The purpose of laying any type of communications is long-term and reliable operation. To achieve the best result, you must comply with the conditions - the use of modern high-quality materials and compliance with the installation technology. Only in this way can the long-term operation of the pipeline be guaranteed without violating its integrity and the need for repairs. One of the best offers on the building materials market today is pipes in polyurethane foam insulation.
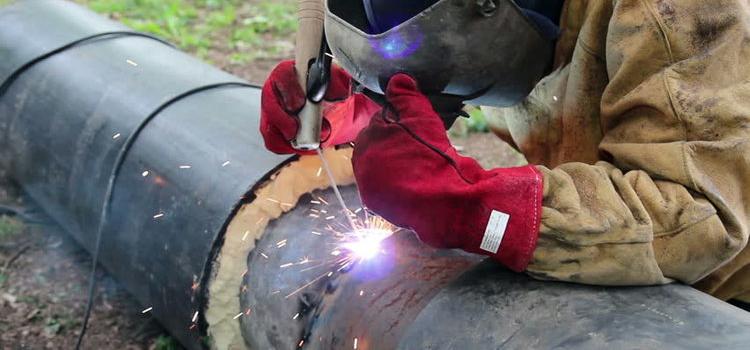
Installation of pipes with foam insulation is not difficult, regardless of the method of applying the insulating layer
Content
- 1 Laying communications on a new technology versus old methods
- 2 The main advantages of the pipeline in polyurethane foam insulation
- 3 Properties of high-tech insulation
- 4 Properties of polyurethane foam and technology for the production of insulated pipes
- 5 Materials for mounting pipes in polyurethane foam
- 6 Phased installation technology
Laying communications on a new technology versus old methods
Installation work on laying quickly rusting and heat-losing pipes is a thing of the past, they were replaced by the installation of pipes in polyurethane foam insulation. The advantages of fast laying and increasing the efficiency of communications are the main reasons for their demand.
The high-tech pipeline with polyurethane "shell" was quickly appreciated by specialists in pipe laying. In terms of thermal conductivity, PPU is slightly inferior to expanded polystyrene, but surpasses in terms of manufacturability. This material is resistant to aggressive reagents, with the exception of universal solvents and acids of high concentration.
Note! Seamless insulation with a “jigsaw” connection allows for more efficient laying in difficult climatic conditions of a pipeline with a coolant of any configuration and functionality. Heat loss is minimized by isolating the foam.
Technological installation of pipes in the PU foam insulation involves laying communications in a non-channel way, which ensures a longer period of operation. Rethinking the process of warming the polyurethane foam pipeline with the pre-insulated method was adopted by advanced companies in providing heat supply and modern communications.
The main advantages of the pipeline in polyurethane foam insulation
The installation of pipes with polyurethane foam according to the new technology has undeniable advantages relative to previously used heaters, such as glass wool, and methods of thermal insulation:
- large amplitude of the temperature regime of use in northern latitudes with high-temperature coolant of the system (within -80 ° С outside and + 130 ° С inside);
- trenchless laying of the pipeline;
- extended service life of communications without the need for repair (40-50 years);
- high efficiency of the heating system with a low percentage of heat loss (about 5-10%,);
- saving resources used for heating the coolant;
- quicker and more economical repair of pipes in polyurethane foam insulation in case of a possible breakthrough or damage to communications;
- pipeline construction time is reduced significantly;
- minimal absorption of moisture from the soil relative to mineral wool and other insulation;
- the ability to quickly enter the heating main into operation, thanks to well-thought-out installation technology;
- resistance of the pipeline in PUF to mechanical stresses during seismic shocks and other unexpected loads on communications.
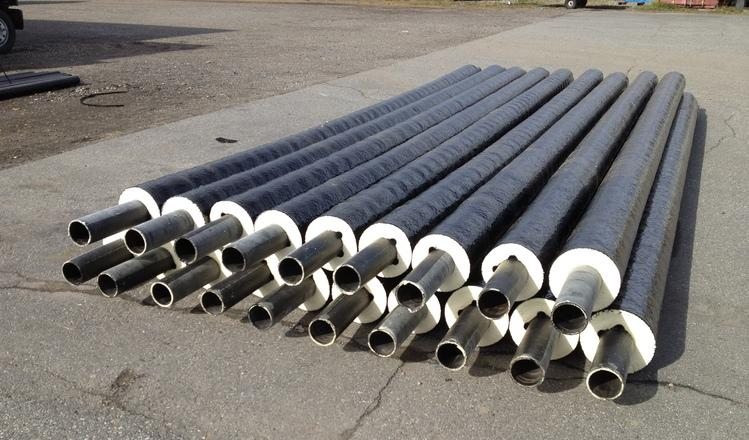
Modern industry produces pipes pre-insulated with polyurethane foam, which have a lot of advantages.
Important! The use of pipes in polyurethane foam insulation in industry and in laying communications of any type is an additional savings. This is the absence of a surcharge for “cold” transportation with forced heat loss from the boiler room to the facility.
Properties of high-tech insulation
Old heat-insulating materials, although cheap, could not guarantee the protection of pipes against freezing at extreme temperatures in winter. Tile insulation was not convenient for installation, and it took a lot of space to install it. An innovative material in the form of a finished insulating “shell” made of polyurethane foam, an envelope of a pipe, has become the best solution.
Shell - insulation made of polyurethane foam in the form of a hollow cylinder cut to the side or a base consisting of two joined parts for covering the pipe.
Note! Due to the fact that everything is thought out and produced in a form ready for installation with a convenient connection, it is quick and easy to collect and stack such communications!
The insulation halves have an effective type of connection - “crest-groove”, which resembles children's “puzzle” puzzles, and this eliminates voids or poor fit. This method of connection provides an undeniable advantage for warming heating mains operating in extreme conditions at any facility.
The idea of a polyurethane "shell" was further developed, and specialized enterprises began to produce pipes under a layer of finished insulation. These are the so-called "pre-insulated" pipes, that is, pre-insulated polyurethane foam.
Installation of pipes in polyurethane foam insulation has obvious advantages:
- sophisticated technology;
- quality control of the pipeline;
- simultaneous laying of communications and their insulation;
- guaranteed tightness of insulation;
- reduction in the cost and costs of the construction of heating mains.
The less time it takes to lay the pipeline, the lower the cost of costs in terms of workday. At the same time, it does not require laying to a great depth or constructing a channel with concrete stops. For rotary sections use tees and couplings with pre-insulation.
Properties of polyurethane foam and technology for the production of insulated pipes
The unique properties of a new generation of sealed insulation is explained by its structure - low density with an abundance of closed bubbles of finely porous material.
Briefly, the production of products with polyurethane foam occurs according to this scheme:
- Chemical raw materials are brought to standard by extrusion technology - a sharp heating to a predetermined temperature.
- The shell or shell is formed from the new material in the mold according to the specified parameters - length, width and thickness.
- From a liquid state, polyurethane foam is converted into a solid form of a certain format. Correct parameters are set according to the standard - from 3 mm to 12 mm thick and from 32 mm to 1420 mm cross-section.
- If there is a need to produce shells for wider trunk pipelines, polyurethane foam is poured into a wider form and a larger thickness is set - up to 120 mm.
All parameters are regulated by GOST 30732–2006.
Materials for mounting pipes in polyurethane foam
When buying pre-insulated pipes in polyurethane foam for heating mains, it is important to pay attention to manufacturers and the quality of components - leaks and depressurization are possible. In order to save money, some people buy pipes of a new type, but they save on connecting parts. Even if tees for pipes of a different type fit in diameter and thread, such a pipeline cannot be called reliable.
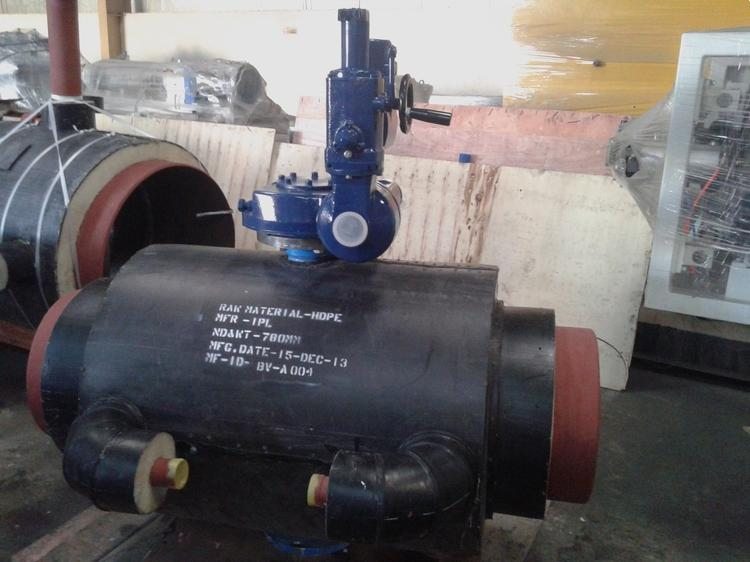
Pipes insulated in the factory must be connected with fittings of the same manufacturer, they must also be labeled with technical specifications
Important! All products must be purchased with certificates, technical documentation and instructions for installation and operation, as well as indicating GOST.
For the installation of PPU pipes by technology, you may need:
- supporting elements;
- enclosures with a locking connection;
- gaskets;
- Ball Valves;
- shrink sleeve;
- bends;
- fittings;
- Z-shaped parts;
- couplings and tees;
- galvanized pipes for the aboveground part of the heating main.
Phased installation technology
In order to outline the inshell pipe laying process, it’s worth familiarizing yourself with the main steps:
- Preparation - stripping the insulation edge at each pipe end.
- Preparation of the welding machine for the work by which the pipes are connected, the joints are clean and dry.
- The reliability of welding at the final stage is best checked by a flaw detector.
- If a half shell shell is put on the pipes, tightness is maintained at the junction so that there is no gap. For pipes of small diameter, a heater with one cut is suitable, wide pipes are covered with two half-cylinders.
- Be sure to use a heat shrink sleeve, and the entire space at the seams is filled with mounting foam to achieve complete tightness. Until the curing sealant has completely hardened, the coupling can be slightly seated or moved.
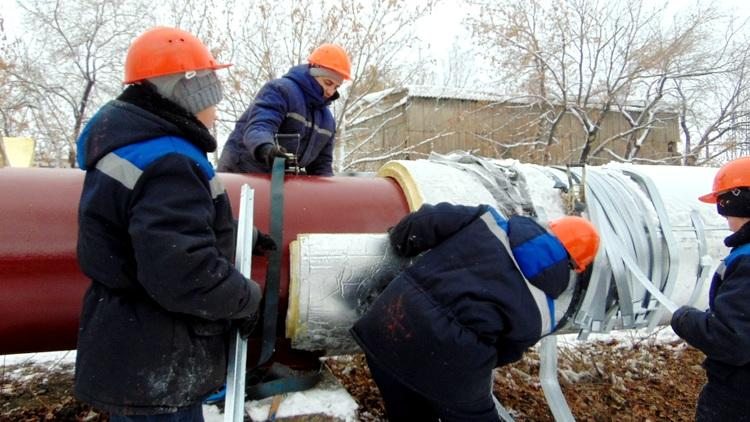
Pipes of large diameters are covered with a shell consisting of two parts; they are fixed with clamps, belts or metal tape
Important! Covered with polyurethane foam and other heaters, the elements are closed with asbestos cloth at the ends during welding, so as not to ignite. According to GOST, pipes are welded with full fusion of the joints at the junction.
For the insulation of pipe joints, different materials are used:
- in components with PPU - a sealant, a casing with galvanization and adapters with PPU;
- with shell - foil adhesive tape, shrink tape, casing;
- with a casing made of galvanized steel and parts with polyurethane foam - shrink tape, gasket, casing and accessories in polyurethane foam.
The installation of pre-insulated communications is usually carried out in large volumes - for heating, an external pipeline and hot water supply. A layer of PPU with proper installation is a guarantee of perfect functioning. For a long period, the system does not leak, does not require repair.
Wide pipes require additional fixing of the shell halves. Fit:
- clamps;
- foil tape;
- steel wire;
- metal tape.
Previously used shells can be reused if its quality has not been damaged during the initial installation.