High-quality components and pipes pre-insulated for heating systems - a guarantee of long-term operation of communications in any climatic zone. The technology of production of these products and qualified installation with the observance of the technology ensures the smooth operation of the heating system for a long period without the need for repair.
Content
What is the difference between pre-insulated pipes and others?
For those who are familiar with the “sandwich” system for chimneys, a pre-insulated pipe with PU foam will seem like a “related” product. The same cylinder in a wider workpiece, but the gap between them is not filled with mineral or basalt wool, but with foamed and baked synthetic filler. At the moment, such a development is considered the most high-tech achievement in the industry.
This method of pipe insulation for heating networks in practice confirms its effectiveness and reliability - high efficiency of the pipeline with a service life of at least 25 years. A pre-insulated product is able to withstand short-term amplitude surges of the coolant at a record low ambient temperature in the winter. The specific shape of the product with internal insulation is used not only for hot water, but also for transporting other liquid and gaseous media.
The main pipe is steel, the outer layer is not always solid metal with galvanization, especially when this is not necessary. The polyurethane foam interlayer can be protected by a flexible shell wrapping a porous filler in the form of a spiral. Each layer of multilayer products is manufactured according to a special technology, equipped with a system of special moisture control of the insulating layer and possible defects in the trunk segment.
The pipe “in the pipe” does not look like an assembly, but as a whole product, due to the tight adhesion of the insulating filler. Pre-insulated products are recommended for practical installation in heating systems. The outer layer is designed to protect PPU from getting wet, and also provides resistance to external influences.
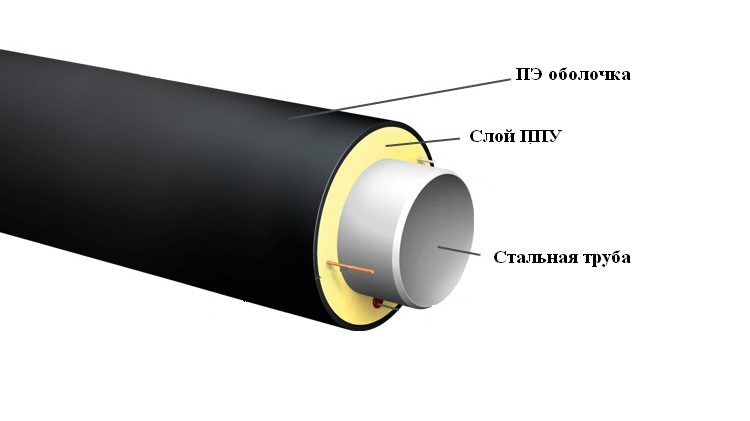
Pre-insulated pipes are similar in design to sandwich chimneys, but the outer shell may be made of polyethylene
Components of pre-insulated pipes
The pipe in the PU foam insulation is produced from the following components:
1. Rod base or functional steel pipe. Certified products are manufactured in accordance with GOST:
- 8731;
- 8733-77;
- 10704;
- 10706;
- 20295;
- PB 03-75-94, etc.
2. The inner thermal insulation layer is produced from polyurethane foam raw materials from leading manufacturers. From domestic products, the production of Izolan, Dau, Elostokam and Huntsman, whose products are not inferior to import systems, reached a high-tech level. Their finished fillers have a long warranty period of operation at maximum external and internal load, even water hammer or short-term temperature increase up to 150 ° C.
3. The outer shell or protective casing is designed to protect the foam layer from damage and moisture.The lack of access to moisture from the outside ensures the safety of all layers of pre-insulated pipes - from corrosion of the core base and crumbling polyurethane. The polyethylene sheath is produced in accordance with GOST 16330 from thermo-light-stabilized raw materials of high density in black. It is possible to use a shell of a different type - according to other standards.
The most popular pre-insulated steel pipes (PPU-PE GOST 30732):
- 57*3,5-1;
- 57*3,5-2;
- 76*3,5-1;
- 76*3,5-2;
- 89*3,5-1.
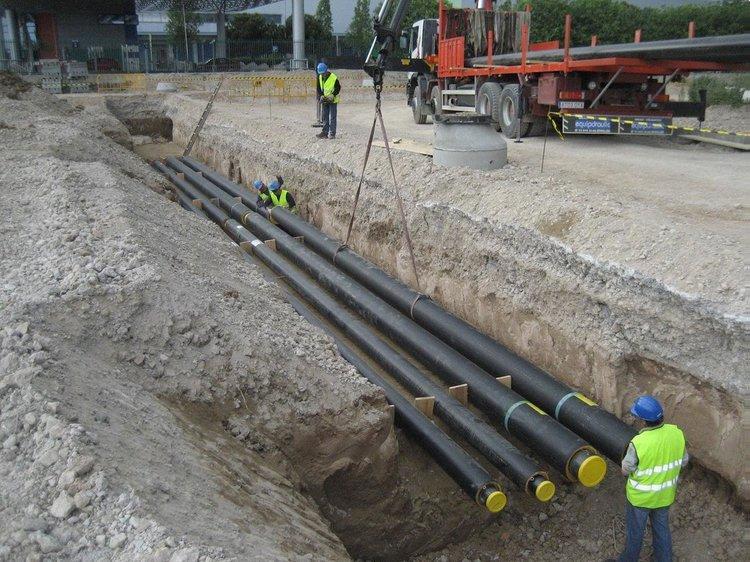
The outer shell protects the pipes from the harmful effects of the environment and helps to increase the life of the heating main
Product Quality Requirements
All processes for the production of pipes with polyurethane foam are carefully monitored for compliance with standardization standards. For example, foaming and hardening of polyurethane foam is a quick process where deviations from the norms are unacceptable. In just seconds, the raw material takes on its final appearance and is ready for use. There are PPU of different density and stiffness - within 1 kg / m³. Its isolated porous cells also have different sizes - up to 1 mm in diameter.
Requirements for heat-insulating filler:
- water absorption of polyurethane foam by volume - within 10% (tested at 1.5 hour boiling);
- density - within 60 kg / m³;
- compressive elasticity - from 0.3 MPa (within 10% deformation in all directions);
- the change in product length after warming up to 110 ° C should be minimal - up to 3%.
Mandatory testing on the main quality indicators pass not only the pre-insulated pipes themselves, but also all components. Before implementation, they are tested in a laboratory way for density, closed pore size and thermal conductivity.
It is interesting! The foam in the insulating layer resembles a yellowish confectionery cream after whipping. But this homogeneous paste has a dense, fine-meshed structure that does not settle, does not stick together. The ends of the PPU insulation do not have a protective layer, and it is obvious that thermal protection is not more than 1/3 of the total thickness of the product.
One of the characteristics of pre-insulated pipes with polyurethane foam is the adhesion of the outer and inner layers. For this, the technological standards must be met:
- cleaning the surface of the steel pipe from rust, with the obligatory formation of roughness, with which foamed polyurethane foam has better adhesion;
- maintaining a predetermined temperature regime for uniform foaming of raw materials;
- discharge treatment of the inner shell for greater adhesion to the foam filler.
Due to the properties obtained, pre-insulated pipes are used in the construction of oil, gas and steam pipelines. They are also widely used in heating networks for hot water supply and in various technical pipelines - in workshops in hot production.
Important! PPU was produced in several ways, but today the practice has become established - to take carbon dioxide and Freon 141b (F-141b) as the basis. This mixture is dangerous, therefore it is used only in an industrial way, due to the explosiveness of the probability of fire. But foaming reagents give the maximum effect when obtaining the necessary content in the annulus. All norms are regulated by a single standardization - GOST 30732-2001.
Advantages of pre-insulated pipes with polyurethane foam
There are many positive qualities and similar products.
- Installation of communications in a short time with minimal labor.
- Decrease in heat losses to a minimum (2% against 40%).
- Improving the efficiency of the heating system to the maximum possible performance.
- Increasing the life of communications by 3-5 times (relatively old technology).
- The opportunity to reduce the cost of frequent overhauls, due to minimizing ruptures of pre-insulated pipes and their joints.
- The operation of the remote control system (UEC).
- There is no need for grounding and arrangement of the drainage system.
- Protection of pipes against corrosion and other external negative factors.
- Pipes in polyurethane foam are less susceptible to destruction from chemicals and aggressive media.
- Safety PPU for the environment.
- Maximum preservation of the temperature of the transported substance, due to the absence of “cold bridges”.
- Minimum thermal conductivity with a small layer of thermal insulation.
Manufacturing technology of pre-insulated pipes
A well-established process involves pouring foaming raw materials into the gap between the outer shell and the steel pipe. The technology is thought out so that the production of products for heating plants is carried out with a minimum of operations.
PPU foam with minimal thermal conductivity is poured over a steel pipe, which is fixed by a hoist on a special assembly table. Centralizers and SODK control the process of forming products. The product is placed by an electric winch into the outer shell. The conveyor moves the product into the heat chamber - for further thermostatics.
Fan heaters heat the inner surface of the pipe with a hot air stream to 350 ° C - the hot base for filling the polyurethane foam is ready. A special device rotates the pipe on a rotary axis. On both sides, the ends of the product are equipped with plugs with small drainage gaps for wire outlet air.
Screws fasten the plugs to prevent the outflow of uncured raw materials from the space between the pipes. The filling machine is regulated on the control panel, where the basic filling parameters are set. They depend on the type of raw material, length and shape of the pipes. The watering can for injection of the PUF of the filling machine is brought to the hole in the pipe and the mixture is quickly introduced. A further goal is the hardening of the thermal insulation layer in the annulus.
Further, the products are transferred to the site of control and laboratory quality control. Certified products are sorted, labeled and packaged. Upon completion of the waterproofing process at the ends of pipes for heating networks, they are stacked on shelves - up to 5-6 products.
Note! In Europe, the basic requirements for preliminary insulation from polyurethane foam for laying underground utilities were regulated by the European standard - EN253. It was reflected in the accompanying documentation.
In Russia, manufacturers of pre-insulated products, technologists and developers have developed a single Russian standard - GOST 30732-2001. The standardization entered into force on 01.07.2001. The regulatory document reflects the requirements for PPU insulation products and components for pre-insulated pipes. The operation of pre-insulated products in communications involves taking into account the thermal conductivity of gases. This indicator increases with increasing temperature. However, this indicator is not able to significantly affect the pipes themselves and the insulating layer of polyurethane foam.