Pipes are products that are a type of closed welded profile with a constant cross section. They form various communication systems. In addition, they are used for all sorts of other purposes in construction (for example, a pipe foundation). Today, there are many varieties of pipes according to the material of manufacture. All of them differ in the method of production and purpose.
Content
Scopes of use of different types of pipes
Until recently, various metals were used as pipe materials. Steel, cast iron, copper and other products were widely used in communications and other fields. However, with the development of industrial technologies, products made of various polymer compounds began to appear, which led to large changes in this market segment.
Plastic pipes have a number of undeniable advantages over metal counterparts: the production and cost of such products is cheaper, they have high anti-corrosion performance and have a long service life. They are easy to transport and install and have an aesthetic appearance.
However, the use of plastic pipes is not always possible due to various circumstances. As an example, the use of products from polymeric materials for household gas pipelines is strictly prohibited. This is due to the fact that the structure transporting gas must have high strength characteristics. Therefore, indoor gas pipelines are mounted only from metal pipes.
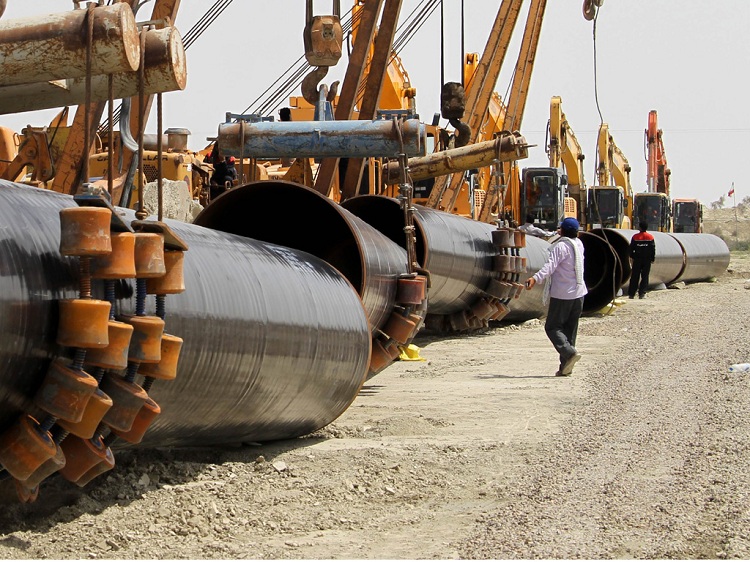
For the construction of highways operating in extreme conditions, only pipes made of steel can be used
Note! In all cases where high strength communications are required, metal parts are used. This is due to the fact that, despite all its advantages, plastic products cannot boast of very high strength. The manufacture of pipelines that require certain technical specifications according to GOST, from such products is prohibited.
Depending on the purpose, the main operational areas of these products can be distinguished:
- Pipes transport various media. The aggregate state of the medium may be liquid or gaseous;
- use as a protective cover for various communications. Most often they are used to protect cables and various wiring;
- use as supports of trunk pipelines;
- for drilling and strengthening wells;
- for water supply systems (household and technical);
- for gas pipelines;
- for sewer communications;
- for chimney constructions;
- for ventilation systems.
You can list only the most common ways to use various pipes. However, this is far from all areas in which communications from these products are used.
Types of pipes
There are a lot of kinds of pipes for pipelines. They may differ in the method of production, material, sectional shape, etc.Pipe production is carried out only on industrial equipment, which allows to achieve high levels of product quality.
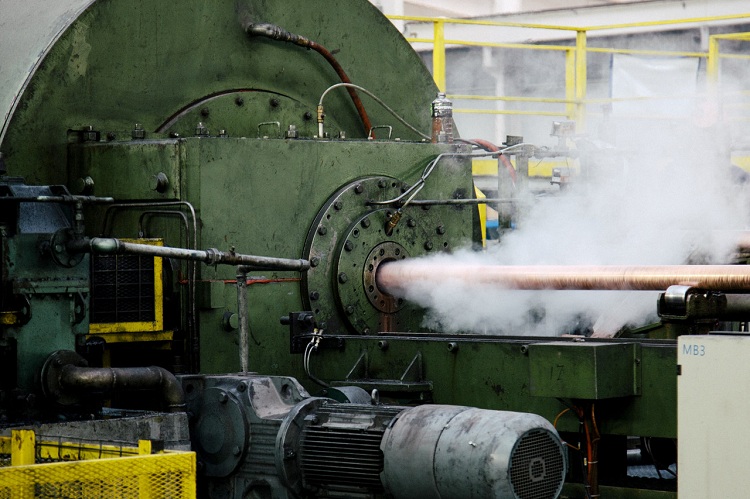
The production of tubular products is a complex process that can take place only in an industrial environment.
Depending on the material used to produce the pipe, several main types of these products are distinguished:
- metal;
- plastic;
- ceramic;
- glass;
- concrete.
Despite the fact that pipelines can be made from various materials, the most popular are metal and plastic products, as well as their combined analogues (metal-plastic).
According to the shape of the section, 4 main types of pipes are distinguished:
- with a round section;
- with a rectangular section;
- with square section;
- with an oval (ovoid) section.
The most popular are products that have a circular cross section. The demand for such products is due to the fact that the round shape does not negatively affect the throughput indicators. Production technologies for different types of pipes are different. This is due to the fact that each material requires an individual approach.
Technologies for the production of metal pipes
The manufacture of metal pipes, despite the growing popularity of polymer products, is very popular today. Without metal pipes, it is difficult to imagine many areas of human life. Such products are distinguished by two main factors: cross-section and destination.
The diameter of the metal tubes varies from 30 to 530 mm, and their length can be from 4 to 12 m. The cross section can have a different shape. The most popular materials from which metal pipelines are made are: steel, cast iron, copper. However, steel products are considered the most popular. Large metallurgical plants are engaged in the production of metal products having different technical characteristics. In order to make a metal pipe, equipment is specially used - pipe rolling machines.
Consider the three main methods by which metal pipes are produced:
- electric welded.
- hot rolled;
- cold deformation.
Welded products are classified by the method of welding on:
- longitudinal welded by high-frequency welding;
- longitudinal welded by electric arc welding;
- products with a helical seam.
The production technology, which involves welding, is very popular and includes 3 main stages:
- Welding rolled metal sheet.
- Profiling.
- Calibration
Important! At each stage of the manufacture of metal pipes, the necessary quality control is mandatory. In addition, the finished parts are tested, which compares the strength and tightness indicators with GOST standards.
Indicators of the outer cross section of longitudinal-seam products vary from 14 to 120 mm, and parts with a screw-shaped seam can have an outer diameter of up to 1500 mm.
The second popular method by which metal products are made is hot-rolled. It includes such stages:
- Heated workpiece to the desired temperature.
- Firmware.
- Rolling.
The wall thickness of such metal rolling varies from 25 to 45 mm. Using the hot rolled method requires compliance with all necessary technical requirements. Products manufactured by any of the methods are regulated by GOST.
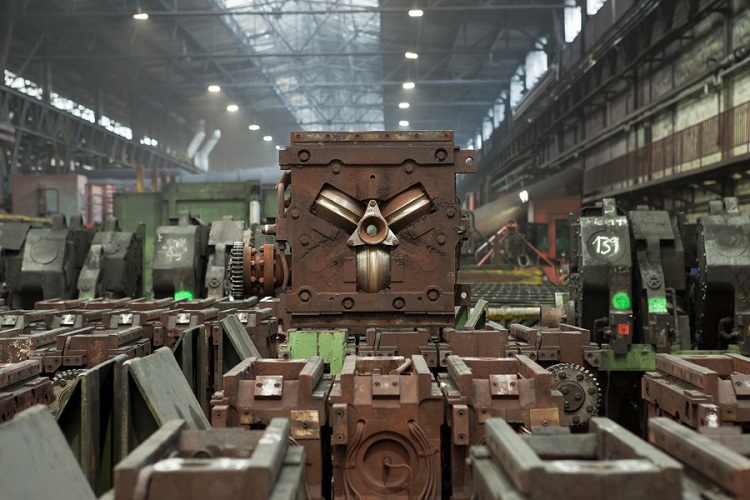
The cold rolling method involves the use of a rolling machine equipped with rollers that form the pipe
The cold deformation method includes:
- Cold rolling.
- Drawing.
A hot rolled billet is used for this method. Cold deformation allows to reduce the cross-sectional area and increase the degree of stretching (approximately 9 times). The outer cross section in this case can be from 20 to 140 mm, and the wall thickness is 0.5–12 mm.
Plastic Pipe Production Technology
The manufacture of plastic pipelines implies the use of a certain polymer, which is processed and then given the desired shape. The necessary raw materials are first prepared for processing, and then parts are made from it for pipelines of the necessary configuration. The method by which parts for pipelines are made from primary raw materials is called extrusion.
Consider the main stages of the production of plastic pipes:
- Training. This step involves mixing and grinding the raw materials.
- Heating. At this stage, the polymer mass is passed through several temperature chambers, which allows heating to be performed gradually.
- The formation of the workpiece. It is produced in special equipment - an extruder. The heated raw material is pumped into the extruder chamber, where it passes through the forming element, the die.
- Cooling. Cool the resulting workpiece with hot water.
- Calibration At this stage, the part is processed in a vacuum calibrator, after which it acquires the final size and shape.
Helpful information! What type of raw material will depend on the type of feedstock. And also in what area it will be operated.
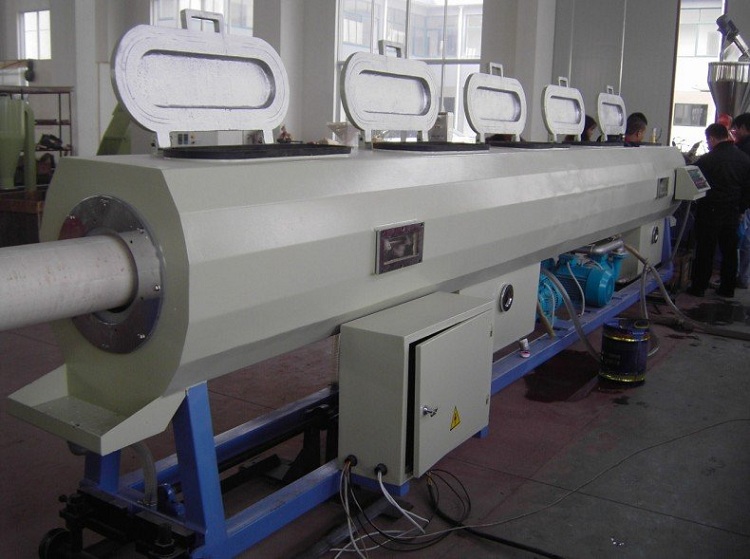
Polymer pipes are manufactured on special equipment - an extruder, and the process itself is called "continuous extrusion"
Today, plastic products are represented by several major polymers:
- polypropylene (PP);
- polyvinyl chloride (PVC);
- polyethylene (PE).
Overview of Polymer Materials
Polypropylene. Polypropylene pipes can be made from such raw materials:
- PP + random copolymer;
- PP + homopolymer.
The first material is obtained by copolymerization of propylene and ethylene in the required proportions. The output is white granules that are labeled PPRC. Pipes and fittings are made from such granules. As a rule, this method is used by European companies. Sewer pipes and various components for them are made from a combination of PP with a homopolymer. Such material is characterized by low strength and is suitable only for the installation of internal pressureless (gravity) sewer communications.
Polyvinyl chloride. The raw material used for the production of PVC pipes is a granular polymer with various additives:
- catalysts that affect the polymerization reaction rate;
- inhibitors that slow down unnecessary processes;
- stabilizers to achieve the desired technical characteristics of the final product;
- plasticizers, which give plasticity to parts;
- dyes, allowing to obtain the part of the desired color.
Industry does not stand still and production technologies are constantly being improved. Not so long ago, in the production of PVC pipes, a two-axis-oriented method began to be used, which can be of two types:
- two-stage periodic;
- single line.
Polyethylene. Such products are by and large represented by low pressure polyethylene (HDPE). In order to obtain such a pipe, special raw materials are used. It can be of two brands:
- PE-80;
- PE-100.
Products made of these materials are characterized by rather high strength, which allows them to expand their operational area.
Ceramic Pipe Production
The technology for the production of ceramic pipes includes the same equipment as when making bricks.Clay forming equipment performs vacuum processing and compaction of the material. This method can be considered a plastic formation.
The process itself consists of several stages:
- Grinding clay, resulting in undesirable clods being broken;
- Mixing special additives that affect the strength characteristics of the final product;
- Preparation of material for forming parts;
- Formation of the part.
- The formation of the connecting element is a bell.
- Trimming the part to the required length.
- Drying parts.
- Clay pipe firing.
- At the last stage, a special glaze is applied to the products.
The drying process is carried out in special dryers, which are called tunnel dryers. Firing, in turn, is carried out in a tunnel kiln. Glazing is carried out by immersing the clay product in the pool with glaze.
Concrete Pipe Production
The production of concrete pipelines is carried out using several technologies. Consider them:
- centrifuge method;
- vibration shaping;
- radial pressing;
The most popular method is vibration shaping. This is due to the fact that this method has several advantages:
- high speed compaction of concrete;
- material uniformity;
- pipes produced by vibration forming are characterized by high strength characteristics;
- such production can be fully automated.
The centrifugation process involves the use of a special centrifuge. Concrete, during the rotation of the form, is evenly distributed along its inner walls, thereby forming a pipe.
Helpful information! The highest quality products are obtained by combining methods (for example, combining centrifugation with vibropressing).
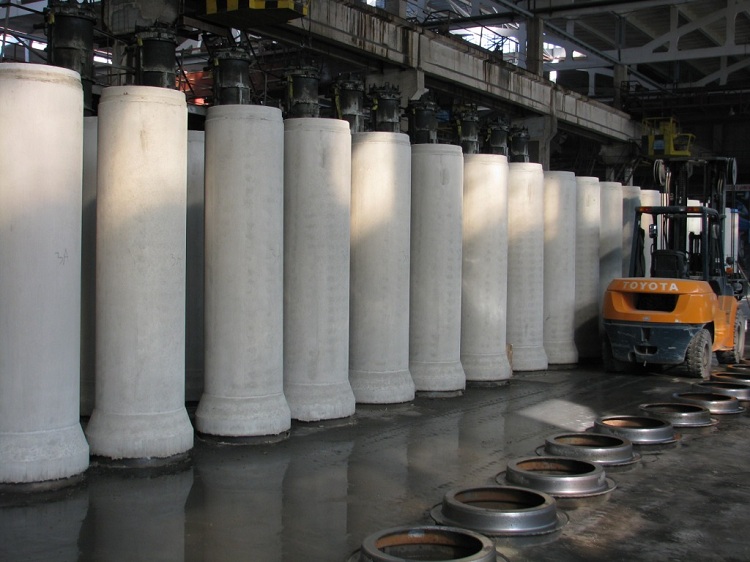
Concrete pipes are available in a very wide range and such products are popular in many areas of construction
The radial-press method is carried out using a press that rotates in the radial direction, distributing and pressing concrete. In addition, during rotation, the internal walls of the part are grouted.
Glass Pipe Production
Glass pipes are manufactured using mechanized methods. Manual methods, which were very popular earlier, have been supplanted by the latest methods.
There are three main ways in which glass pipes are made:
- Products with cross sections up to 50 mm are manufactured using horizontal pulling (GWT).
- Parts with a cross section greater than 50 mm are produced by vertical pulling up.
- Parts with a cross section greater than 50 mm are carried out by vertical pulling down.
Glass that is used to make pipes is usually boiled in a bathroom oven. The operation of such furnaces is characterized by the continuity of the process.
A variety of pipes allows you to choose the product that is most suitable not only for technical parameters, but also for price. Thanks to new technologies and materials, it is possible to significantly reduce the installation costs of both industrial and domestic pipelines.