Pipe connection is an integral part of the design and installation of pipelines for various functional purposes. For this purpose, a variety of fittings are used, including couplings. In the operation of networks he assigned one of the main roles. Indeed, in any highway there are bends, and therefore engineering communications without couplings will not function effectively. And it doesn’t matter what type of pipeline - metal or polymer.
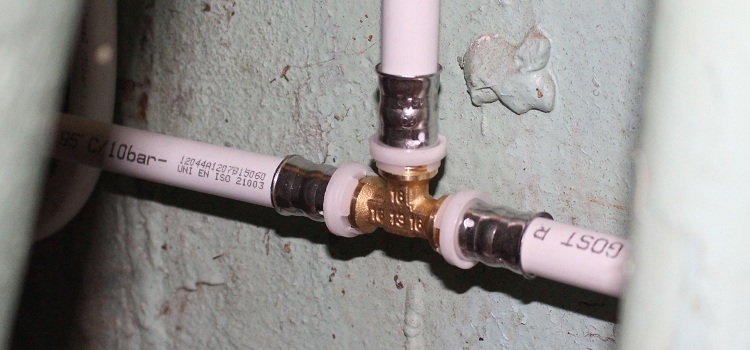
The connection of metal-plastic pipes is carried out by different types of fittings, the installation of which has its own characteristics
Content
Types of connections
In general, connectors are classified according to a number of key characteristics. Depending on the function performed, fittings are:
- cross-shaped - are used to organize the removal of two branches from the main highway of the system;
- nipple - provide the ability to connect metal-plastic products with flexible hoses;
- angular - change the direction of the pipeline by a certain angle - 90, 45 or 120 degrees;
- tee - are used to organize one branch from the main pipe of the mounted engineering communications;
- coupling - with their help, a standard connection of tubular products located on the same line is performed.
In addition, fittings are usually divided into direct and transitional. The former are used to connect pipes with identical diameters. The second ones are used when you need to change the cross section of the trunk. However, there is a main criterion according to which fittings for the installation of metal-plastic products are divided into three types - threaded, compression and press fittings.
What tool is needed for working with plastic pipes. Types of couplings and their installation
It should be noted right away that the use of such a fitting as a coupling in metal-plastic pipelines is not widespread. The reason for this phenomenon lies in the fact that pipes made of metal-plastic arrive at the end user with bays of tens of meters in length. Therefore, the docking of two elements made of this material is irrelevant. After all, the contractor can rewind a measuring segment of any necessary length from the bay.
And yet, sometimes it is necessary to solve the problem of connecting two metal-plastic pipes. Working with such products does not require welding or soldering, it is enough to have the following tool at your disposal:
- adjustable, open-end and open-end wrenches;
- a cutter or pipe cutter (in extreme cases, a hacksaw will do);
- pipe bender;
- calibrator;
- press pliers;
- expander;
- scan.
The connection of metal-plastic tubular products is performed by threaded and press couplings. In addition, compression fittings are used for this. Consider each option in more detail.
Mounting to a threaded sleeve. The sequence of actions in this case looks like this:
- cut the pipes.
Important! The cut plane must be strictly perpendicular to their longitudinal axis.This ensures that the end of the pipe and the edge of the coupling fit perfectly.
- disassemble the threaded fitting;
- put split rings and compression nuts on the pipes;
- insert the first pipe onto the coupling fitting, pressing the connection with a nut;
- put the second pipe on the opposite fitting and also fix it with a nut;
- fix the coupling body with the sliding wrench and then, using the ring wrench, tighten the first and second tightening nuts one by one. On this, the work on the coupling connection of metal-plastic pipe elements with a threaded sleeve will be completed.
Mounting to a press clutch. Compared to the threaded counterpart, the press-fit connection is much faster. Its implementation includes the following steps:
- cut the joints, as in the previous version, strictly at right angles;
- insert into the sleeves available in the press coupling to be connected to the pipe;
- crimp the junction with a special tool.
Important! Compress at both ends of the coupling at the same time.
Mounting on compression fitting. Perform this work as follows:
- cut pieces of the required length from the tubular products. Align their ends with a calibrator. Strip the edges with a round file or a sharpener with a burr and roughness;
- align the plastic pipe. As a result of this operation, you should get a straight, even section with a length of 10 centimeters before and after the cut;
- make an end chamfer up to 1 millimeter long at the ends of metal-plastic products;
- put the union nut and the split ring on the pipe first;
- lubricate the fitting with a silicone compound, and then put the tubular on it so that its end abuts with its entire plane against the edge present on the connecting element;
- tighten the nut all the way by hand without using a wrench. If twisting requires a lot of effort, it means that the nut is not threaded. When you easily tighten it all the way, do the following: hold the body of the fitting with one wrench and tighten the nut by no more than 2 turns with the other. In this case, a split crimp sleeve is compressed on a metal-plastic product, thereby ensuring the tightness of the connection between the pipe and the fitting.
Connection of metal-plastic pipes with products from other materials
In real life, it may be necessary to modernize an existing pipeline. In houses built during the USSR, utilities were made of metal. And although today such products are also present on the market, experts recommend stopping their choice on more modern pipe products - metal-plastic.
Of course, it is not practical to change the entire pipeline - it is just possible to replace its problematic metal sections. But for this it is necessary to know how metal-plastic pipes are connected with elements of a branch of an engineering network made of other materials.
Connection to metal pipes. For this, a crimp coupling for metal-plastic pipes is used, made of metal. The step-by-step instruction of this procedure looks like this:
- the end of the metal (old) pipeline clear of rust and dirt;
- screw the coupling using an open-end wrench;
- calibrate the product. Put on it a compression ring and a nut;
- put a plastic pipe on the free end of the coupling and tighten the nut.
Good to know! Paint and tow may come in handy. Their use contributes to the creation of a denser connection that prevents leakage.
Connection with polypropylene pipe elements. As a rule, products of this type are used to connect gas water heaters, washing machines, boilers. In this case, docking is performed using a special adapter coupling. This part has its own characteristics: the part of the coupling on the side where the pure polymer pipe will be connected is made of polypropylene. The connection is made by soldering or welding. But the connection of the metal-plastic pipe product is carried out to the metal part of the connecting part by screwing it onto the thread. That is, everything is simple here and no additional comments are required.
How are cast iron pipes connected
These products are mainly used in sewage systems. There are cast-iron pipes on the market, both with and without a bell. They are labeled SME and SMU, respectively. The tightness of the bell joints is ensured by a rubber gasket installed in the bell. Installation of smooth sections is carried out using various cast iron fittings: couplings, bends, elbows, tees, crosspieces, flanges, plugs and saddles.
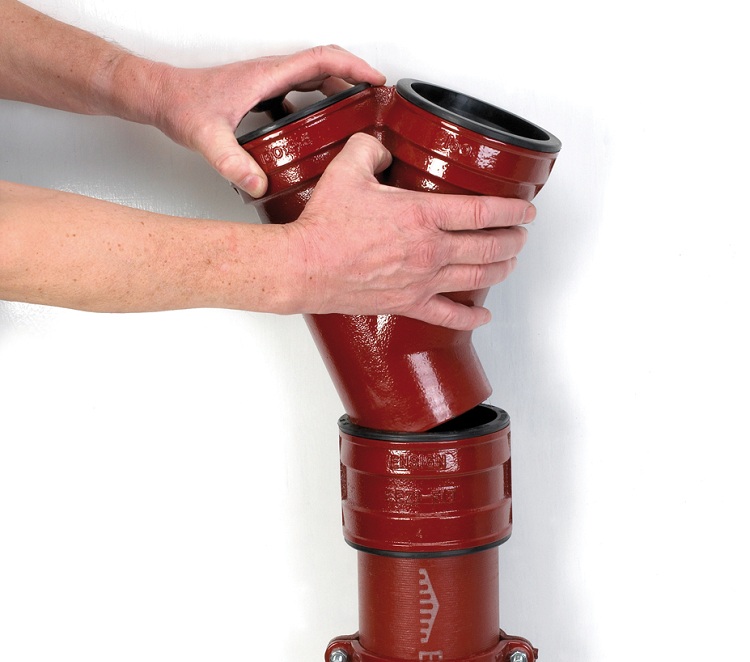
The connection of cast-iron pipes is most often carried out by the bell-shaped method, but in this case the junction may require additional sealing
As for the couplings, there are three types of them:
- Coupling made of cast iron. This part is a cylinder with an internal thread. Used to connect two pipe products with the same diameter.
- Adapter coupling. Design - two cylinders, on the inner surface of which there is a thread. Designed for coupling joints of segments with different diameters.
- Futorka. Thread cylinder on the outside and inside. Used to connect elements of heating systems.
The coupling for cast iron pipes at the end may have a socket or flange. This provides the opportunity to use various types of pipe products when installing the system. The most reliable way to connect cast iron pipes with metal-plastic pipes is to use a press fitting, one side of which is designed for joining with a metal-polymer element, and the other has a thread for metal.
Connect in the following sequence:
- evenly cut the end of the old pipeline;
- grease it with solid oil and cut the thread;
- wipe the thread and wind the seal around it. For this, an FUM tape is suitable;
- screw on the coupling.
Important! To prevent it from bursting, wind it by hand. If a leak appears after connecting the system, the coupling can be tightened.
The connection of cast-iron pipes with steel is carried out by means of pipes, at one end of which there is an adapter for steel, and at the other - a bell. Such parts are different in weight and length.
The sequence of stages of accession is as follows:
- insert the end of the old pipe into the socket;
- at the steel end, cut the thread;
- screw on it FUM tape first, and then the coupler;
- screw the steel tubular to the other end of the connecting part.
In the absence of leaks, you can put the created branch of engineering communications into operation.
How to mount a cast iron coupling with chasing joints
Embossed couplings have been used for more than a century. These parts are equipped with two sockets directed in opposite directions. Without certain knowledge, it is not possible to reliably connect the pipe to the coupling in this case. Therefore, we dwell on this issue in more detail.
- To seal the joint, it is necessary to have access around the entire circumference, both to the pipe and to the coupling. When installing the sewage system near the wall, a section of the wall will have to be hollowed out.
- A seal must be used to prevent leaks. As such, organic fiber soaked in oil (the so-called cabbage) is suitable.No worse results will be obtained when minting joints with a graphite gland.
- So that the seal simply does not fall in, the pipe is inserted into the sleeve until it stops.
- Minting the heel should be a few turns. Moreover, each of them must be sealed around the entire circumference of the pipe element.
If there is no special tool for minting at hand, home craftsmen offer such a solution to the problem: use a wide screwdriver or a steel ton pipe with a flattened end.
After sealing, the joint is necessarily covered with cement mortar.
Having carefully examined and studied all the existing options for joining metal-plastic and cast-iron pipes using couplings and fittings, you can easily easily correct the emergency situation in your water supply and sewage system and even repair the pipeline yourself.