Any elements and equipment of heating or plumbing systems have an operational life. The optimal solution for arranging such networks is plastic communications. In case of repair (replacement), it may be necessary to install pipes made of cross-linked polyethylene. An important role in this process is played by the knowledge of the features, the nuances of the work, as well as the required tools and materials.
Content
Some material features
Polyethylene is obtained by ethylene polymerization. The process of its “stitching” consists in such a transformation of the internal structure of the material, in which the chemical composition remains unchanged. The technology expands the capabilities, characteristics and applicability of products from cross-linked polyethylene. The most valuable benefits of the pipe are:
- resistance to high temperatures: in the absence of pressure withstands up to 200 ºС without changing the configuration;
- good impact resistance even at temperatures up to -50 ºС;
- maintaining a balance between elasticity and hardness;
- anticorrosion properties;
- perfect smoothness, flexibility, damping ability of mechanical vibrations and sounds;
- resistance to various chemicals;
- lack of heavy metals in the composition;
- the ability to bend freely without breaking;
- small dimensions, weight, long service life.
Such polymer products have the property of shrinkage - the adoption of its original shape some time after stretching. In addition, the installation does not require special sophisticated tools for pipes made of cross-linked polyethylene.
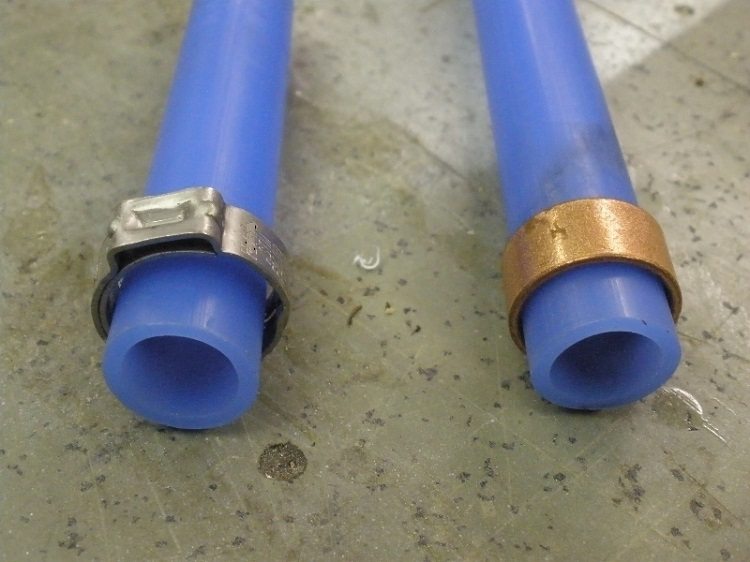
Cross-linked polyethylene pipes are highly durable and resistant to elevated temperatures and pressure.
Stitching process
The crosslinking process is aimed at eliminating one of the main disadvantages - thermoplasticity. The output is polyethylene, which remains flexible, but does not deform at temperatures above 80 degrees.
Note! Due to the fact that the basis of the sewn polymer is pure carbon, when exposed to temperatures above 400 ºС, the material will begin to melt.
Technical parameters of the product depend on the chosen method of obtaining crosslinking:
- silane;
- peroxide;
- electron beam.
In the first method, a substitution reaction occurs using a silane (reagent). The second method is characterized by preliminary mixing of the raw material and the inhibitor, and the crosslinking process is performed under pressure. The third direction applies irradiation, under the influence of which the formation of additional bonds and substitution occurs.
Products for mounting various systems
The necessary tools for installation and suitable pipes are determined by the field of application of the products. The supply of hot water for heating, cold water, the withdrawal of sewage occurs under different conditions, therefore, the characteristics of the products require different.
So, when supplying cold water, single-layer communications from cross-linked polyethylene with a diameter of 16-20 millimeters and a working temperature of up to 95 degrees are usually used. These pipes are mainly obtained by the electron beam method, which determines their affordable cost.
The supply of hot water requires the use of multilayer structures, since resistance to heating and temperature extremes should be up to 110 degrees. Such pipes have an inner layer of cross-linked polyethylene, which is obtained by the peroxide method, then aluminum and again polyethylene.
Aluminum in the design of the product gives it bending strength and prevents the access of oxygen. The outer layer protects against mechanical damage and ultraviolet radiation. The pipes have a diameter of 16-63 mm. Products for heating are also multi-layered with sizes of 16-20 mm.
The main types of fittings
Cross-linked polyethylene communications bend well after heating. To perform system turns, it is enough to have one tool - a building hair dryer. When installing networks, it may be necessary not only to bend, but also to connect two pieces of pipe. This is possible thanks to fittings.
By appointment, they are of the following types:
- squares;
- coupling fittings;
- drives;
- stubs;
- crosses, tees.
It is convenient to use angles in places of a planned change in the direction of the pipeline. Rectilinear segments can be joined by fittings-couplings. Bends are used to connect a new segment to the existing product, crosses and tees - for piping, plugs - to close its ends.
Fittings are also divided by material:
- polypropylene;
- polyethylene;
- combined;
- polyvinyl chloride.
The most common are brass connectors. There are also direct (for joining pipes of the same diameter) and reducing (for connecting pipes of different diameters) fittings.
Pipe Connection Options
There are three main ways to connect cross-linked polyethylene pipes. Installation tools in each case are somewhat different. The easiest is to use compression (crimp) fittings. Distinctive features of a system with such connections are:
- the possibility of simple dismantling at the required time;
- simple tool;
- applicability for "cold" and "hot" pipelines.
Another way of joining segments is with press-fit fittings (press fittings). In this case, one-piece but very reliable connections are obtained. In this case, the property of cross-linked polyethylene is used to restore shape after deformation. Polymer molecules after crimping on the fitting, straightening, fill special gaps, indentations and create a very reliable connection.
Note! When choosing the appropriate option, it is important to consider the expected pressure in the future network, since the maximum limit for compression fittings is 2.5 atm, for pressure fittings from 5 to 6 atm.
The third method - the use of electrofusion fittings for cross-linked polyethylene - is the rarest, but allows you to get the most durable compounds (comparable to a monolith). For its implementation, a special tool and skills for such work are needed.
Docking with compression fittings
To carry out work on installing communications from cross-linked polyethylene, you will need such a tool:
- pruning shears;
- two wrenches.
Directly installation work is carried out in a certain sequence. First, a crimp nut is put on the end of the product so that its thread is facing toward the connector. Next, fixation of the split ring is necessary. Its edge should be located at a distance of 1 mm relative to the pipe cut.
At the next stage of the process, a cross-linked polyethylene product with a ring and a compression nut is put on the fitting fitting until it stops. The latter is tightened to a snug fit with two wrenches. The fitting does not need to be disassembled before pulling the pipe on it, and there is no need to carry out other additional actions, for example, chamfering. When tightening, it is important to control the degree of effort so as not to damage the pipe.
Crimp connection
To implement the connection on press fittings, you need the following tool:
- scissors for cutting pipes;
- expansion gun having nozzles of different diameters;
- vice for crimping.
First, the end of the pipe made of cross-linked polyethylene is trimmed as neatly and evenly as possible with special scissors.
Note! The slice of the product should be strictly perpendicular to its axis, without burrs and other defects.
Then a sleeve is put on, to which the crimping method will subsequently be applied. It is important to consider that it is worn before performing the expansion of the inlet of the pipe itself, since then the sleeve simply will not fit.
After that, picking up the nozzle of the required diameter and using a special tool - a gun for expansion, the input (end) of the product is increased in diameter by several millimeters. The fitting fitting is inserted into the resulting hole. The lubrication, which is usually included in the kit for assembling such systems, will help facilitate the process.
The final step is to fix the sleeve with a tool for crimping cross-linked polyethylene pipes. Work with a vice carefully, so as not to damage the docking station.
Important aspects of pipe installation
Before starting installation work, a diagram of the future pipeline is drawn up. It is necessary to calculate the number of pipes, adapters and connecting fittings that you need to purchase. The right tool is also being prepared.
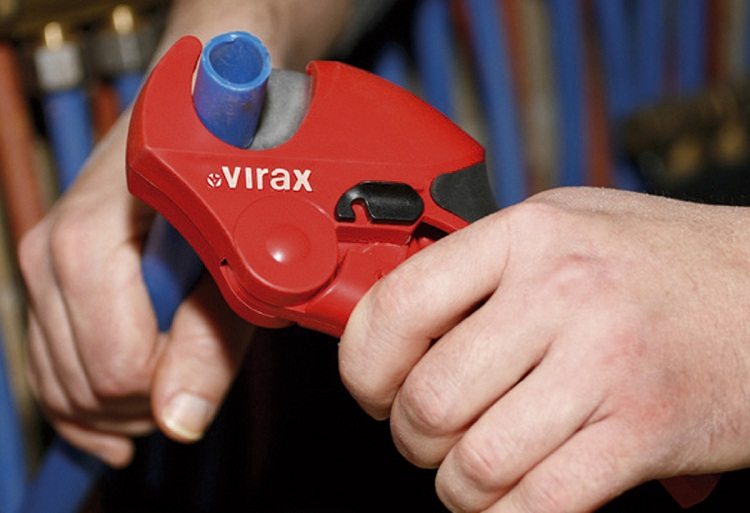
The reliability of the connection largely depends on the end of the pipe, so for cutting you need to use a sharp (preferably special) tool
According to the scheme, pipes are cut into pieces of different sizes. It is advisable to carry out a preliminary check of the correctness of preparatory actions by placing all parts of the system on the floor in a certain sequence.
All connecting elements must be parallel to each other. Even the slightest distortions during the arrangement of fittings and pipes are unacceptable. Otherwise, the reliability of the connection will be in question.
Work with a press clamp step by step is as follows:
- fully capture the connection tool;
- switch the lever to the “up” position for crimping;
- bring the expander's handles so that the sleeve slides to the fitting flange;
- bring the lever to its original position ("down");
- move the handles together and then sharply raise the movable part by 90º so that the tool returns to its original position.
Installation work must be carried out in compliance with safety standards (protection of eyes, hands).
Installation and crimping of pipes made of cross-linked polyethylene can be done independently, if you have the appropriate knowledge and tools. It is important to consider that a particular system has its own requirements for the materials used and installation methods.