Couplings in general are one of the varieties of fittings. They are designed to connect pipes to each other, as well as connect other elements of the pipeline infrastructure to them. The use of these products guarantees reliable fastening of joints and their tightness. Couplings for low-pressure polyethylene pipes are used in housing and communal services, construction, oil and gas, chemical and other sectors of modern industry.
Content
Principle of operation and properties of electric-welded fittings for polyethylene pipes
The design of such products includes electric heating elements - conductors with high resistance. And as raw materials for the manufacture of electric-welded couplings, low-pressure polyethylene (HDPE) is used.
When an electric current of a given value flows through a conductor, the electrical energy is converted into heat, due to which the plastic is heated to its melting point. As a result, the materials of the parts to be joined are mixed, and when cooled, they are welded.
On the outside of the couplings of electric-welded PND are two terminals. The electrodes of the welding machine, the function of which is performed by the transformer-rectifier, are connected to them. This device is tuned to the calculated voltage and current strength necessary to perform welding of the main parts.
Electrical fittings are used for the installation of such pipelines:
- domestic and industrial water supply, sewerage:
- highways on which it is supposed to transport chemicals that do not violate the structure of IPA;
gas pipelines.
Electric welded fittings have the following physical characteristics and properties:
- allow connecting pipes with an external diameter of 20 ≤ Din. ≤ 400 mm;
- the pressure of the working medium in the pipeline can fluctuate in the range of 6.3-16 atmospheres. Due to this property, an electrically welded PND coupling is recommended for connecting the most critical sections of the main;
- used for pipelines SDR 17 and SDR 11 pressure type, through which drinking water is supplied. The temperature range regulated by the requirements of GOST 18599-2001 is: 0 ≤ T ≤ 40 ≤С;
- an electric-welded coupling is used when laying a pressure head external sewage system, especially where it is necessary to create turns, as well as in places of changing pipe diameters, branches and connections of fittings and shaped elements;
- the welded joint remains very resistant to hydraulic expansion and shock over time.
Helpful information! Published data according to which HDPE pipes with electrofusion coupling are able to withstand freezing and thawing of liquids. The expansion coefficient of ice is about 11%.
The margin of safety and elasticity of polyethylene is very significant, therefore these pipes are used so widely.
Advantages and disadvantages of electric-welded fittings for HDPE pipes
The advantages of these products include their following characteristics:
- The use of electrowelded couplings provides ease of installation of the pipeline structure.
- Long service life - about 50 years.
- Affordable price allows the use of these products to a wide range of consumers.
- Convenience of installation. It is possible to work with electric-welded couplings for polyethylene pipes in a limited space, as well as in inaccessible places.
- Universality. Use these elements is allowed to connect HDPE pipes with any parameters.
- Speed of assembly.
Any type of pipeline made using such connections is characterized by high reliability.
Although the disadvantages of electric-welded couplings are much smaller, nevertheless, they should be taken into account when installing the system:
- the compound does not tolerate being in an alkaline and strongly acidic environment;
- electrofusion fittings cannot be used when pipeline installation hot water and heating. As mentioned above, such compounds are designed for temperatures up to 40 ° C;
- high price. This drawback is not so critical if we take into account the price of welding equipment, with the help of which fittings of other structures are installed, the need to attract a highly qualified specialist and the subsequent payment for his work.
In addition to the usual repair and connection of communications, electric-welded couplings are ideally suited for connecting pipes not only with different diameters, but also made of various materials. The most common transition is from the metal segment of the pipeline to the polyethylene.
Stages of electrofusion welding
Despite its simplicity, this method HDPE pipe connections requires accuracy and sufficient attention. It involves the following actions:
- cut the pipe that you will mount into the system so that the cut plane is strictly perpendicular to its axis;
- the ends of the connected products on the length of their entrance to the fitting, clean well with a special tool. Having done this, thoroughly degrease the treated surfaces;
- fix the parts to be welded in a special mount. It is very important that the distance between the edges of the PND pipes in the middle of the coupling does not exceed the thickness of their walls;
- Connect the terminals of the rectifier transformer to the contacts of the electrofusion fitting. After the information is read from the barcode (it is present on all connectors of this type), the welding process itself will begin. Moreover, it will be executed in automatic mode. The data received from the barcode will be taken as the initial data.
After welding, check the joints for leaks. This must be done before putting the working fluid into the pipes.
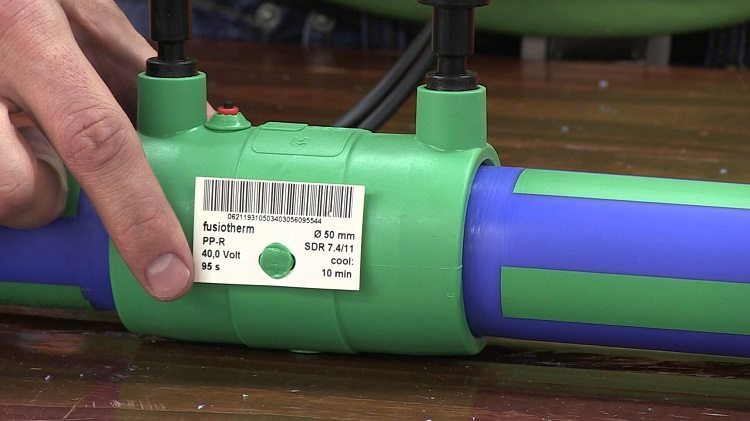
The device determines the heating temperature and duration of welding automatically by reading the barcode data.
To do this, you can use the following simple method: wash the joints and feed a stream of air under pressure, for example, by inserting the hose of the vacuum cleaner into the “blow” hole. The absence of bubbles will confirm the fact that the joint is tight.
Important! A similar sequence of actions is performed twice. This is due to the fact that the welded installation involves fixing the pipeline at the inlet and, at the same time, at the outlet of the fitting.
Technical characteristics of electric-welded couplings for polyethylene pipes. How to choose
To make the right choice of these products, it is necessary to take into account the features of the connected objects - the polyethylene pipes themselves. Like any others, they have a marking system that includes sequences of characters SDR and PE, followed by certain numbers.
SDR is the ratio of the outside diameter of the pipe to the wall thickness. That is, with a decrease in SDR, the wall thickness increases, and with its increase, on the contrary, the wall becomes thinner. After the characters “PE” (polyethylene), the mark of this material is indicated.
Today PND pipes PE100SDR17 are most in demand. They are characterized by uniquely high strength, so these products are very reliable during operation. But even if they did not fail, often homeowners have to change the configuration of the pipeline (for example, to bring water into the premises of a newly built summer kitchen).
In order not to spoil the overall picture of reliability, it is recommended to connect PE100SDR17 pipes using couplings, the design of which includes an electric heating element. The table below shows the technical characteristics of such electric fittings. The unit of measurement of geometric dimensions is millimeters.
Table 1
L - coupling length | L1 - length of the coupling section for the connected pipe | H - coupling height, taking into account the dimensions of the pin contacts | Weight, kilograms | D - inner diameter |
340 | 169 | 465 | 13,300 | 400 |
319 | 158 | 415 | 9,200 | 355 |
266 | 133 | 387 | 8,746 | 315 |
283 | 138 | 320 | 5,860 | 280 |
219 | 109 | 312 | 4,438 | 250 |
218 | 109 | 285 | 3,592 | 225 |
211 | 106 | 260 | 3,307 | 200 |
205 | 102 | 229 | 2,398 | 180 |
186 | 92 | 209 | 1,811 | 160 |
194 | 96 | 182 | 1,076 | 140 |
157 | 77 | 168 | 0,882 | 125 |
161 | 79 | 152 | 0,716 | 110 |
127 | 63 | 131 | 0,388 | 90 |
125 | 62 | 115 | 0,305 | 75 |
107 | 53 | 101 | 0, 169 | 63 |
99 | 48 | 87 | 0,132 | 50 |
89 | 43 | 71 | 0,080 | 40 |
81 | 40 | 62 | 0,051 | 32 |
81 | 40 | 53 | 0,032 | 25 |
83 | 40 | 52 | 0,027 | 20 |
A large number of models are presented in the segment of electric-welded couplings of the modern market. Often there are products manufactured by companies from Germany, Holland, Italy and Russia. When choosing them, you must follow the advice of specialists and take into account consumer reviews. Preference is given to products of well-known brands such as, for example, Chiorino (Italy), Optibelt (Germany), Nupigeco (Italy), Ammeraal Beltech (Holland).
Helpful information. Products of these manufacturers are of high quality, primarily because recycling is practically not used for their manufacture.
If you plan to upgrade an existing pipeline or lay a new one from polyethylene components, the best solution for connecting its branches would be to use electric-welded fittings for HDPE pipes.