PPM pipe is used to protect the pipeline structure from environmental influences and other negative factors. Such protection is one of three types of pre-insulation, which are widespread when laying pipelines for various needs. The excellent performance and rather long service life of this composite material allows not only to minimize the percentage of heat loss, but also protect the pipeline structure from mechanical damage.
Content
Why use PPM pipes?
Heating networks transport heat to consumers and it is very important that heat losses are minimized. For this, they use thermal insulation. Earlier, heat-insulating materials complicated the process of laying pipelines. Pipes in the PPM insulation, which appeared not so long ago, helped to cope with this problem.
Foam-thermal insulation is a layer of rigid material that has a closed-cell structure and consists of polyurethane foam and a mineral additive. Today, the production of PPM pipelines takes place on an industrial scale. The quality of the foam-polymer protective layer is growing, which is reflected in its operational characteristics.
Helpful information! Mineral additives, which are part of this material, can give it high strength. Due to this, the PPM pipes are resistant to mechanical stress.
Perhaps one of the most important qualities of a foam-polymer-mineral material is vapor permeability (this indicates that such thermal insulation practically does not absorb drip moisture). PPM insulation does not coalesce over time and does not lose its unique characteristics.
The materials used for the production of such tube shells are cheap, but at the same time they are very strong and reliable. In the process of forming such a structure, it is placed in a collapsible form. Before being placed into the mold and applying the PPM insulation, it is cleaned of oxides and contaminants using the firing method.
Advantages and disadvantages of foamed polimermineralnoy thermal insulation
Foam-thermal mineral insulation has a number of operational advantages in comparison with other insulating materials. First of all, these advantages are associated with its properties.
Consider the main advantages of using PPM isolation:
- the material does not deteriorate over time. During operation, its thickness does not change;
- PPM insulation has a low coefficient of water absorption;
- such insulation has low thermal conductivity. Thanks to this, the use of a foam-polymer-mineral sheath makes it possible to better retain heat in the mains. Heat loss, as a rule, is no more than 2–4%. If we compare the same indicator of mineral wool, it is several times higher;
- low cost in comparison with other options of heat-insulating materials (for example, polyurethane foam);
- foam-polymer-mineral sheath increases the operational life of the pipeline (more than 30 years);
- trunk with such insulation does not require large maintenance costs. In addition, the risk of an emergency in the system is reduced;
- if the pipeline gives a leak, the foam-polymer membrane will dry out and not lose its properties;
- there is no need to mount an operational remote control system (SODK) in order to check the condition of the thermal insulation layer.
Like any material, foamed polymineral insulation has some disadvantages:
- the heavy weight of this material increases transportation costs. The installation of such thermal insulation is carried out, as a rule, with special equipment;
- heat losses in such a system will be greater than when using a polyurethane foam (PUF) shell;
- PPM insulation is not completely sealed. In order to protect the pipeline from the harmful effects of corrosion, it is necessary to additionally apply an anti-corrosion agent on it.
Features of PPM insulation
Foamed polymer and additional fillers are used to produce such insulation. Fillers for such material most often serve:
- ash;
- sand;
- toxins.
Thanks to additional additives, the strength characteristics of the foam-polymer-mineral membrane increase. The high strength of this shell allows you to protect pipes from mechanical stress, which is a big plus.
Installation of insulation PPM is carried out on the outside of the pipe. The PPM shell, as a rule, contains 3 layers:
- anticorrosive layer, the thickness of which is 5-10 millimeters;
- main heat-insulating layer;
- the protective layer, which is external and in order to protect the pipeline from mechanical stress, has a high density. The thickness of this layer, as a rule, is 10-15 millimeters.
Note! The lengths of the ends of the pipe, on which there is no foam-polymer insulation, are usually 15 centimeters with a pipe diameter of up to 219 mm. For pipes with a diameter of 273 to 820 mm - 20 centimeters.
PPM insulation can be applied to pipes that have a diameter of 32 to 820 mm. The length of the pipe can reach up to 12 meters. The pipe itself can be welded or seamless. Such products are regulated by GOST 8731, 10704, 8733 and 20295.
Characteristics of PPM pipes are presented in table No. 1.
Table 1
Pipe diameter mm | Diameter with insulation, mm | The thickness of the foam polymer insulation, mm |
820 | 960 | 70 |
720 | 860 | |
630 | 750 | 60 |
530 | 650 | |
426 | 514 | 44 |
377 | 462 | 42,5 |
325 | 412 | 43,5 |
273 | 359 | 43 |
219 | 309 | 45 |
159 | 257 | 49 |
133 | 205 | 36 |
108 | 180 | |
89 | 45,5 | |
76 | 150 | 37 |
57 | 46,5 | |
40 | 121 | 40,5 |
32 | 44,5 | |
25 | 48 |
In addition to pipes, thermal insulation can be applied to such elements of pipelines:
- transition elements;
- bends;
- tees and other shaped components.
Pipes with PPM insulation are often used for laying heating mains, as well as water pipes that transport hot water. According to SNiP 41-02-03, such pipes can be used in the installation of various coolants, the temperature of which does not exceed 140 ° C.
Consider the main types of gaskets that are allowed for PPM pipelines:
- channelless closed (underground);
- closed channel;
- open (aboveground).
PPM pipes were developed by domestic specialists and in their production the climatic features of the regions are taken into account. Thus, we can conclude that they are adapted for our country.
Pipe production
The shell of the foam-polymer insulation is monolithic and is superimposed on the pipe during the production process. For pipes with section sizes from 57 to 820 mm, shells with a thickness of 32 to 88 mm are used. The adhesion properties of this polymer material create reliable thermal insulation for heating systems.
In the production of these pipes, three layers of insulation are formed, which have different properties.The density indices of these layers are also different. This design allows you to cope with difficult operating conditions.
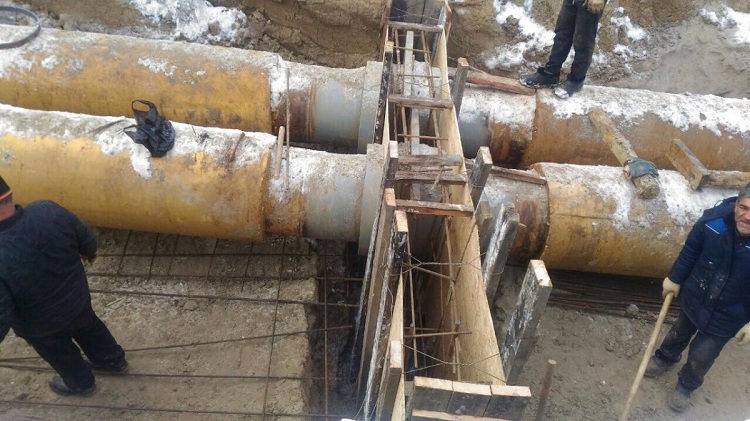
The production technology of pipes allows you to operate them in difficult conditions, for example. in harsh regions
Consider the stages of production, coated with foam-polymer insulation, pipes:
- First, a foamed polymer and an additive of ash, sand or slag are prepared.
- Next, a steel pipe or fittings are prepared, on which thermal insulation will be applied.
- At the third stage, the foam-polymer-mineral mass is poured into the workpiece, where the centered steel pipe is located.
- After the PPM pipe is ready, it is tested for quality.
The filling of the mass planning material into the mold takes place in stages. First of all, it is necessary to determine and measure the percentage of the individual components of the insulating material. Different factors influence the calculation - the thickness of the insulating layer, the dimensions of the pipe section, etc. After certain calculations, the individual components of the composite are dosed and combined. The resulting mass is delivered to the mold. It contains a centered pipe. After the foam-polymer mass hardens - the mold is removed and the finished part is sent for testing. The entire production process takes no more than one hour.
Note! The mold itself is a split hollow cylinder. The base of the form is motionless, and the upper part is able to open. On both semi-cylinders special sealing elements are placed, due to which the necessary sealing is achieved.
The price of PPM pipes varies depending on their size, thickness and density of the insulating material. In addition, well-known manufacturers produce pipes more expensive, but the quality of such products is higher. The cost of the insulating material is calculated based on its thickness, pipe diameter and footage. The price of 1 meter of foam-thermal insulation varies from 550 to 9500 rubles.
PPM pipes are very effective and are used for various heating systems, as well as water pipelines that transport hot water to consumers. The cost of these products varies and depends on the design features of the pipes and foam-polymer insulation. If you wish, you can save a lot on laying a trunk with such insulation. In addition, PPM communication does not need routine inspections and has a rather high operational life, preserving its heat-holding properties regardless of the period of service. The laying of such communications can be carried out both open and closed. Hydrophobicity and excellent strength indicators allowed them to spread widely and take one of the leading positions in the market of insulation materials.