Polymer thermoplastic and thermoset tubes are widely used due to the relatively low cost, durability and reliability in operation. They are used mainly for pipelines for various purposes, through which water and other liquids, gaseous substances are transported. Another popular area of application is the laying of communication cables, electrical, fiber-optic, where they are used as a protective sheath.
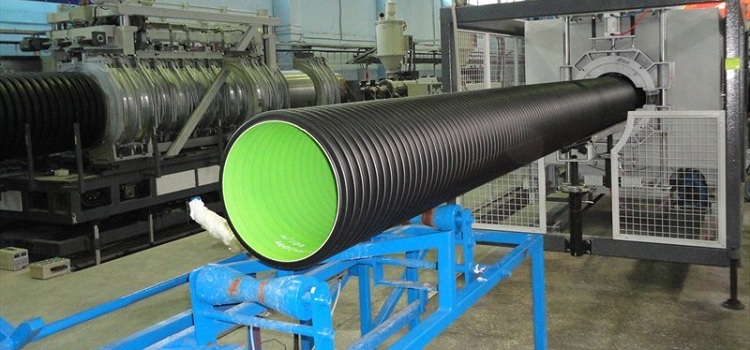
A large number of types of pipes used for the construction of various highways are produced from polymeric materials.
Content
- 1 International labeling of polymer thermoplastic pipes
- 2 Marking of polymer pipes according to Russian GOST
- 3 Polymer water pipes versus steel
- 4 Polymer water, sewer and gas pipes
- 5 Metal-polymer pipes: manufacturing and device
- 6 How to label metal pipes
- 7 The use of plastic pipes
- 8 Advantages and disadvantages of plastic pipes
- 9 Fiberglass pipes made of polymer materials
International labeling of polymer thermoplastic pipes
The generally accepted international marking carries a significant amount of information about polymer pipes:
1. About the type of plastic used for manufacturing. Letter designations refer respectively:
- PE-AL-PE - to simple polyethylene;
- PERT-AL-PERT - to heat-resistant polyethylene;
- PEX-AL-PEX - to cross-linked polyethylene (a-pyroxide, b-silane, c-electron, d - obtained azo compound of molecules);
- PP-AL-PP - to polypropylene;
- PB - to polybutylene;
- PVC-C - to chlorinated polyvinyl chloride.
2. On the diameter of the product and the minimum wall thickness (in mm, inches).
3. About working and maximum pressure.
4. About the appointment for the working environment that will be transported.
5. About the batch number, production date.
It is recommended that manufacturers mark polymeric thermoplastic pipes in such a way that they are readable during inspection and repair work.
Marking of polymer pipes according to Russian GOST
GOST and technical specifications approved by the State Standard of the Russian Federation describe the following types of polymer pipes according to the material of manufacture:
- PVC - polyvinyl chloride;
- PE - low, medium and high density polyethylene, as well as cross-linked polyethylene;
- PP - polypropylene;
- PA - polyamide;
- PB - polybutene.
According to Russian standards, data similar to those included in the requirements of international marking are entered in the marking. Information on operational parameters is required to be indicated in the passport (technical) documentation.
Polymer water pipes versus steel
The advantages of laying polymer pipeline systems are visibly manifested by the example of the use of polyethylene pipes:
- low cost of production, transportation (almost twice) and installation (2-2.5 times);
- pipeline laying is accelerated by at least ten times;
- environmental friendliness achieved by gentle laying methods;
- elasticity allows you to solve problems associated with turns of the track;
- low roughness leads to a large throughput of 10-15%;
- high anticorrosion resistance eliminates the need for additional insulation, arrangement of electrochemical protection;
- eliminates the cost of maintaining highly qualified personnel and checking welded joints;
- the probability of errors by operators is reduced to minimal automation of the installation process.
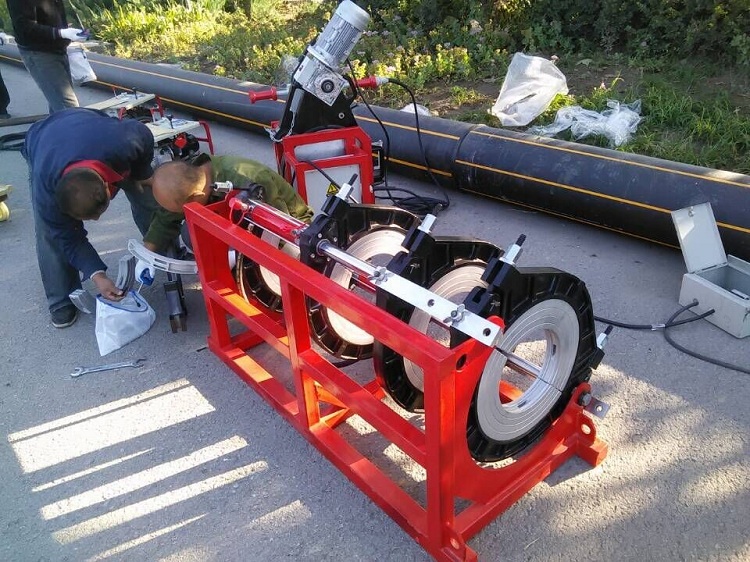
The installation speed of PE pipes and the absence of errors in operation is due to the use of automatic welding machines
In addition, the maintenance of the pipeline laid from polyethylene pipes will require very low costs, and it will work for at least two and a half decades.
Polymer water, sewer and gas pipes
Polyethylene pipes were initially used only for cold water supply. The invention of cross-linked polyethylene, which is resistant to ultraviolet radiation, is more durable and is used when water is supplied with a temperature of up to 95º C, which allowed to occupy about half of the polymer pipe market. Cross-linked polyethylene pipes are suitable for hot water and heating systems. It is from cross-linked polyethylene that the pipes of the largest diameter are made (Norwegian hard-walled pressure pipes - up to 2 m, German polymer composite PE pipes - up to 4 m in diameter, designed for operating pressures up to 20 bar). Polyethylene pipes are used in gas networks of low and medium pressure.
Polypropylene products are similar in properties, but are more rigidly made of cross-linked polyethylene. Therefore, they are produced as measured segments, which complicates the transportation and installation.
Polyvinyl chloride structures are used in drainage and sewer systems (the presence of chlorine precludes use for water supply). They are insensitive to ultraviolet radiation, are characterized by reduced flammability and increased chemical resistance.
Polybutene pipes are similar in properties to products made of cross-linked polyethylene; they differ from polypropylene pipes in elasticity. They are used for hot water supply, heating (for example, the arrangement of underfloor heating).
Metal-polymer pipes: manufacturing and device
A special place among polymer structures belongs to metal-polymer ones. The technology of their manufacture is not difficult. It includes four stages:
- From the extruder (a machine that processes polymer raw materials into a homogeneous molten mass), the inner shell of the product obtained by extrusion comes.
- A special adhesive layer is applied to it to connect with the carrier layer. Its aluminum foil is overlapped or butt welded by laser welding.
- A layer of aluminum foil is coated with a special adhesive layer and covered with an outer shell, which is formed similarly to the inner one.
- The resulting compound is crimped.
The inner polymer layer reliably protects the aluminum shell from the aggressive effects of the working fluid moving through the pipes and prevents the formation of condensate. The outer polymer layer eliminates exposure to the aluminum core of moisture and oxygen. Double-sided protection reduces the thermal conductivity of the product, eliminates the destruction of the aluminum layer, which provides the design with advantages such as strength and flexibility.
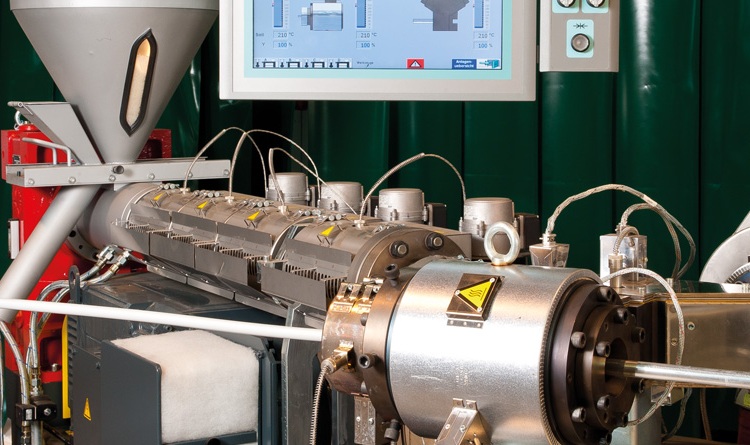
A metal-plastic pipe is a multilayer product, and it is produced using a more complex technology than conventional polymer parts
How to label metal pipes
The most popular among polymer products are metal-plastic. Marking of metal plastic by different manufacturers has some differences. But all of them without fail indicate:
- Manufacturing company.
- Certificate of conformity. The product was manufactured according to him.
- Design features of the product.The material used for production is marked with letter designations (for polypropylene - PP-R, for polyethylene - PE-R, for cross-linked polyethylene - PE-X).
- The diameter of the pipe (and wall thickness) is indicated in mm, its values are in the range from 10 to 1200 mm. However, occasionally the diameter is indicated in inches.
- Pressure rating It means continuous water pressure (in kgf / cm2 (PN) or in bars) in a product at an external temperature of 20º С. A fifty-year warranty on a plastic pipe means that it is used in the described conditions.
- Suitable for transportation medium.
- Date of manufacture, batch number.
It is strongly recommended that marking is always kept in mind when laying metal-plastic structures. This will greatly facilitate maintenance and repair, because you can immediately determine what type of product was used.
The use of plastic pipes
Metal-polymer parts account for about half of the total polymer production. Such a large share is due to the fact that these products, characterized by excellent performance, find the most diverse applications.
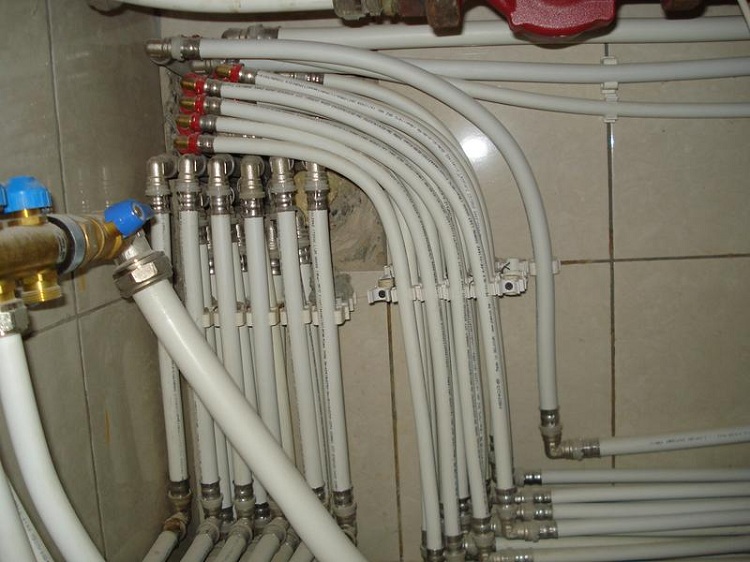
The properties and characteristics of metal-plastic pipes allow their use in heating and domestic hot water
The most famous areas of use of steel pipes:
- transportation of liquids, gaseous substances, compressed air;
- air conditioning systems;
- cable shielding.
Almost everyone has to deal with metal-plastic structures installed in water supply systems. Moreover, for the supply of drinking water, since the polymers in their composition do not have harmful impurities.
With all the advantages of metal plastic, including the convenience of installation, its use is strictly excluded:
- next to a source of thermal radiation, the surface of which is heated to 150º C;
- if the working pressure is planned more than 10 bar;
- if the fire safety standards set the category "G";
- in a central heating system having elevator units.
Advantages and disadvantages of plastic pipes
The distribution of metal is provided by its characteristic qualities:
- non toxicity;
- antistatic, excluding the influence of stray currents;
- resistance to corrosion;
- resistance to aggressive environments;
- low thermal conductivity;
- good soundproofing;
- increased throughput;
- ductility;
- ease of installation and ease of repair;
- aesthetic appearance.
The disadvantages are also called, although it is more correct to talk about the features of operation:
- It is necessary to take into account the difference in the expansion coefficients of metal and plastic, which are part of the product. Therefore, in order to avoid leakage of the joints, the pipes are not laid tight, but on the bends provide compensation loops.
- Bending is allowed only a certain radius, multiple bends should be avoided.
- It is impossible to twist relative to the central axis of the pipe.
Taking these features into account will allow one of the main advantages of metal-polymer compounds to be realized - durability and reliability.
Fiberglass pipes made of polymer materials
Composite thermosetting pipes are used in structures that are intended to operate in difficult conditions. Among the fields of application of fiberglass (in English-speaking countries it is customary to call it thermosetting):
- aviation;
- gas production;
- shipbuilding;
- astronautics;
- petrochemical industry.
Fiberglass pipes are most common in the same areas as other similar polymer products - transporting liquids and gaseous mixtures, laying electrical and other cables.
The manufacture of fiberglass pipes for various purposes is carried out using such materials:
- basalt, glass, carbon and synthetic fibers;
- rubber, rubber plastics and fluoroplastics;
- binding materials (resins, adhesives).
Fiberglass products are distinguished by strength, stiffness, chemical resistance and low weight, durability.
A variety of polymer pipes continue to successfully displace metal counterparts. Work does not stop on improving polymer products, improving the quality of their operational characteristics, and expanding areas of application.