When installing pipelines, plastic pipes are increasingly used. They are able to withstand high pressures and temperatures, do not rust and have a long service life. For reliable connections among themselves the elements of such a water supply, sets for welding plastic pipes are used, which ensure the speed and quality of the docking procedure without the use of additional parts and tools.
Content
Features of plastic pipes
Plastic pipes are widely used in hot or cold water supply, sewage systems. Compared to products made from other materials, such pipes have several advantages. They exhibit good resistance to rupture during sharp pressure surges in the system, have low thermal conductivity and high throughput. Light weight allows for quick and easy installation, and corrosion resistance provides a long service life.
Important! The not very high value of the maximum working temperature (usually 95 °), significant thermal expansion and the possibility of destruction under the influence of ultraviolet rays impose restrictions on the use of plastic pipes.
Plastic pipes are represented by products made of polyvinyl chloride (PVC), polyethylene and polypropylene. PVC pipes are not recommended for installation of a hot water supply system, since the polymer can produce harmful and dangerous substances under the influence of heat. Such pipes are connected by fittings, glue or cold welding.
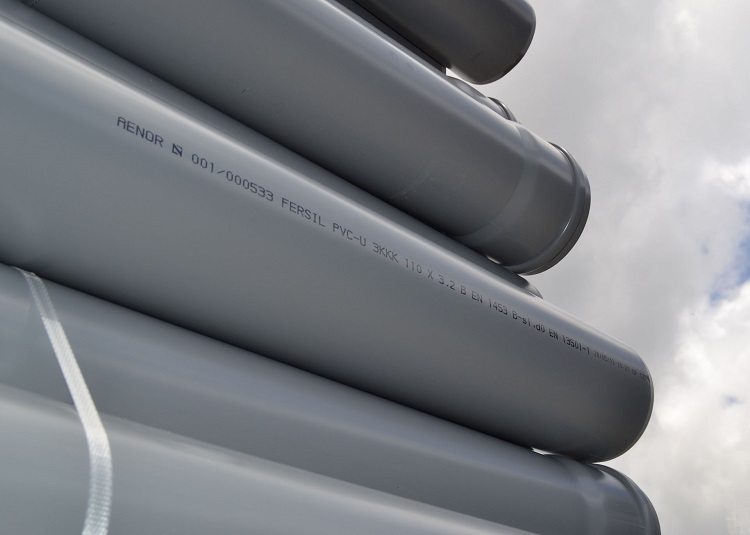
Plastic pipes are made from different raw materials, therefore they have different properties and characteristics
The thermoplastic welding method using fittings is acceptable for polypropylene pipes. Polyethylene pipes come in three types:
- HDPE pipes;
- LDPE pipes;
- PEX pipes.
They are connected using crimp fittings and welding.
The main types of welding
There are three main ways plastic pipe welding joint:
- butt;
- bell-shaped (sleeve);
- electrofusion.
The pipe joining machine can be manual, mechanically or hydraulically driven. Different types of equipment and tools are used for different types of welding and diameters of plastic pipes.
A machine with a mechanical or hydraulic drive is suitable for butt welding of pipes with fittings, with a pipe made of polypropylene, polyethylene. A hand-held device for socket connection is suitable for pipe diameters from 16 to 110 mm made of polyethylene and polypropylene.
In the case of socket welding, a coupling or tee is used. The end of the pipe and the end of the connecting part are heated. Then the pipe is inserted into the coupling or tee to the marked depth.
A hydraulic welding machine is used to butt plastic pipes with a diameter of 63-800 mm, mechanical - with a diameter of 50-250 mm.The mechanical machine is designed for frequent use. It consists of a support frame with an instrument unit and a hydraulic unit. On both sides there are grips between which the liners are installed. The heating element is a disc.
Tools required for joining pipes by welding
Before you start welding plastic pipes, you need to prepare the necessary materials and devices:
- the required number of plastic pipes;
- fitting;
- device for welding pipes;
- special scissors for trimming;
- timer (stopwatch);
- gasoline or alcohol;
- marker or pencil.
For work, it is necessary to determine the size and diameter of the plastic pipes.
It is better to provide a small supply and buy more pipes than required. Fittings are used to dock products. They are purchased in accordance with the terms of the project. Gasoline or alcohol is required to degrease the surface of the pipes.
Important! During welding, the heating process and subsequent solidification of the pipes is controlled by a timer or stopwatch.
Cutting products can be done with a conventional hacksaw for metal, but it is better to use special scissors to cut plastic pipes. Welding is carried out with a soldering iron for plastic. The set includes various nozzles having a Teflon coating. Due to this surface, the pipe material does not stick to them.
Features of welding machines
The device for welding plastic pipes includes a heating element and a dielectric handle. The housing is equipped with several slots that serve to attach interchangeable nozzles. The cost of the soldering iron and its performance is higher, the more it has slots.
A device with more power runs faster. Speed determines the number of parts that can be joined in a given time. If welding work is one-time in nature, then buying a device is irrational, since the car is expensive. In this case, it is better to rent a soldering iron. The temperature of welding pipes made of plastic lies in the range of 250-280 degrees and is set by the regulator.
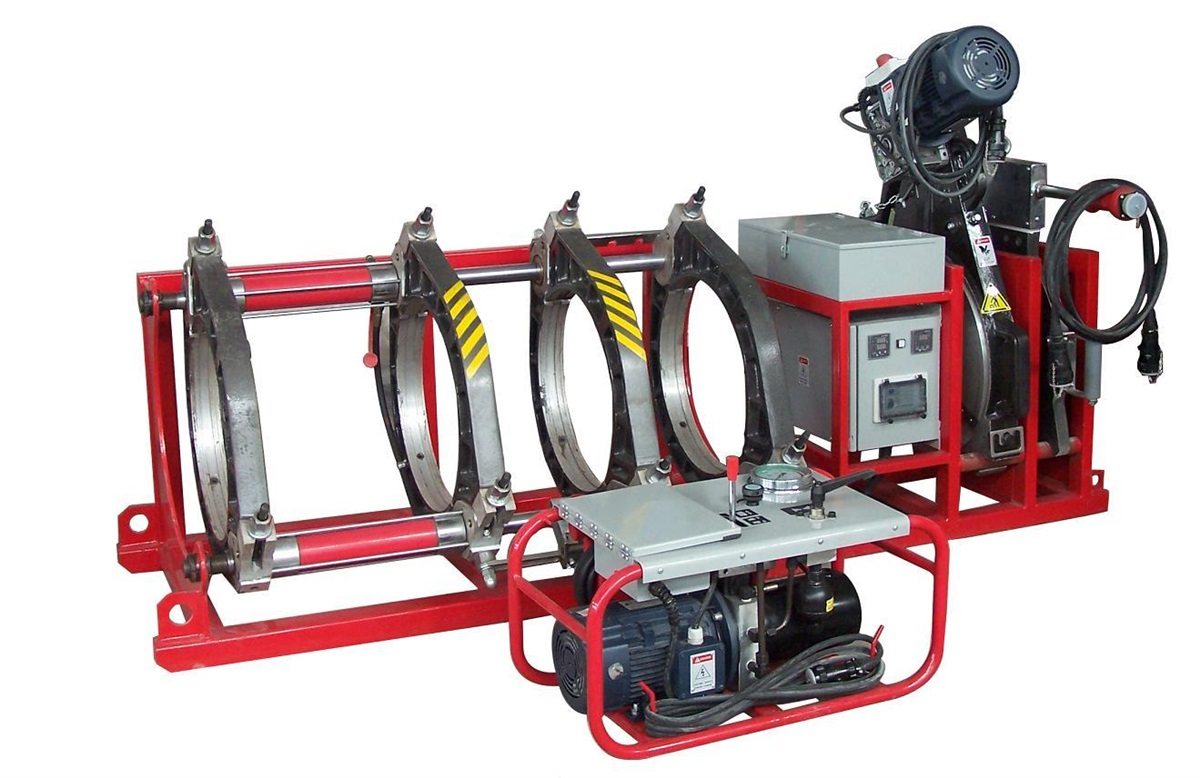
A hydraulic welding machine is more expensive than a mechanical one, therefore it is often used for professional purposes
The mechanical machine is distinguished by its design. Due to its small size and weight, it can be used in confined spaces.
A pipe welding machine is available for professional and occasional use. The set of professional devices, in addition to the necessary nozzles, includes a tool for cutting and preparing the ends of plastic pipes, measuring devices and devices, stands, mittens, cases.
Butt welding equipment and pipes
The welding machine for plastic pipes has a specific set of components. On the frame is a centralizer having one or two fixed clamps for the pipe and the same number of movable clamps. The movement of the clamps is carried out by the oil pressure in the system, which is produced by a hydraulic unit or a mechanical drive handle. Alignment and cleaning of the ends of the pipes to be welded occurs with the help of a miter, which can be mechanical or electric.
The kit also includes a welding mirror, which is needed to heat the ends of the pipes. As a rule, a mirror and a trimming tool are located on the frame, and are stored on a special stand. To fix plastic pipes of various diameters, replaceable liners are used.
Parts of pipes to be welded must be fixed in the centralizer. Usually one of them is fixed rigidly, and the second has the possibility of axial movement.
Helpful advice! The use of roller stops eliminates the friction on the ground of the movable pipe.
In addition to coaxial fastening, the clamp allows you to move the movable pipe towards the stationary one with the control of the force that is created mechanically or hydraulically.
Butt welding
The use of teflon facilitates the removal of heated tools from the welding zones. After fastening the plastic pipes, the ends must be aligned with the crosscut. Parts that are welded must be well pressed to the surfaces of the miter and machined until a flat plane is reached. The depth of the cutter knife pass in one pass should not be more than 0.2 mm. Thus, a snug fit of the ends of the pipes to the heated tool is ensured, as well as the oxide layer is removed and all kinds of contaminants are removed.
Visually, the end of the miter can be determined by the appearance of ring chips on both sides of the miter. Without stopping it, it is necessary to weaken the clamping force and withdraw the movable pipe. This ensures smoothness and lack of scoring.
Then, with a clean tool, chips are removed from the welding zone and from the inside of the pipe. Do not touch the surfaces to be welded with your hands.
After cleaning the pipes are reduced and the tightness of the surfaces that are to be welded is checked. The mismatch of the walls of the pipes should not exceed 10% of the thickness of the pipe.
Table 1
Outer diameter of the pipe, cm | The gap between the ends of the pipes, mm |
≤ 35,5 | 0,5 |
40-63 | 1,0 |
63-80 | 1,3 |
80-100 | 1,5 |
Some centralizer designs minimize misalignment with special alignment adjustments.
Butt welding
Plastic pipe welding must be carried out in ventilated rooms in compliance with safety regulations. While pressing the ends of the pipes to the welding mirror, some efforts must be made to achieve uniform heating. For different pipes, the clamping force is not the same. It depends on the material of the pipes, their wall thickness and diameter.
Under pressure along the perimeter of the end face, molten material acts - grat. It causes a thickening of the wall of the plastic pipe at the seam. The thicker the pipe wall, the greater the necessary height of the burr. After heating, it is necessary to quickly remove the welding mirror and combine the joined surfaces. The welding tables indicate the maximum time for which these operations are necessary. If the value is exceeded, this will affect the quality of the seam.
Note! After contact of the parts to be welded, the pressure of the clamp must be slowly increased to the cooling pressure.
The final formation of the seam occurs after cooling at room temperature.
Procedure for performing socket welding
Before you start laying plastic pipes, preliminary calculations are made. Pipes are cut and laid out in the order in which they will be located in the finished version. The ends must be degreased, as well as grinding from burrs. The pipe is marked with a length that matches the depth of the fittings. This will facilitate further docking work.
After heating the nozzle, a fitting is put on it having thicker walls, and then a pipe segment. Further, the material is heated, the time of which depends on the diameter of the fittings and pipes.
table 2
Pipe diameter mm | Warming up time, sec |
20 | 5-6 |
40 | 12 |
90 | 40 |
Docking machine for welding large diameter plastic pipes takes longer. After warming up, the pipe segment and fitting are removed from the nozzle and the pipe smoothly winds into it. This operation is not allowed with great physical effort or too fast. If the pipe is not included in the fitting, then the conditions for its heating are not met.
Important! It is not recommended to insert the pipe into the fitting until it stops. This can lead to its deformation and a decrease in the inner diameter.
The joined parts are fixed and left to harden. For pipes of small diameter, it usually takes 20-25 seconds. Larger pipes harden longer. A collar is formed at the junction of the fitting and the pipe, the appearance of which indicates the correctness of the welding. The connection is suitable for use after hardening.
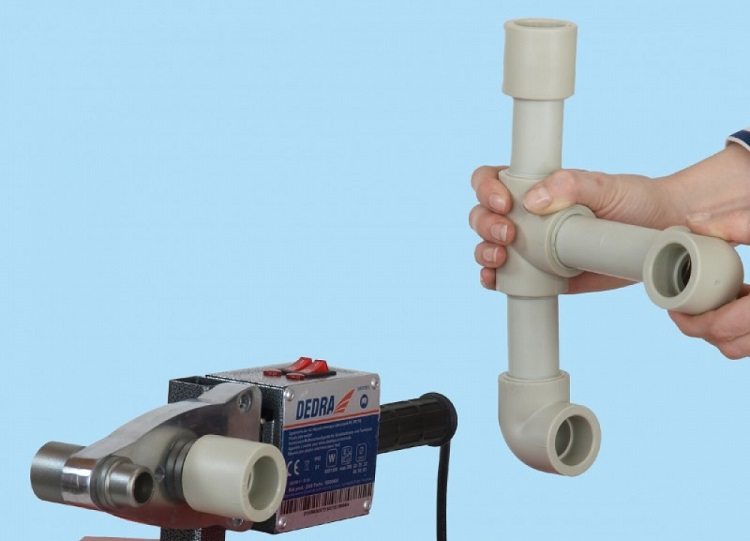
After the heated pipe is inserted into the fitting, it is necessary to withstand for some time to solidify the seam
Features of socket welding
After connecting the device for welding plastic pipes to a power source, heating of the device begins, the speed of which depends on its power. For example, it takes a quarter of an hour to heat a 1.5 kW soldering iron to a temperature of 260 degrees.
The machine may have a light that lights up when the heating element reaches the desired temperature. Heat transfer is more intense in the case of heating the surface of the tool than when welding with heated air, which ensures uniformity of the thermal effect.
When connecting the fitting and pipe, the rotation of the parts to be connected is prohibited. An unheated fitting should have a slightly smaller diameter than the outside diameter of the pipe. It is possible to use pipes with different sizes and brands of polyethylene. Socket welding is more expensive than butt welding. In some cases, the method of coupling welding, you can make the transition to a pipe having a metal thread.
Welding is the most durable and reliable form of joining parts. The effectiveness of the docking operation depends on the quality of the purchased apparatus for welding plastic pipes.