Laying the communication cable in rooms or on the ground does not exclude the possibility of damage to it during operation. Widely used as protection pipe made of low pressure polyethylene (HDPE). It is also used in cases of laying power lines. Such pipes reliably protect communications from mechanical damage, stray currents and soil exposure. The choice of installation technology depends on the purpose of the engineering network and its location.
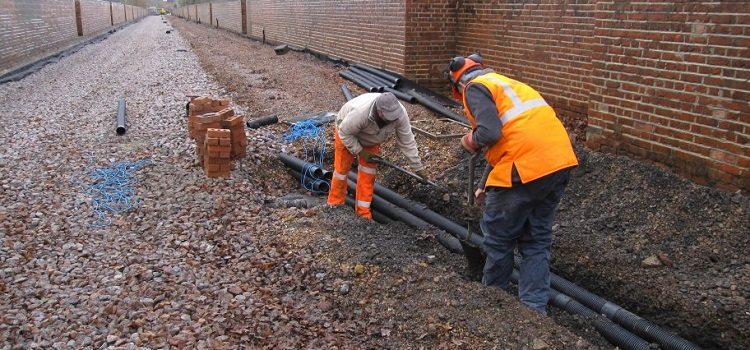
Polyethylene pipes - one of the best means for protecting cables when laying underground electrical networks
Content
- 1 HDPE pipe production
- 2 Features of PND products for laying electric cables in the ground
- 3 Types of protective pipes PND for cables
- 4 Technical parameters of pipes
- 5 Advantages of using HDPE pipes
- 6 Labeling of polyethylene products
- 7 Basics of choosing HDPE pipes
- 8 Subtleties of laying technical pipes
- 9 Cable routing in structures
- 10 Laying cables in HDPE pipes in the ground
- 11 Trenchless cable laying technology in the ground
HDPE pipe production
The main raw materials for the production of protective corrugated piping are Low Density Polyethylene (LDPE) and Medium Density Polyethylene (MDPE). Non-combustible or slow-burning HDPE pipes are made from a mixture of flame retardant and polyethylene.
The basis for obtaining products is the extrusion method. Production is carried out on high-tech equipment with automated quality control. Optimization of the consumption of raw materials, minimizing the amount of rejects and lowering the price is achieved due to constant monitoring and the ability to adjust indicators at any stage of production.
The technical pipeline has a single layer smooth structure. It has all the required characteristics of dielectric and mechanical strength, as well as chemical resistance. Since such pipes are used not only for cable protection purposes, they are delivered without an installed probe.
Product color is usually black. A flexible polyethylene pipe is used to lay electrical wiring inside structures.
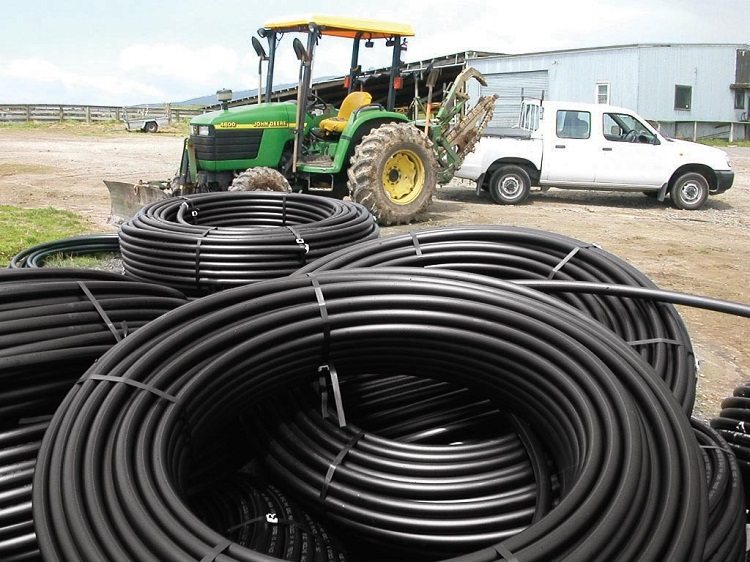
The HDPE flexible pipe has a small diameter and is convenient to use for installing the network indoors
Features of PND products for laying electric cables in the ground
For underground cable laying, these types of HDPE pipes are used:
- light corrugated;
- heavy corrugated;
- halogen free;
- smooth walled rigid;
- double-walled.
Corrugated pipe can be reinforced with steel wire, which gives it additional strength. Double-walled products have a smooth inner shell, which is made from LDPE, and a corrugated shell made of HDPE. This design has a high ring stiffness, allowing the pipe to withstand significant loads.
The smooth inner surface makes cable installation as easy as possible. In addition, double-walled pipes are lightweight, and this facilitates their laying in trenches and transportation.
Note! Installation work can be carried out in a fairly wide temperature range (even in cold weather).
The two-layer corrugated pipe exhibits high resistance to ultraviolet radiation and aggressive substances. No-socket couplings are used for docking. The term of operation is not less than 50 years.
Types of protective pipes PND for cables
Laying power lines or other utilities involves the use of different HDPE pipes. They vary in design features and technical parameters. The division of protective products into electrical products (usually corrugated double-walled pipes) and technical (usually smooth single-walled).
For the installation of electrical wiring in a brick wall or floor screed, a smooth black pipe is used.
Products having a corrugated surface are applicable for laying telephone, television, computer and electrical networks that operate at AC or DC voltage up to 1 kV. There are open, half-hidden and hidden methods of cable management. This type of electrical installation can operate in open air or indoors.
Corrugated HDPE pipes for laying in the ground of the cable are characterized by increased strength and elasticity, ease of installation and the ability to restore their linear dimensions.
The type of product design determines the release of products with a probe (broach) or without a probe. The broach is a special device designed to introduce the cable into the pipe. The presence of the probe accelerates the process of laying communications and power networks.
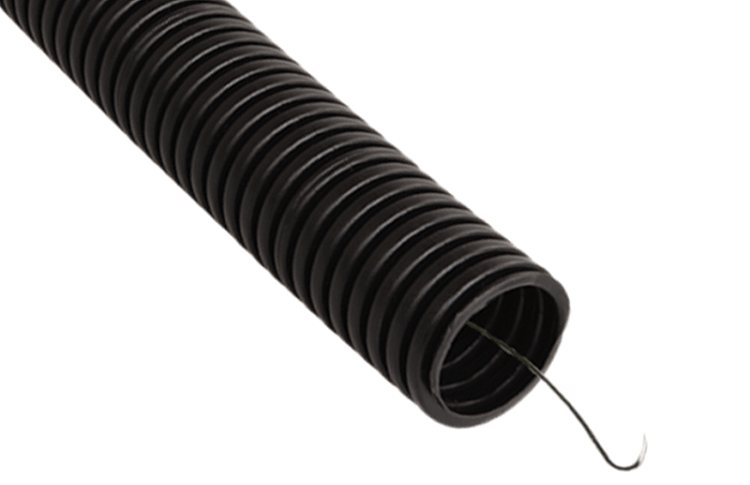
Choosing a product equipped with a probe for cable pulling can greatly facilitate the placement of wires inside the pipe
The broach can also be done using a reusable attachment. However, this process is labor intensive and requires special technical support. HDPE pipe without broaching can be used repeatedly.
Technical parameters of pipes
For any type of pipe, it is mandatory to comply with all technical specifications and requirements that are established in the standards. GOST 16338 defines the manufacture of HDPE markings 286, 277, 276, 273 and 271. GOST 16337 - markings 16803-170, 15803-020, 15303-003, 10803-020.
The product should not have blisters, cracks, or other external damage. Separation of the walls is unacceptable.
Note! The inner surface of the pipes, both rigid and corrugated, should be smooth, and the outer - homogeneous.
The range of technical pipes PND is given in the table.
Table 1
SDR 9 | SDR 11 | SDR 13.6 | SDR 17 | SDR 17.6 | SDR 21 | SDR 26 | |
Outer diameter in mm | Wall thickness in mm | ||||||
16 | 2,0 | ||||||
20 | 2,3 | 2,0 | |||||
25 | 2,8 | 2,3 | 2,0 | ||||
32 | 3,6 | 3 | 2,4 | 2,0 | |||
40 | 4,5 | 3,7 | 3 | 2,4 | 2,0 | ||
50 | 5,6 | 4,6 | 3,7 | 3 | 2,4 | 2 | |
63 | 7,1 | 5,8 | 4,7 | 3,8 | 3,6 | 3 | 2,5 |
75 | 8,4 | 6,8 | 5,6 | 4,5 | 4,3 | 3,6 | 2,9 |
90 | 10,1 | 8,2 | 6,7 | 5,4 | 5,2 | 4,3 | 3,5 |
110 | 12,3 | 10 | 8,1 | 6,6 | 6,3 | 5,3 | 4,2 |
125 | 14 | 11,4 | 9,2 | 7,4 | 7,1 | 6 | 4,8 |
140 | 15,7 | 12,7 | 10,3 | 8,3 | 8,0 | 6,7 | 5,4 |
160 | 17,9 | 14,6 | 11,8 | 9,5 | 9,1 | 7,7 | 6,2 |
180 | 20,1 | 16,4 | 13,3 | 10,7 | 10,2 | 8,6 | 6,9 |
200 | 22,4 | 18,2 | 14,7 | 11,9 | 11,4 | 9,6 | 7,7 |
225 | 25,2 | 20,5 | 16,6 | 13,4 | 12,8 | 10,8 | 8,6 |
250 | 27,9 | 22,7 | 18,4 | 14,8 | 14,2 | 11,9 | 9,6 |
Such products have a high level of wear resistance. They differ in tensile strength at break of 20-38 MPa and a linear expansion coefficient of 140 Pa.
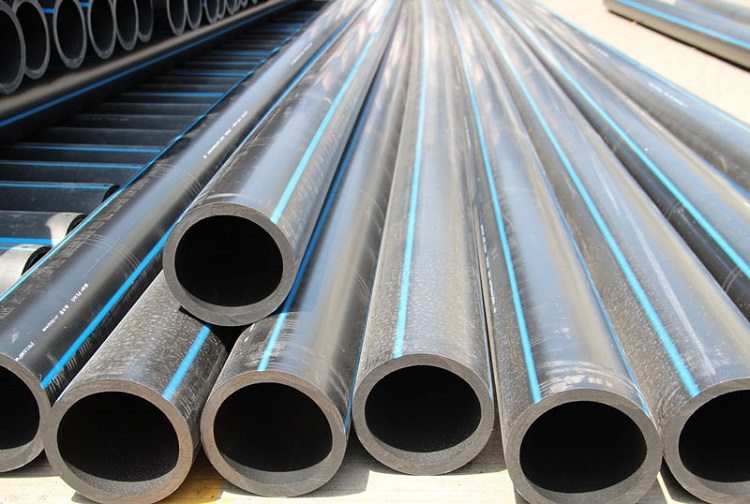
If the electrical network is laid very deep underground, it is better to choose heavy HDPE pipes for this
The nominal pressure of light electrical pipes is 0.25 MPa, medium light - 0.4 MPa, medium - 0.6 MPa, heavy - 1 MPa. Non-standard pipes are produced with the nominal pressure required by the customer.
Advantages of using HDPE pipes
Polyethylene pipes for cable laying are much cheaper than protective structures made of metal. It is also allowed to use products made from recycled materials. HDPE technical pipes are basically waste products mixed with various types of polyethylene additives. This technology in some way changes the existing characteristics, as well as the color of the finished product, however, it allows to reduce costs and cost.
HDPE pipes for laying cables in rooms or on the ground have a long service life of 50 years under normal conditions. The connection of pieces of small diameter products does not require application apparatus for welding. Due to the good electrical insulation properties of HDPE pipes, there is no need for their grounding.
They are much lighter than metal counterparts and are not subject to destruction under the influence of corrosion and aggressive environment.The PND pipe for laying the cable in the ground or in the room can withstand temperature extremes from -25 to +70 ° C while maintaining its parameters. These products also do not accumulate condensation on the surface and do not emit harmful substances.
Since pipes (especially small diameters) are bendable, cable laying in the ground is possible along any path without the use of connecting elements. However, the product cannot be bent too much. If a short circuit occurs, the product prevents burning.
Labeling of polyethylene products
Pipe marking is one of the methods for monitoring the conformity of product quality and its performance to the data given in the documentation. The pipe made of polyethylene must bear the quality mark. It shows that all the requirements of the standards are met. In addition, the trademark or full name of the manufacturer is indicated.
The code and number of the national or international standard by which it is manufactured is applied to the pipe. The following are data on the material of the product. Marking of pipes made of PE 63; PE 80 and PE 100 are carried out as MRS 6.3; 8 and 10.
Note! Mandatory marking parameters are the minimum wall thickness and the size of the outer diameter. The pipe also indicates the nominal pressure, which is expressed in bars. The nominal pressure is such a pressure of the medium that is able to withstand the product at +20 ° C for continuous operation.
The labeling may separately indicate the possibility of using gas pipes and pipes intended for the transfer of drinking water. Separately, the batch number and release date of the product.
According to the standards, the pipe can belong to one of six classes: heavy (T), medium heavy (ST), medium light (OS), medium (C), medium light (SL), light (L).
Basics of choosing HDPE pipes
The choice of corrugated PND pipes depends on the number and size of wires that are used for electrical wiring. The necessary data are given in the table.
table 2
Cable Cross Section (mm2) | Pipe diameter (mm) | Number of wires (pcs.) |
95 and more | 63/63 | 3/2 |
70 | 63/50/63 | 3/2/4 |
50 | 50/50/63/63 | 3/2/5/4 |
35 | 50/40/63/50 | 3/2/5/4 |
25 | 40/32/50/50 | 3/2/5/4 |
16 | 32/32/40/40 | 3/2/5/4 |
10 | 32/25/40/32 | 3/2/5/4 |
6 | 25/20/32/32 | 3/2/5/4 |
4 | 20/20/25/25 | 3/2/5/4 |
2,5 | 16/16/25/20 | 3/2/5/4 |
1,5 | 16/16/20/20 | 3/2/5/4 |
The most popular sizes of corrugated HDPE pipes are summarized in the table.
Table 3
Outer diameter given in mm | Inner diameter given in mm | Bay length (m) |
63 | 50,6 | 15 |
50 | 39,6 | 15 |
40 | 31,2 | 15 |
32 | 24,3 | 25 |
25 | 18,3 | 50 |
20 | 14,1 | 100 |
16 | 10,7 | 100 |
Different manufacturers produce HDPE pipeswhose diameter varies between 16-225 mm (some even 250 mm). The walls of the products are thin, middle and thick. If the cross section of the pipe is small (up to 9 cm), then it is supplied in bays with a total length of 200 or 100 meters. Products with a different cross section are produced in 12 m lengths.
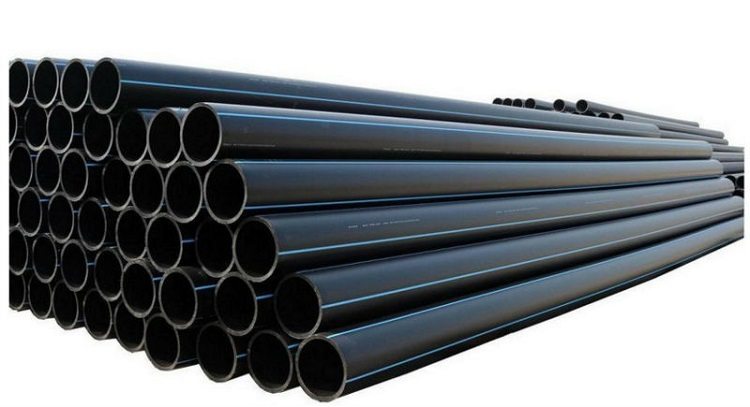
Pipes with a diameter of more than 9 cm are delivered in lengths of 12 m and transport will require transportation
The main criterion for evaluating the geometry of HDPE pipes is the SDR indicator. It is the quotient of the division of the outer diameter and wall thickness. The lower the value of this indicator, the higher the strength parameters of the pipe.
Technical HDPE pipes can be used not only for laying power lines, but also in plumbing, pressureless sewers, as well as for protecting metal pipelines.
Subtleties of laying technical pipes
Depending on the type of pipe, cable laying can be carried out above ground, underground and indoors. In the latter case, the protective structure is placed in concrete, brick or plasterboard walls. Performance of work requires taking into account some nuances, among which there are the following:
- PND pipes are allowed to work at temperatures up to -30 ° C.
- With a channel trench laying, the depth of which is more than 2 meters, it is necessary to provide a protection layer - a concrete channel with a thickness of 80-100 mm.
- Horizontally placed products may be concreted into the foundation structure.
- It is important to ensure the tightness of the connection points during installation.
- If the operation of the pipe involves the possible formation of condensate, then it is mandatory to install a lingering tube to collect it.
The tightness of the connections ensures the cable is protected from moisture, oil, dust and other contaminants inside the pipe. The joints should be tightly sealed.
Note! The most leakproof joint methods are the use of compression couplings and butt welding.
Thanks to the use of HDPE fittings, it is possible to easily create a pipeline having any configuration. During installation, there is no need for a cathodic protection device.
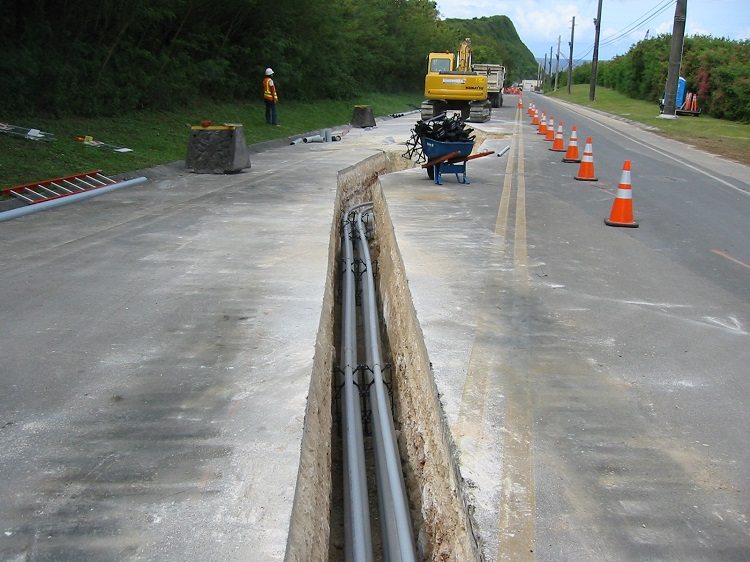
When laying at a shallow depth, pipes do not require additional protection in the form of a concrete channel
Cable routing in structures
Current regulations do not prohibit the use of smooth or corrugated PND products for the installation of concealed wiring. Cable routing in the PND pipes in the room is performed in the following sequence:
- the location of the cable is planned;
- the pipe is fixed;
- cable pulling is in progress;
- the structure on the floor is poured with concrete screed, in the ceiling or wall it is covered with plaster or other materials.
Fastening to the floor can be carried out using metal brackets, and to the walls or ceiling - with special holders with a latch. When pulling the cable, it is necessary to ensure its free location without tension.
Using HDPE pipes allows you to perform repair work, as well as hauling wires without damaging the surfaces of walls and ceilings. In addition, the length of the wiring is significantly reduced.
If communications are mounted indoors, it is possible to use different connecting elements to fix individual sections of the protective pipeline: couplings, bends, etc. However, corrugated products are often used to make the transition from wall to floor or at the points where pipes enter the plate. Since the required bending angle is 90 °, deformation and crushing of a smooth HDPE pipe is possible.
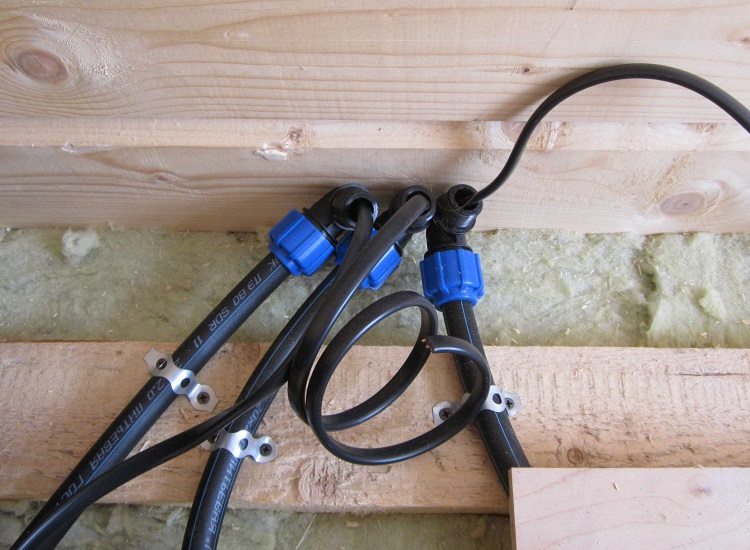
If the walls or ceiling are made of combustible materials, then in such a pipe, only a low-current network can be laid along them.
Laying cables in HDPE pipes in the ground
The technology of laying HDPE pipes in the ground is in demand when conducting communications in a private house or in a summer cottage. Before starting work, it is necessary to inspect the cable for the integrity of its sheath. The process of laying in the ground is as follows:
- marking is carried out and a trench of the required depth is excavated;
- an HDPE pipe (with or without a broach) of a suitable diameter is placed in it;
- the cable is stretched and laid without tension;
- the pipe is filled with a 10-cm layer of sand, and then with soil about 15 cm.
To detect the location of the cable above it, you can lay the signal tape.
Note! Using PND products for laying power lines in the ground, it is advisable to exclude the use of connecting elements and couplings, as this may violate the sealing.
When connecting cables to a building, fittings are required.
On straight sections of cable laying in the ground, it is necessary to use solid sections with a cross section of at least 4 mm. To tighten the wiring into the pipe at large distances, a metal wire or a special broach from kapron is taken.
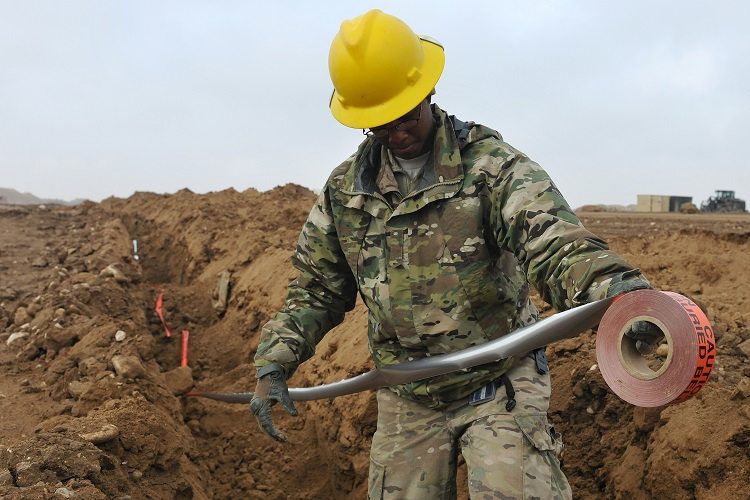
When trenching the cable, a signal tape is laid in the prepared ditch to indicate the electrical network
Trenchless cable laying technology in the ground
The trenchless technology for laying communications in the ground is used when they are located in inaccessible places. It requires the use of special equipment and equipment. At the same time, horizontal drilling is performed in the ground.It allows you to lay communications without much disturbance of the topsoil.
For work, a permit is first obtained and the composition of the soil is studied. Cable laying in the HDPE pipe occurs in stages:
- drilling a pilot well;
- the well is expanding;
- PND pipe is installed with a cable inside.
During the drilling of a pilot well, the soil is punctured with a drill head having built-in radiation and a bevel in its front part. When it passes through the holes in the ground, a solution is supplied that fills the well. It cools the tool and reduces the risk of crashes.
The expansion of the well is carried out by a trimmer replacing the drill head. Pulling HDPE pipes into the well is performed using a drilling rig.
The most significant drawback of this technology is its complexity. For this reason, such work is carried out by specialized organizations with the necessary equipment.
Features laying HDPE pipes depend on the location of the cable, as well as the conditions for its use. Protective products made of low-pressure polyethylene are excellent for underground power lines. High indicators of quality and resistance to external influences determine their increasing popularity in comparison with analogues from other materials.