The tool for the installation of metal-plastic pipes has become widespread in connection with the advent of metal-polymer products. Composite constructions required special equipment for cutting, bending and installation - scissors, cutters, pipe cutters and pipe benders, calibrators and chamfers, crimping pliers. Differences from a similar tool used in working with metal are generated by the characteristics of the material for which they are intended to work.
Content
- 1 Work with composite metal-plastic pipes: tool requirements
- 2 Metal pipe cutting: with a hacksaw or scissors?
- 3 Cutter and pipe cutter for plastic pipes
- 4 Manual bending when installing pipes made of metal
- 5 Pipe bender
- 6 Classification of pipe benders by other parameters
- 7 Installation of plastic pipes
- 8 Repair of plastic pipes
Work with composite metal-plastic pipes: tool requirements
Durable, durable, resistant to aggressive environment metal-plastic pipes are widely used. They are used in plumbing and heating systems, for transporting various chemical compounds and compressed air, for laying electrical cables. Popularity is ensured by the success of the composite design. It consists of five layers:
- made of cross-linked polyethylene, the inner and outer layers are made;
- the center of the structure is occupied by an aluminum shell;
- adhesive joints bind the aluminum core to the outer and inner cross-linked polyethylene coating.
Structural elements of a metal-plastic pipe are called upon to play the following roles:
- aluminum allows you to keep fit;
- polymers protect aluminum from exposure to aggressive media, prevent moisture from entering and prevent the onset and development of the corrosion process.
The lightness of the design puts forward special conditions for the use of a special tool that is accurate in operation and eliminates the use of excessive forces. Otherwise, the elegant design will immediately be damaged and become unusable.
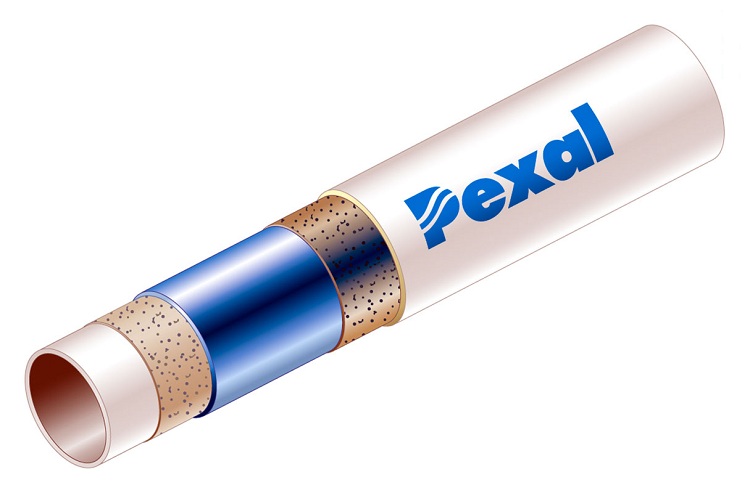
A metal-plastic pipe is a composite product and you need to work with it carefully so as to prevent delamination of its components
Metal pipe cutting: with a hacksaw or scissors?
Plastic pipes are delivered in bays. Before starting work, they need to be measured, to determine how many products and what length will be needed for subsequent installation. Then proceed to cutting segments of the desired length. This can be done with an ordinary hacksaw, but it will leave nicks and burrs, which can lead to a loose fit of the joints. Using a hacksaw is fraught with deformation of the internal section of the product, which will need to be corrected by the calibrator.
At home, it is worth using special scissors for metal plastic. Their design consists of:
- wedge-shaped knife made of hardened or stainless steel;
- a latch that protects against uncontrolled opening of the tool;
- convenient handles to ensure precision cuts;
- auxiliary gear knife rack;
- a button that allows you to return the tool to its original position.
Cutter and pipe cutter for plastic pipes
For products of small and medium diameter, a cutter for metal-plastic pipes is used. This tool, in comparison with scissors, is more suitable for professional use, which does not exclude the use in domestic conditions.
It is equipped with convenient handles and a latch-lock of the closed position. The support and upper brackets allow the installation of the required girth of the pipe and the perpendicular direction of the removable knife. Using a torch for makes the use of a calibrator unnecessary; it is equipped with built-in calibrators. The cutter can not only cut the structure, but also restore its shape on the cut.
For cutting large diameter plastic pipes, it is recommended to use a pipe cutter. The use of a pipe cutter requires attention to a number of details:
- whether it is suitable for cutting products of a given diameter;
- what the tool manufacturer recommends regarding the frequency of knife sharpening;
- what material was used to make the knife.
Manual bending when installing pipes made of metal
Metal-plastic structures often have to be bent during installation. If the bending angle is small and the length is significant, then this operation can be done manually. Nevertheless, it is recommended to break it into several stages, approaches. This is done for the sole purpose of: not allowing haste to result in a change in the cross section of the product or the formation of folds on its concave side, or hopeless deformation. The length of the bend should be seven times the diameter of the pipe.
If there is no special tool at hand, then you can use it for bending:
- metal spring;
- sand;
- blowtorch or building hair dryer.
Using a spring of a suitable diameter avoids deformations when the structure is bent. Sand will not be allowed to deform even if it is covered with sand at one end (as a kind of spring) when the other end is closed. Uniform heating of the metal-plastic construction from all sides with a blowtorch or a building hair dryer can be used in combination with other bending methods or as an independent method. After warming up, the bend is set by a single action of the hands.
At home for plastic pipe bending You can use a spring mechanism. You will need to choose a spring of the desired cross section and length with one extended end, for ease of use. The usage pattern is as follows:
- A steel wire is connected to a spring selected for cross-section and length.
- A pipe bender is inserted into the pipe (or vice versa).
- The spring is positioned so that its center coincides with the center of the planned bend.
- Bending is performed, possibly using an emphasis in the form of one's own knee.
- The spring is removed by pulling the steel wire attached to it.
Pipe bender
The recommendation on how to avoid deformations when bending while working with any metal-plastic pipes is simple: use a special tool. Pipe benders for metal-plastic constructions are divided according to the features of the device into:
- Tame. Designed for bending products with a section of up to 50 mm and an angle not exceeding 180º.
- Electromechanical. Management is carried out by means of predetermined programs; the unit is supplemented with special functions and corresponding structural elements. Home use is naturally unprofitable.
- Hydraulic (stationary and manual). A manual pipe bender equipped with a hydraulic pump can be made in a home workshop. The hydraulic pipe bender (with open frame or closed) is controlled by a linkage. This allows you to establish control over the bending process, which can be interrupted at any time, set the desired bending angle.
Advantages of pipe bender:
- operational safety;
- structural deformations are excluded;
- the possibility of processing pipes of any section.
Classification of pipe benders by other parameters
According to the method of bending pipe benders are:
- crossbow. Allow bending to 90º, carried out around the device. Differ in compactness and low cost;
- spring. Suitable for bending both copper and aluminum structures. Longer spring benders allow you to work with longer sections. Individual models are equipped with the ability to move the spring, which allows them to be applied to individual sections of the pipe, and not to the entire structure as a whole;
- segmented.
The pipe bender can work by:
- rolling technique, when the structure is located between the fixed and rolling rollers of the device. The gradual impact on the pipe with the use of reciprocating movements virtually eliminates the possibility of deformation;
- winding technique, when the clamps press the structure against a rotating bending roller. In order to avoid crushing of the pipe, a mandrel should be inserted inside it - a metal rod of the corresponding section, having a rounded end. Dorn can be flexible, made of several interconnected sections.
Installation of plastic pipes
When installing compounds of metal-plastic products, two types of fittings are used:
- compression;
- press (in this case, the use of sliding press fittings or crimp couplings is possible).
Installation of pipes, regardless of the type of fittings, will require the use of:
- measuring tape;
- wrenches;
- calibrator;
- pipe cutter;
- chamfer;
- expander (if press fitting is used).
It is undesirable to use compression fittings in hard-to-reach places, since over time they need to be tightened to keep the connection tight.
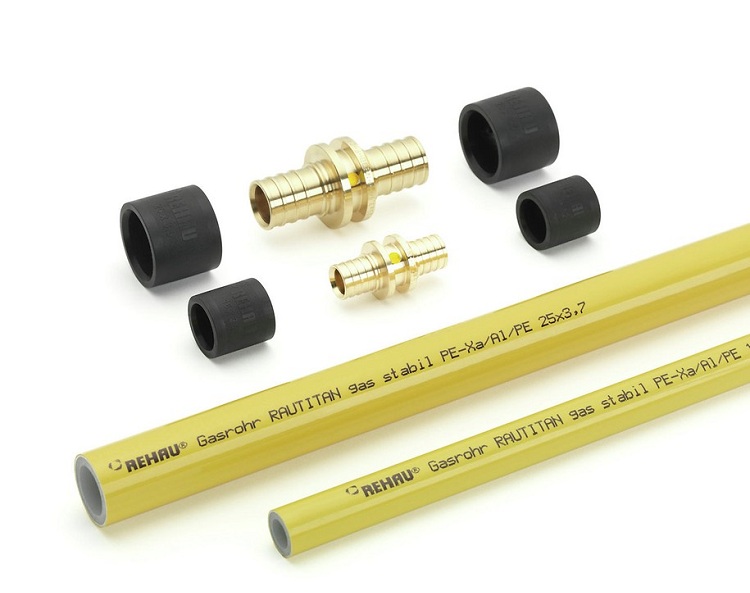
MP pipes are connected by different types of fittings, for the installation of each type you will need your own tool
Press fittings are more practical as they form one-piece joints. Therefore, they can be installed in inaccessible places. For the installation of press fittings, special press pliers are required:
- hand held;
- with hydraulic drive;
- with electric drive.
Before applying press tongs, it will be necessary to carry out preparatory operations:
- A pipe is cut perpendicularly.
- The chamfer is removed.
- The calibrator sets the desired pipe diameter.
- A sleeve is put on.
- The fitting part of the fitting is inserted all the way into the pipe.
Regardless of the principle of operation, press tongs for metal-plastic products ensure their reliable connection with a single effort. The junction is crimped down to the stop of the tool handles.
Repair of plastic pipes
Installation of metal-plastic pipes for heating most often causes a need for repair. If a leak is detected in one of the heating pipes or in any node in the pipelines, the nature of the damage should be determined. And then decide how to work. If a leak occurs under the compression fitting, sometimes it is enough to tighten the nut. When the simplest measure did not work, then water is drained from the system and checked:
- sealing ring;
- gaskets;
- evenness of the pipe cut.
The identified problem is eliminated by the use of FUM tape and silicone.
Leakage from press fittings is usually caused by deformation of the soft ring (olives) inside the press fitting. Replacing the olives or installing a tight-fitting coupling instead of a fitting, or inserting a copper shunt will help out.
If a crack is detected in the pipe itself, then you can:
- close the fistula of small size by cold welding after draining the water (readiness for operation will come in a day);
- apply a bandage (preferably metal clamps) protruding beyond the edges of the damage by at least two centimeters, using rubber 2-5 mm thick.
The best repair method is to immediately replace a damaged metal-plastic construction.
Plastic pipes will last long and reliably if during their installation to use high-quality special tools without violating technology.