. Depending on the number of pipe connections, it is customary to call solenoid valves:
- two-way. Such devices have one inlet and outlet pipe connection. Two-way devices are both NC and NO;
- three-way. Equipped with three joints and two passage sections. They can be produced as NC, BUT or universal. Three-way valves are used for alternating pressure / vacuum supply to distribution valves, single-acting cylinders, automatic actuators;
- four-way. Four to five pipe connections (one for pressure, one or two for rarefaction, two for a cylinder) ensure the operation of double-acting cylinders, automatic drives.
What you should carefully look at when choosing a solenoid valve
When choosing a solenoidal device for controlling gas flow, it is recommended to take into account a number of characteristics and requirements, neglect of which can result in operational problems:
- The rated operating pressure must be suitable for the application. The cost of acquiring a device with a higher nominal pressure may be unnecessary or even harmful (if the pressure drop is insufficient);
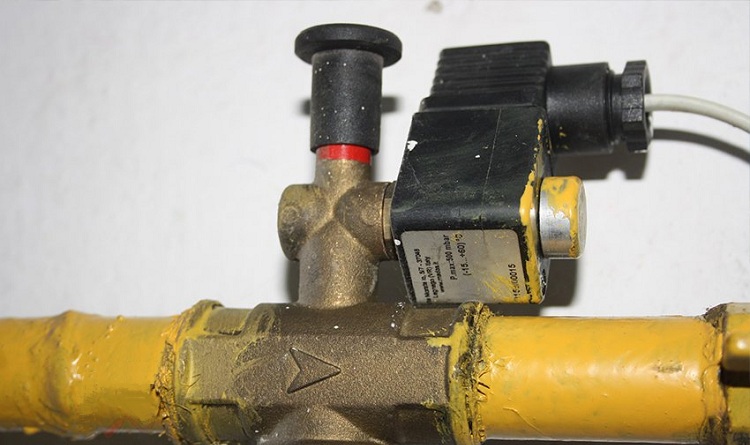
Depending on the valve model, the rule of its installation is observed - in the direction of the medium or against
- installation of a two-way valve is carried out exclusively in the direction specified by the manufacturer of the device. And the two-way solenoid valve works with the flow of the working medium moving in one direction. An attempt to operate in a direction that does not coincide with the one indicated by the manufacturer will either lead to unstable operation of the device or make operation impossible;
- Most device models are available for use in a clean working environment. Manufacturers indicate exceptions that should be given the closest attention. The installation, in which the electromagnets are vertically located, will help prevent the ingress of impurities into the core tube;
- most models are operated at rated voltage with deviations not exceeding 10%.
Good to know! Under reduced voltage, opening / closing will be incomplete, vibrations and excessive noise will occur. With increased voltage, overheating is possible. In both cases, the device will fail prematurely.
- the size must be appropriate so that performance does not suffer;
- the device must be adapted to function with minimum / maximum pressure drops at the place of intended installation;
- electrical parameters must be considered. Most models allow simple electrical control. In some models, the use of manual on / off mode in an emergency is provided. Intrinsically safe devices use ultra-low power, eliminating the appearance of sparks in explosive and fire hazardous environments;
- the materials of which the structure is composed must withstand the operating conditions at the place of the proposed installation;
- The selected device should be suitable for the available power source. Replacing the coil does not allow you to redo the valve, designed for a different type of current.
The spread of electromagnetic solenoid valves for gas was facilitated by the introduction of a number of technological innovations, as a result of which the productivity of the devices increased and the cost decreased. The installation of devices is not associated with the need to purchase additional components, as is the case with ball valves, and requires minimal time, money and effort.The electromagnetic solenoid device is designed for long-term operation, withstanding about a million inclusions.