Carrying out electrical work almost always involves the installation of appropriate wiring. Laying the cable with its subsequent fixation allows you to organize the connection of lighting, household appliances and various equipment in the house or at the industrial enterprise. However, the use of additional means of protecting the wiring from various kinds of damage is often required. Among them - corrugated metal pipes.
Content
The principle of operation of the protective product
One of the main characteristics of all tubular products is resistance to external mechanical loads of any origin. These, in the first place, are the weight of the soil. If we compare a corrugated and smooth-walled metal pipe, it becomes obvious that with an equal conditional pass, the surface area of the first is much larger. And from a high school physics course it’s known that
P = F / S,
where P is the pressure, F is the force acting perpendicular to the plane, S is the surface area.
An analysis of this formula shows that the larger the surface area, the lower the pressure per square centimeter of corrugated metal pipe. This factor provides significant bearing capacity of this product.
Helpful information! The walls of the pipes transmit part of the vertical load to the surrounding soil. Therefore, the paramount role is played by how well the soil or concrete mix adheres to the surface of the corrugated pipe over the entire section.
If voids are left when laying these products on the sides, the probability of deformation of these structural elements is non-zero.
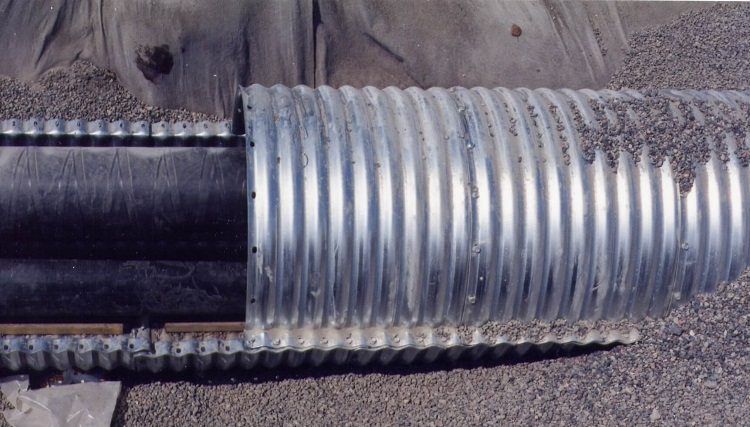
The strength of corrugated pipes is higher than that of smooth pipes, so they are used for underground pipelines
Features and types
A metal corrugation pipe has a feature due to the technology of its production. The manufacturing process of this material is carried out by molding the surface under pressure of rollers of various diameters and configurations. Segments with a smaller diameter are characterized by a smaller metal thickness. Such a constructive solution gives the pipe a certain flexibility, thanks to which it is not required to use fitting for bending the line in case of obstacles in the way of laying the pipeline.
On sale you can find metal corrugation for electrical wiring of the following types:
- light flexible hoses characterized by a low level of mechanical stability. Their installation is allowed only on top of stretch ceilings and under plasterboard structures, that is, in those places where high pressure will not act on the electrical wiring cable. The reason for this requirement lies in the fact that this device does not withstand heavy and sharp loads, so the electric communication line cannot be considered absolutely protected;
- heavy products of medium strength. Such a spiral-shaped corrugated metal pipe can be used for laying cables in concrete, earth and plaster;
- extra heavy corrugations. Pipes of this type withstand increased loads.It is recommended to use them in places requiring special attention to safety. These include healthcare institutions, education, as well as other organizations, including public ones, with high attendance.
Where are metal corrugated tubes used?
The release of these products was first mastered in Russia. It happened back in 1875 at a metal plant in St. Petersburg. Then, by 1896, their production was established in the United States. And only then metal corrugated pipes appeared in Japan, Korea and on the African continent. In the USSR, serious attention was paid to their manufacture. The older generation remembers the "construction of the century" - the Trans-Siberian Railway BAM and so on. The important role of corrugated metal culverts in this matter is undeniable.
In general, such products present on the modern market differ in diameter and cross-sectional shape. Actually, these parameters determine the scope of their application.
Important! When purchasing a corrugated metal pipe for electrical wiring, remember that in the catalog, as a rule, the outer diameter is indicated. From the inner diameter, it differs upwards by several millimeters.
Corrugated tubular products are available with the following sections:
- round. This section is characteristic of a corrugated metal pipe used to create a culvert structure with a height of 1.5-7 meters. The same section, but only smaller, has a corrugated pipe to protect the wiring;
- square. Corrugated pipes with this section are used to create culverts and in the construction of tunnels (3-8 meters);
- pear-shaped. Tunnels, culverts (1.5-8 meters);
- arch. For small bridges, car and railway tunnels (height from 2 to 13 meters). Corrugations of this type can be installed in existing embankments by puncture;
- pipe arch. Tunnels under roads and railways (height from 2 to 13 meters);
- vertical ellipse. This section is suitable for telecommunication type tunnels, created on the basis of corrugated metal culverts;
- transition. With their use, pedestrian crossings are built (1.8–9 meters high);
- horizontal ellipse. This section is inherent in a metal corrugated culvert;
- arch with high or low profile. Small bridges, railway and automobile tunnels (height 6-15 meters).
Manufacture and benefits
The strength of a metal corrugated pipe for electrical wiring is due to a variable cross section. Assembly is carried out from standard elements in the factory. Corrugated metal sheets are used for this. Their connection with honey is carried out by flat-concave and flat-convex washers using bolts. The size of all these elements is determined by the dimensions of the structure. Hot dip galvanizing provides high corrosion resistance. For bordering, a metal corner is used. In the process of manufacturing the design, a grade of steel is used, which is optimally suited to the expected operating conditions:
- 15SP - from minus 40˚С and higher;
- 09Г2Д - at minus 40˚С and lower.
The production of stainless steel corrugated pipe has its own characteristics. For the first time, such material was used for this purpose in the early 80s of the last century in Japan. In the manufacturing process, a steel tape 0.25-0.3 mm thick is used. The pipe is formed from tape by argon welding on an automatic line. Reliability control of the weld is carried out using a laser system. Its width should not exceed the wall thickness more than 1.6 times. The formation of the corrugation is the final stage of production of products of this type.
Helpful information! Before sending to the finished goods warehouse, corrugated pipes for wiring must be checked for leaks by immersion in a container with ordinary water. Compressed air passed through the product, localizes the defective areas.
In addition to fulfilling the functions of protecting the wiring from negative influences, corrugated metal pipes are widely used in heating and water supply systems.
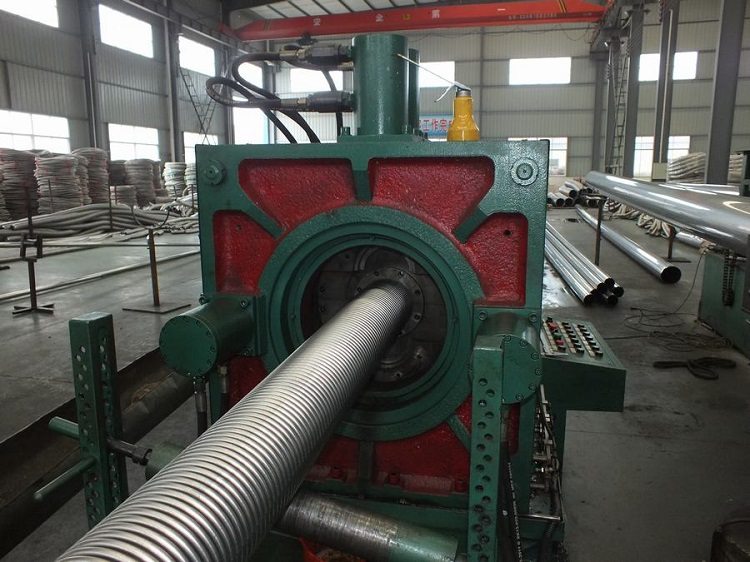
Pipe production includes several stages, the formation of the corrugation is the final part of the process
The advantages of stainless steel products include:
- simplicity of installation and operation;
- increased heat transfer (compared to copper);
- the impossibility of the formation of sediment on the walls;
- high resistance to corrosion;
- possibility of use in the temperature range 0≤ T≤ + 100˚C.
- ability to withstand pressure up to 65 bar (64.15 atmospheres). If welding is carried out at a temperature of the order of + 1150 ° C, the seam is able to withstand 210 atmospheres.
Specifications
As mentioned above, the main parameter of a corrugated pipe for wiring is its diameter. In order not to waste time searching for a suitable variant of a tubular product, you can use the data presented in the table.
Table 1
Conductor cross section, square millimeters | Cable type and voltage | ||||||
4-core up to 1 kV | Three-core voltage, kV | 2-core voltage up to 1 kV | Single core up to 1 kV | ||||
10 | 6 | Until 3 | |||||
800 | ______ | ______ | ______ | ______ | ______ | 1700 | |
625 | ______ | ______ | ______ | ______ | ______ | 1520 | |
500 | ______ | ______ | ______ | ______ | ______ | 1400 | |
400 | ______ | ______ | ______ | ______ | ______ | 1220 | |
300 | ______ | ______ | ______ | ______ | ______ | 1000 | |
240 | ______ | 460 | 510 | 570 | ______ | 880 | |
185 | 450 | 400 | 440 | 490 | ______ | 755 | |
150 | 395 | 355 | 390 | 435 | 500 | 675 | |
120 | 350 | 310 | 340 | 390 | 435 | 595 | |
95 | 310 | 265 | 295 | 340 | 380 | 520 | |
70 | 265 | 215 | 245 | 285 | 325 | 440 | |
50 | 215 | 180 | 200 | 235 | 270 | 360 | |
35 | 175 | 150 | 160 | 190 | 225 | 285 | |
25 | 150 | 120 | 135 | 160 | 185 | 235 | |
16 | 115 | 95 | 105 | 120 | 140 | 175 | |
10 | 85 | ______ | 80 | 95 | 105 | 140 | |
6 | ______ | ______ | ______ | 70 | 80 | ______ |
There are other technical specifications for these products. Of particular note are the following:
- the surface roughness coefficient is 0.008;
- the thermal conductivity of the corrugated stainless pipe is 17 W / m * K;
- the bending radius of the product, depending on its diameter, ranges from 25≤R≤150 mm;
- service life over 30 years.
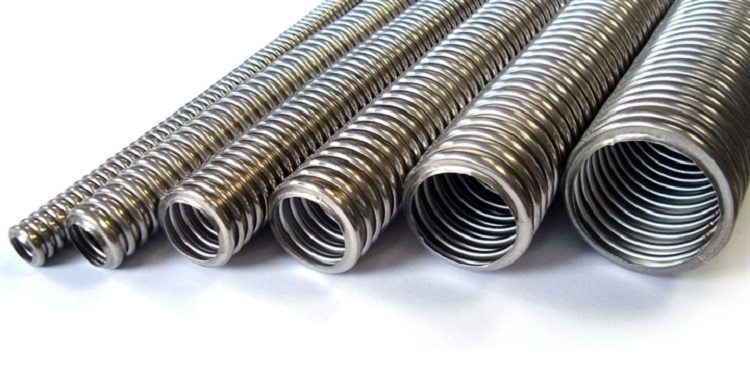
The choice of the diameter of the corrugated pipe depends on the parameters of the cable that will pass through it
Installation of electrical wiring in a corrugated pipe
This procedure involves several steps.
Preparation of materials. First, the necessary piece of metal corrugated pipe for the cable is cut. At the same time, it is very important not to allow the steel cable to go inside the tube product, because it is always slightly taut. If you miss, it will rest against the fold of the pipe. And in order to get the cable, you have to make a cut in another part of it. To avoid such an unpleasant situation, bite the broach, hold it with your fingers, and at the end of this operation, pull it out a little and bend along the pipe.
Preparing the wiring harness consists in fastening the wires or cables with electrical tape at regular intervals.
Helpful advice! It is better to use PVC electrical tape, rather than cotton, because it is very smooth and does not create additional friction when pulling the wiring.
Pay particular attention to the quality of the fastening of the harness to the pull cable. It must be extremely reliable, otherwise in the event of a break, you will have to do the work again. Electricians do this in two ways: a tourniquet is encircled with steel wire, pulled together with pliers. A more effective fastening is a puncture with a cable for pulling the spring insulation of the bundle cables, followed by winding the puncture places with electrical tape. This must be done so that the ends of the wiring cables do not abut while pulling into the bends of the corrugation. The longer the connection between the harness and the pull cable is longer, the more reliable it will be.
Tightening the bundle into a corrugated metal pipe. It’s easier to do this work together. One partner holds the cable tightly, and the second pulls the corrugation on the tourniquet. However, having reliably fixed the broach, you can cope alone. But, one way or another, it will be very difficult to do without strong hands capable of continuously pulling the corrugation with considerable effort. In addition, free space is required to complete this operation.And remember, when working with a tourniquet and corrugation, extreme care must be taken to prevent the broach from breaking.
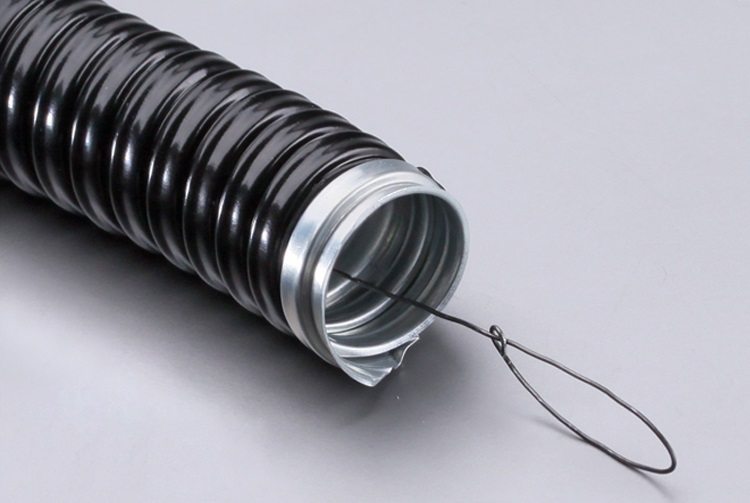
To make the process of pulling the cable inside the corrugation quick and trouble-free, choose sleeves equipped with a probe
Fixing a corrugated metal pipe for electrical wiring. After tightening the tow, the resulting structure should be fixed to the wall or ceiling. As fasteners, you can use a mounting aluminum strip or special clips, which should be selected according to the diameter of the pipe. In trading enterprises they can be bought individually. Position the fasteners at approximately equal intervals. So you will not allow sagging of the corrugation, the weight of which will add a cable harness stretched inside it.
By connecting switches and sockets, as well as introducing harnesses into branch boxes, it is also better to hide the end of the corrugation inside so that there are no bare sections of wiring. To this end, purchase boxes, sockets and switches with rubber seals that are cut to the diameter of the corrugation. This is especially true for outdoor communications.
Selection and installation recommendations
Corrugated spiral-wound metal pipes comply with fire safety requirements from the point of view of laying networks in wooden houses using an open method. Of course, when a corrugated pipe with an electrical wiring cable is laid on a wooden wall, it is necessary to do this using other fire-resistant material, which can be used, for example, asbestos.
Good to know! This approach will prevent fires if a short circuit occurs when the automation system is not working.
And one more very important point: the quality of fastening clips should not be inferior to the quality of corrugated tubes. Select these fixation elements taking into account their ability to withstand the corresponding load. It is also necessary to bear in mind that for sale on the domestic market you can find defective metal corrugation for wiring, not equipped with a steel cable that serves to pull the cable. To avoid problems when purchasing, find out the availability of this accessory.
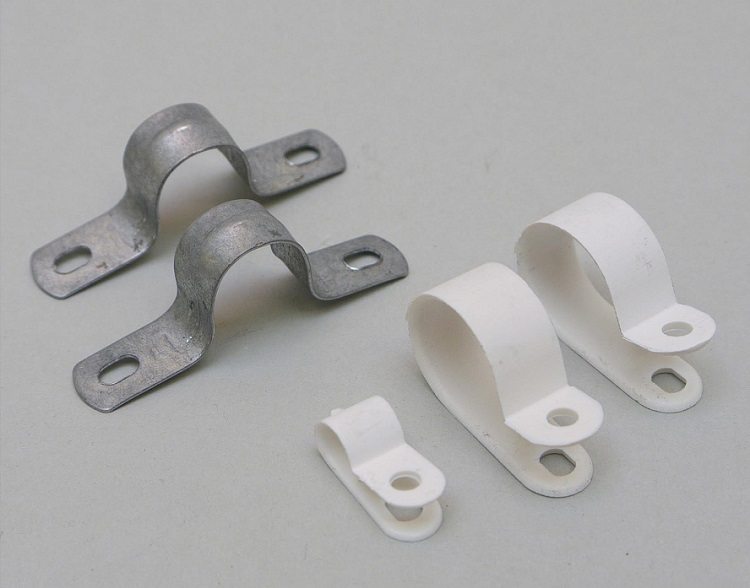
Fasteners must be selected in accordance with the diameter of the corrugated pipe, then it will be reliable
When buying, give preference to products of famous brands. Although its cost is relatively high, it is fully consistent with the quality of the corrugation for wiring. Today, in this segment of the domestic and world market, products of such companies as:
- Legrand (France). In the USSR, the products of this brand first appeared in the not-so-distant 1980;
- IEK Group of Companies (Russia). Its branches are open in the Baltic countries, Mongolia, Kazakhstan, Moldova and Ukraine;
- Frankische (Germany). The demand for and the highest quality of products of this brand is eloquently indicated by the fact that it has been working in this segment of the world market for more than 100 years. Frankische was founded in 1906.
It should be noted that, according to some homeowners, the use of corrugations for wiring from an aesthetic point of view is unacceptable. However, if you lay it evenly and neatly, you will get a normal appearance that will not spoil the interior design of the living room.