When carrying out work related to the laying or repair / maintenance of the pipeline at industrial facilities or in private households, quite often the problem arises of how to measure the diameter of the pipe. It is not always possible to consider the marking, there are situations when the ends of the objects are not available for visual observation and measurement. Provided that special accuracy is not required, measurements can be made using improvised material.
Content
How to determine pipe dimensions by factory control methods and in production conditions
In a pipe mill factory, dimensions are determined using a caliper, a construction tape measure and the formula D = L: π - 2∆ -0.2 mm. To perform the calculations, the following notation and quantities are used:
- D is the value of the outer diameter;
- L is the length of the product measured by tape measure;
- π - taken as 3, 14;
- ∆ is the tolerance allocated to the value attributable to the thickness of the panel used when measuring the device;
- 0.2 mm - empirically obtained allowance value related to the fit of the measuring device to the wall of the measured product.
To measure the length of pipes in factories resort to the use of measuring wire or tape measure. Dimensions may have permissible deviations, according to the declared length of pipes passing through accuracy classes:
- on the first - 15 mm in any direction;
- on the second - 100 mm in any direction.
The maximum deviation that the pipe may have in terms of outer diameter depends on the size of the cross section:
- up to 200 mm - rolled products may have a deviation of 1.5 mm in any direction;
- for larger products, measurements are carried out using an ultrasonic device and the value of the permissible deviation is determined in percent.
The wall thickness of the products under industrial conditions is measured using a caliper with a scale step of 0.01 mm. In this case, the value of minus tolerance should not go beyond the five percent indicator of the nominal value.
Pipe dimensions in the factory take into account the possibility of deviations:
- curvature
- ovality of the ends. Actually, the ovality of the pipes in the factory is determined using a caliper applied in mutually perpendicular planes, or measuring the diameter of the end using an indicator bracket.
On the surface of the tested products, 500 mm from the end face, a factory marking is applied that contains sufficiently informative data, including with respect to nominal sizes.
The delivered batch of products is accompanied by a product certificate containing information about:
- nominal sizes;
- number and date of technical specifications;
- material grade;
- party number;
- results of mechanical and hydraulic tests;
- results of x-ray flaw detection;
- type of heat treatment;
- chemical analysis of smelting.
How to determine pipe diameter in metric and in inches
The calculation of the required pipe sizes is sometimes difficult due to the fact that some data are given in accordance with the requirements of the metric system, and others in inches (this applies to steel products and imported products).
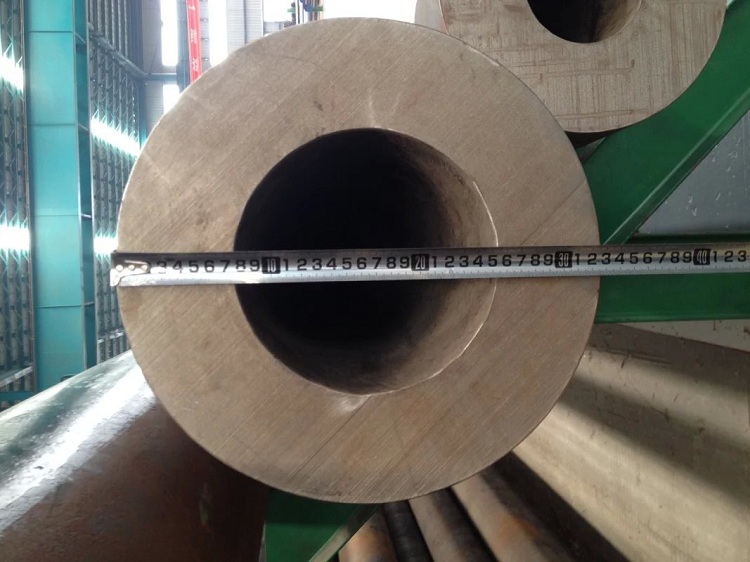
The diameter can be measured in centimeters or inches, but you should be careful when converting from one unit of measurement to another
The pipe size in such cases is calculated taking into account certain features inherent in such products. In particular, for rolled steel, designated as inch, the outer diameter is 33.5 mm, and the inner diameter differs depending on whether we are dealing with an ordinary pipe (27.1 mm) or reinforced (25.5 mm). which almost exactly corresponds to one inch. These characteristics of steel products should be taken into account when replacing with analogues made of other materials. When working with pipelines, you should rely on the size of the conditional passage.
Another nuance is associated with threaded connections, where it is customary to use a special system for pipe threads cut to an outer diameter that differs from metric threads.
Important! The designation given for metric thread matches the size of the outer diameter. The designation for pipe thread with the prefix “pipes”, for example, ½’’ pipe, will correspond to 20.955 mm.
Products of foreign origin are usually marked in inches. Converting from inches to metric is simple: 1 inch = 2.54 mm. Reverse translation is a bit more complicated. How to know the diameter of the pipe in inches? To obtain the product diameter in inches, the available value, measured in the metric system, should be multiplied by 0.398.
How to measure a pipe using materials at hand, even when inaccessible for measurement
Practitioners suggest how to calculate all the necessary structural parameters, dealing, for example, with a chimney, and using the tools available at home.
It is easiest to make the necessary measurements when there is the possibility of visual inspection and direct access to the ends of the pipes, and the accuracy in the calculations is not too significant. Then just use a ruler or construction tape. The measuring device is attached to the widest part of the end face of the measured product. The error of the measurements will be within a few millimeters. If such an error in the measurements is recognized as unacceptably significant, then you will have to resort to the use of more accurate measuring instruments, for example, a caliper.
When determining the outer diameter of the accessible pipe, if it does not exceed 150 mm, it is preferable to use a vernier caliper attached to the end face and legs tightly pressed to the outer walls of the product. The pipe dimensions will be determined to the nearest tenth of a millimeter.
To determine the internal diameter, a caliper or a standard ruler can be used to measure the thickness of the wall of the structure. Its double value is subtracted from the value of the outer diameter. A caliper is also useful if you need to measure an already mounted product, the end of which is not available, but you can attach the measuring device to the side surface. A prerequisite for obtaining an accurate result is the length of the caliper legs must exceed half the value of the pipe diameter.
In order to independently measure large diameter products, you will need to use a cord or construction tape, or a tailor's centimeter. After measuring the circle, the resulting value will need to be divided by the number π.
The difficulties associated with how to calculate the size of the pipe, which is difficult to get to for measuring, are overcome with just two items:
- the camera, which is present in most models of mobile phones;
- a small object, the dimensions of which are precisely known, or a ruler.
A ruler (or an object of known size) is applied to the measurement object. A pipe section and an object attached to it to get an idea of the scale are photographed. To carry out subsequent calculations, work with the image in the photograph is performed. After measuring the visual width in the photograph in millimeters, a translation is made taking into account the scale of the image to obtain values for real sizes.
Note! Measurements and calculations of pipe sizes using materials found at hand can be carried out with a fairly high degree of accuracy, which is quite suitable for work at the household level.
The measurement of the diameter of the pipe is very essential for subsequent operations with the product, which are performed during the preparation of the wiring, installation, docking with other pipes (including those made of other material), the use of fittings. When passing the factory control, exact diameter values are set with insignificant permissible deviations. If it is impossible to use these data, it is completely acceptable to take measurements on your own, while achieving accuracy that allows you to neglect errors as insignificant.