The issue of isolation of pipelines from environmental influences remained open until the technology of protection of polyurethane shell was introduced into production. Pipes in insulation made of polyurethane foam have a longer service life and are more protected from corrosion and stray currents. The indicators of heat loss in networks protected by polyurethane foam insulation are reduced to the standards prescribed by SNiP 2.04.14 and SP for design.
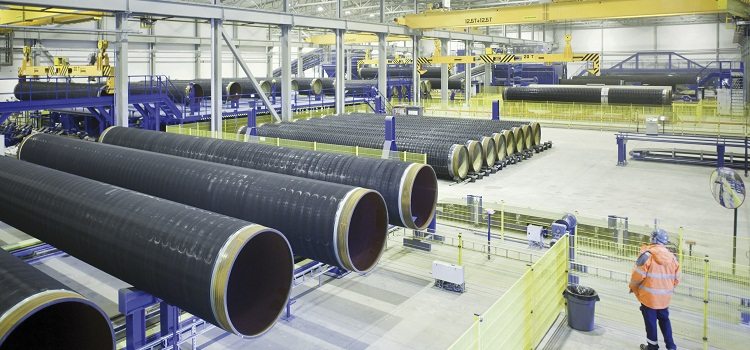
The production of pipes in polyurethane foam insulation can effectively solve the problems of thermal insulation of heating mains and other highways
Content
The process of manufacturing pipes in polyurethane foam insulation
Production involves the receipt of the finished product on the principle of "pipe in pipe". The steel product of the required diameter is placed on the centering supports and enters the outer pipe-shell. For pipes intended for internal laying, a polypropylene waterproofing pipe is used as the second sheath pipe. For products used when laying outdoors, galvanized steel is used. The uniform space between the two pipes is filled with polymer components, which over time harden and form a single monolithic insulation.
The technological process by which the production of pipes in insulation is carried out includes 8 successive stages. The execution order is controlled by GOST under the number 30732-2006 (earlier version - 30732-2001).
- The first stage of production work will be quality control of the prepared materials. Control is necessary for the timely detection of defects on the surface of the inner steel pipe and polyethylene (galvanized) pipe pipe). Raw materials with flaws detected are subject to rejection. At this stage, certificates, passports and other documentation are prepared and verified.
- The preparation of the outer surface of the inner steel pipe. If the surface of the steel is not sufficiently treated, sufficient adhesion to the PUF layer will not be ensured. The adhesion is adversely affected by the presence of oil or grease stains, patches of rust, scale, dust and dirt contaminants. For optimum processing, shot blasting, shot blasting or brushing is used. Sometimes flame or chemical treatment is used.
- The preparation of centering elements and UEC systems is being carried out. At a constant uniform distance from each other, centralizers are distributed that hold the steel inner pipe in the exact geometric center of the protective polyethylene or galvanized shell. A copper wire is drawn through the holes (“ears”) of the centralizers, providing a system of operational remote control (in short - UEC).
- The steel pipe with the extended cable of the UEC system is placed in a protective sheath. For this, track pulling equipment is used. The use of this device provides an equal distance between the surface of the inner pipe and the protective sheath. This condition is especially important for the same foam layer throughout the product.
- The temperature stabilization of the workpiece is performed.The pipe heats up to a temperature of +230 degrees. This procedure allows to achieve maximum adhesion of the PUF shell with other surfaces.
- At the ends of the structure, casting flanges are installed, intended for further pouring of polyurethane foam. One of the flanges is equipped with holes necessary for bleeding air in the annulus. A high-pressure casting machine is used to fill insulating material. The pipe is placed at an inclination of 1-15 degrees to the absolute horizontal.
- To improve adhesion and achieve high performance, a product with a flooded layer of polyurethane foam is sent to a storage warehouse. Casting flanges are removed from the pipe, excess foam is cleaned off.
- The finished product, which has passed the aging period, undergoes rigorous technical quality control. The degree of compliance with certain norms of SNiP is determined.
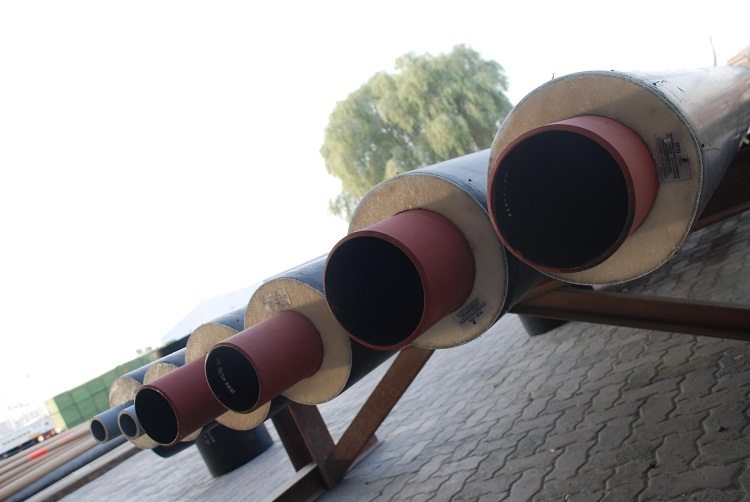
The pipe in PPU is a three-layer construction in which there is a steel billet and two layers of insulation
Sometimes the process of pouring polyurethane foam is replaced by the technology of spraying the material onto a continuously rotating steel billet. GOST assumes the release of products with reinforced and conventional insulation. Also taken into account the fact of the mandatory presence of segments and two ends of the pipe, devoid of insulation. This measure is necessary to simplify installation work.
Using ready-made PPU shells for pipes
In addition to pouring and spraying the material, there is a method involving the production of individual shells for thermal insulation. It can be used to isolate a finished pipeline or cover pipes with a non-standard relief. The pipeline is ready for operation when the PPU shell is fixed to a previously prepared surface with glue specially designed for thermal insulation.
Before gluing steel and polyurethane foam surfaces, it is necessary not only to clean the pipe from contamination, but also to treat it with mastic. For a stronger connection, retaining clamps are used.
Important! The use of adhesives and mastics does not contradict the norms of SNiP relating to the laying of heating networks with insulation.
Insulating PUF shells are produced by mixing under high pressure two chemical components. Material is poured into molds of various thickness and diameter. Due to the variety of shapes, manufacturers offer the customer a wide selection of shell thicknesses designed for various operating conditions.
Shell segments have transverse and longitudinal locking joints, thereby reducing the risk of crevices. When gluing segments directly on a steel pipe, the insulation seam is almost completely sealed, approaching in its properties to a monolith. The shells can be covered not only with a metal or polymer casing, but also with fiberglass or armofol.
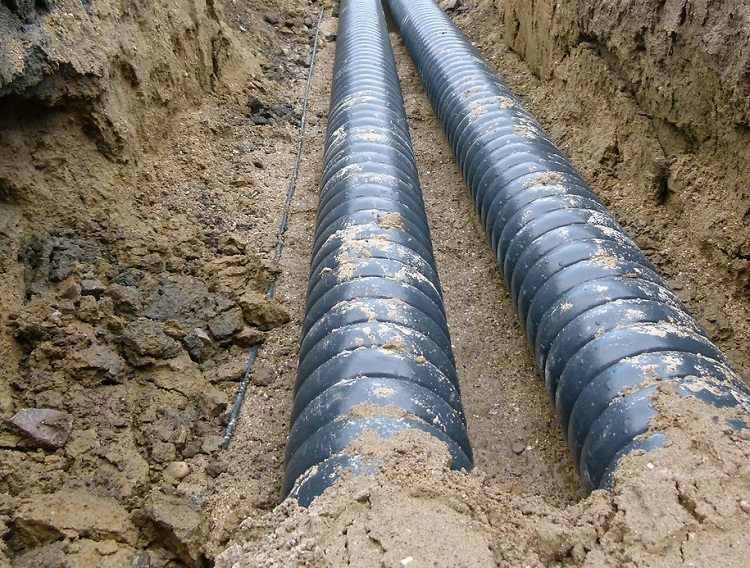
For underground installation, pipes with an outer shell of polymer are used, since they are not subject to moisture and corrosion
Requirements for the production of PPU pipes according to SNiP
The provisions of SNiP 41-03-2003 determine the requirements related to the design of structures in thermal insulation. The requirements related to the manufacture of PPU pipes will be as follows:
- SNiP 41-03-2003 states that at a temperature of the contained substances and coolants in the range from +20 to +300 degrees and with any laying methods (channelless laying is not considered), heat-insulating materials with a density not exceeding 200 g / m3 are used. The maximum value of the coefficient of thermal conductivity according to SNiP in the dry state and at an average operating temperature of +25 degrees is 0.06 W / (m * K).
- If the temperature of the coolant exceeds +300 degrees, SNiP allows the use of heat-insulating materials with a density of up to 350 g / m3.
- When choosing a material for thermal insulation and its coating layers, the resistance of other structural elements to chemically active substances in the environment is taken into account.
- The normative document defines the thickness of thermal insulation.
SNiP imposes obligations on pipe manufacturers in insulating materials on the availability of certificates (hygienic conclusion, fire certificates, certificates of conformity of products).
Also, in accordance with the norms of SNiP, tests are made of the strength and density of finished products in insulation and fittings. The main tests are carried out hydraulically.
The provisions of the joint venture for the design of PPU pipes
The presented Code of Practice (SP 41-105-2002) contains standards and guidelines related to the design and construction of heating networks from steel ("black") pipes and fittings coated with industrial insulation from polyurethane foam.
Important! The implementation of the actions described in the joint venture is correlated with the mandatory requirements set forth in SNiP 41-03-2003 and other SNiP specifying insulation materials. The joint venture refers to PPU pipes, the production of which was carried out in accordance with GOST under the number 30732.
The provisions of the joint venture determine:
1. The presence of linear conductors for UEC, monitoring the state of humidity.
2. Steel grades for operation in areas with an outside air temperature below 0 degrees:
- up to -30 degrees - steel grades 10, 20 and Vst3sp5 are used;
- up to - 40 degrees - brands 17ГС, 17Г1С or 17Г1СУ;
- up to - 50 degrees - brand 09Г2С.
3. The joint ventures allow a margin of corrosion of the wall thickness of the inner pipes, as per the customer’s request to a specific organization.
4. If the possibility of ovalization of the pipe under the weight of the soil appears during internal installation, the joint venture recommends the use of reinforced walls.
5. The ends of the pipes, not insulated in the factory for ease of installation, must be coated with anticorrosion mastics for the entire installation time.
6. According to the joint venture, the production of heat-insulated pipes with a diameter of 530-720 mm is designed for channel-free laying of heating networks throughout the territory of the Russian Federation and neighboring countries.
7. The joint venture also obliges manufacturers to supply elements complete with PPU pipes, such as:
- panel reinforced concrete supports;
- axial compensators;
- starting compensators;
- end-to-end insulation elements;
- polyurethane foam components for filling joints;
- sealing sleeves made of rubber or polymers;
- devices of systems for remote control.
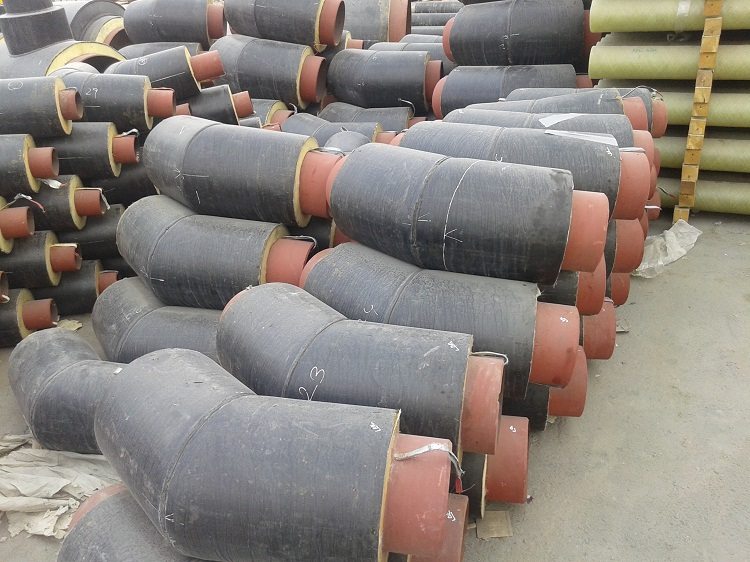
The factory producing PPU pipes also produces a variety of fittings, supports and other components for this type of product
In addition, the joint venture stipulates the conditions of static strength and recommends that manufacturers make the necessary calculations using desktop programs.
Equipment for creating polyurethane foam insulation for pipes
Production lines are offered both as a complete product and as individual work units. The option is practiced when the customer purchases from the company a set of drawings for independent production of individual production sites. The complete sets of production lines depend on the requirements for capacity and workshop area. Standard equipment is:
- live rolls of steel pipes;
- chain conveyor;
- live roll of polymer products;
- live rolls of finished steel pipes;
- filling machines;
- filling tables;
- chambers for heating blanks;
- tilter of finished pipe structures;
- tilter of polyethylene pipes-shells;
- assembly table;
- hydro power station;
- storage device.
One of the most important elements of the production line is a machine for pouring polyurethane foam, operating under high pressure. Filling machines allow you to create pipes of all diameters specified in the relevant GOST. Some machines are equipped with programmable controllers. Such equipment has up to 60 different pouring modes.
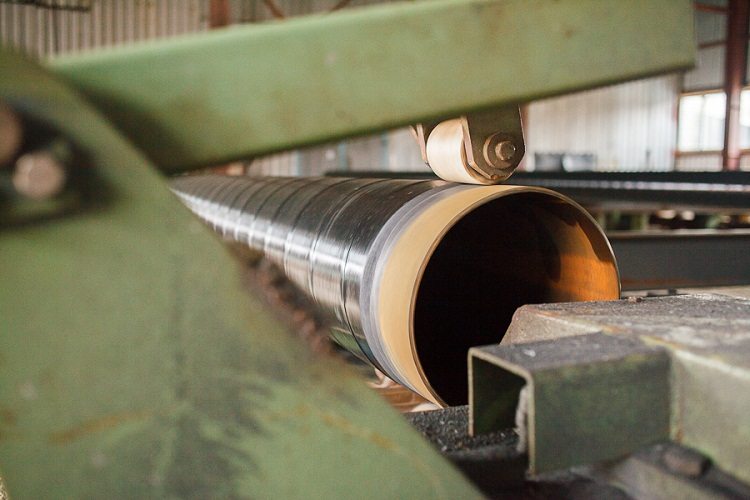
The plant for the production of PU foam pipes should have equipment for working with different types of external shells
It is interesting! Under optimized operating conditions, the minimum time spent filling one segment can be 0.5 mm.
Also, special equipment will be required for galvanizing the outer shell. For the manufacture of plastic pipes-shells, threaded and welding equipment for working with polymer materials will be needed.
Equipment using PPU pipe insulation technology has a standard package:
- two containers for mixing components;
- pump for injection;
- hydroelectric power station with a capacity of 3 kW;
- electrical cabinet with an automated control system;
- polyurethane foam injection apparatus.
Polyurethane foam filling machines have differences in performance. From this indicator, accordingly, the cost of the machine will depend. In order to make the right choice, when buying, you should focus on the planned diameter of the manufactured products. It is necessary to calculate the amount of polyurethane foam injected every minute, and determine the productivity of the machine from this indicator. For example, the diameter of the pipeline with an inner pipe diameter of 426 mm will be 560 mm. To fill such an amount of space will require 87 kg of insulating material. This means that the productivity of the filling machine is required with an indicator of 96 kg per minute.
When buying networks of equipment for pipes in insulation, it should be borne in mind that installation, commissioning, and the cost of training personnel are required.
All that is needed to organize the production of PPU pipes is a detailed study of the intricacies of the production process and the provisions highlighted in GOST, SNiP and SP for pipes in isolated materials. Equipment for pouring or spraying the PUF layer (or shell) is selected in accordance with individual performance requirements.