Today, there are several ways to connect pipes made of low-pressure polyethylene (PNA). The most optimal and practical is the welding method. However, to perform this procedure correctly, one cannot do without knowledge of some technological nuances. It is also worth listening to the opinion of professionals. And even having decided on the method, it is necessary to correctly approach the selection of suitable equipment for welding HDPE pipes.
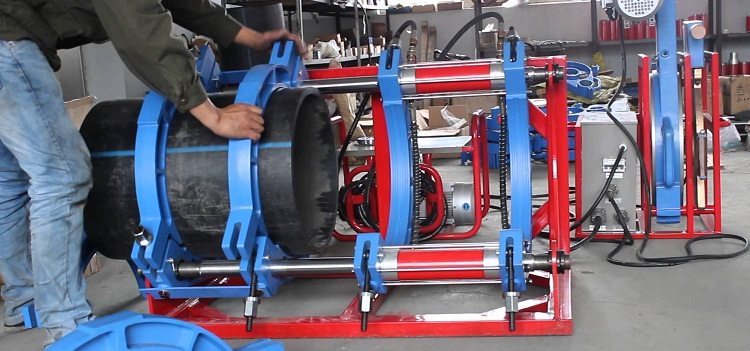
The type of apparatus for welding HDPE pipes is selected depending on the diameter of the products and the method of connection
Content
Connection Methods
Popularity HDPE pipes due, among other things, to the simplicity of their installation. The connection is performed by two main methods:
- detachable;
- one-piece.
To implement the first, connecting parts are used. The second involves the use of an apparatus for welding HDPE pipes. As practice shows, this particular method gives the best results. The welds obtained during welding are absolutely tight and the most durable.
This technology, in turn, is of two types. Consider them in more detail.
Electrofusion method. It uses a special polyethylene coupling with built-in electric spirals. Their ends are output and connected to a special apparatus for electrofusion welding of HDPE pipes. It creates tension and an electric current begins to flow in spirals. As a result, the part is heated to the required temperature, and its surface melts and increases. The molten polyethylene, being limited in space by the inner diameter of the electrofusion coupling, is exposed to the pressure required for welding. Then the device can be turned off.
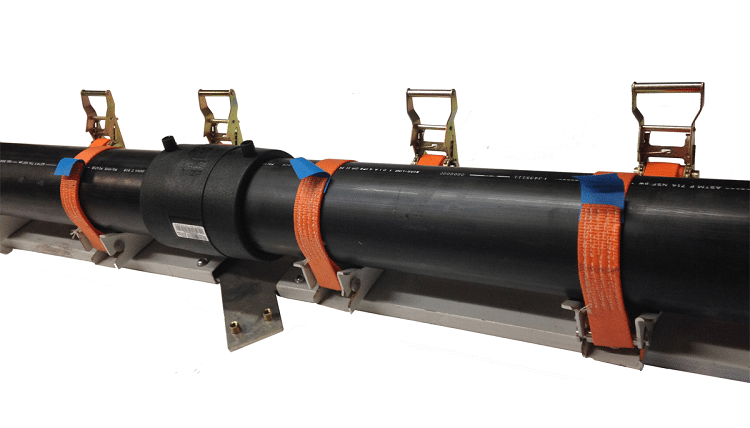
In electrofusion welding, pipes are often fixed with straps so that there is no displacement during heating
Before starting electrofusion welding directly, the ends of the products must be thoroughly cleaned and degreased. It is customary to use this technology when repairing bends and creating taps in an existing system. Its feature is to ensure the immobility of the connected parts during electrofusion welding and until they are completely cooled.
Butt welding. This method is implemented using a special apparatus for welding HDPE pipes. The process itself consists of several stages:
- cleaning the ends of products from contamination with their subsequent degreasing;
- heating the edges to a viscous state using a special heater;
- pressure connection.
Allowing the seams to cool can put the pipeline into operation. Critical for butt welding are the following options:
- heating time;
- temperature;
- the height of the flashing of the ends;
- pressure level on the connected surfaces.
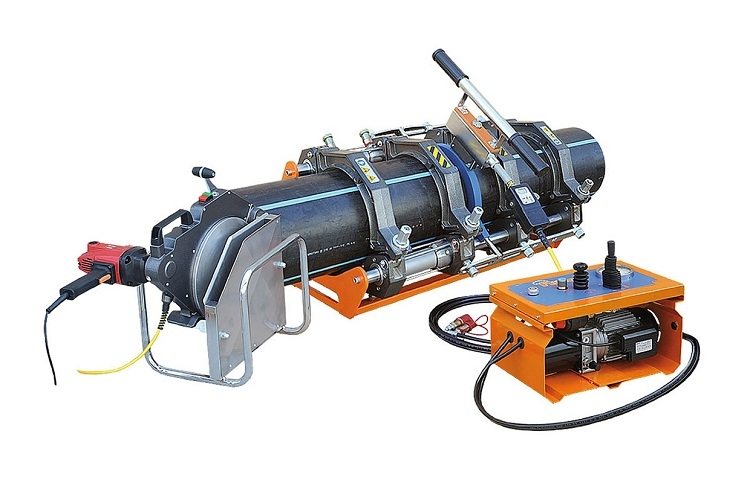
When welding “butt” pipes are rigidly fixed with a special apparatus, which after heating the ends strongly presses them to each other
On a note! Butt welding is the main technology for creating engineering communications from HDPE pipes.
The similarities and differences of various models of apparatus for electrofusion welding HDPE pipes
Relative to all these devices are low weight and low power consumption.Modern models of such equipment provide the ability to work even with samples of minimum sizes in automatic mode. This is explained by the fact that the microprocessor is included in the design of the apparatus for electrofusion welding, which performs the adjustment of parameters, logs data and makes it possible to identify all defects in operation.
But their main differences are as follows:
1. Type and diameter fittingswith which the device is able to work. The type of coupling is determined by the location of the heating coil. It can be closed or open. Large diameter fittings can be used with crimp plates. The latter are intended to be returned to the deformed when cutting ends of the original shape.
2. A set of options for monitoring the progress of the workflow. As a rule, a barcode is applied to the surface of the electrofusion coupling containing information about its characteristics. With the help of a bar-scanner (this device is included in the set of apparatus designed for electrofusion welding of HDPE pipes), the code is read. After that, the received data is automatically or manually entered into the external memory of the microprocessor, which on its basis determines the operating mode.
The device displays information on the duration of the process, heating temperature, voltage, amperage, etc. All these data are stored in the memory of such modern equipment. Most models include a system that signals the start or completion of the process.
3. The number of production modes. The use of such devices necessitates the use of a large number of consumables, which increases the cost of work. But this is offset by the following factors:
- simplicity of the method;
- the ability to perform welding in hard to reach places.
That is why models of this type are most often used in the repair of pipelines. Professionals highlight another serious advantage of this method. It is briefly formulated as follows: the possibility of welding HDPE pipes not only of different diameters, but also made of polymers of different grades.
Butt welding
This type of connection is used for pipes whose diameter is not less than 50 mm, and the wall thickness exceeds 4.5 mm.
Important! Unlike electrofusion, butt welding is allowed to be performed only with pipes made from the same polymer grade.
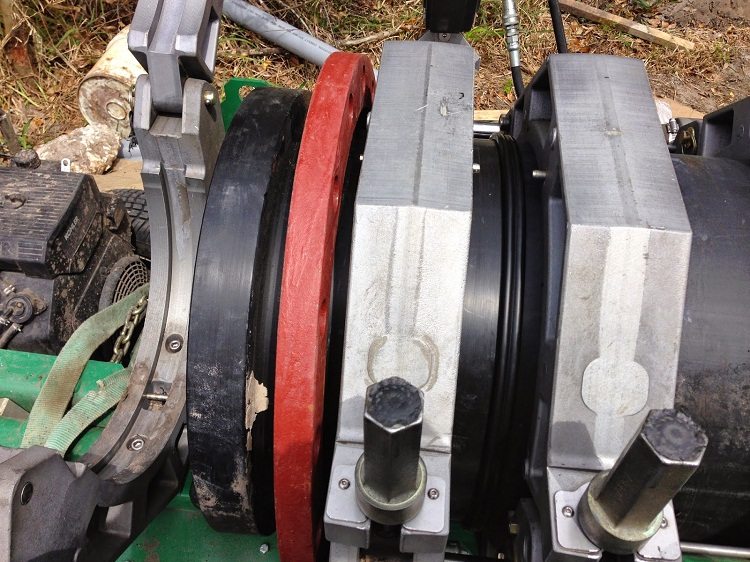
When butt welding is carried out correctly, a “roller" of molten plastic appears in the place of the joined ends
This method involves the following sequence of actions:
- the initial stage is checking the geometry of the pipes. To ensure a tight fit of the ends, the edges must be trimmed and cleaned;
- then, the welded ends of the HDPE pipes are fastened in compliance with the alignment.
- after that, a heating element is started between the ends of the products. When voltage is applied, it heats up, which causes the edges of the pipes to melt;
- then the heating element is removed, and the ends are pressed with the use of force to each other, and are kept under pressure until completely cooled. The extruded layer of molten polyethylene, hardening, forms a weld.
Below is a table of the time required for butt welding.
Table 1
Outside pipe diameter, mm | Heating time, seconds | Connection time, seconds | Cooling time, minutes |
75,0 | 30 | 10 | 8 |
63,0 | 24 | 8 | 6 |
50,0 | 18 | 6 | 4 |
40,0 | 12 | ||
32,0 | 8 | ||
25,0 | 7 | 4 | 2 |
20,0 | 7 | ||
16,0 | 5 |
Without the availability of certain qualifications, it will not be possible to successfully complete all these butt welding operations, since they must be done quickly and accurately with the mandatory observance of all technological requirements.
Types of butt welding machines
Depending on the equipment, the butt welding machine may belong to one of the existing types.
Manual welding mirror. Such a model includes only a heating element - a mirror. All operations, from summing up the ends, and ending with holding them in the right position under pressure, are performed manually.
Such equipment can be classified as high-tech only with a big stretch, since the “human factor” does not contribute to obtaining a high-quality seam. Therefore, low-pressure pipelines, for example, sewer, are welded using mirrors. Their main advantages are low cost and low weight.
Machine for welding HDPE pipes. This is an aggregate of a more complex design, it has a bed. A heating element, a centralizer with clamps, a trimmer and a drive are mounted on it. The centralizer is designed to fix and center the ends. The miter cuts the ends and thus ensures their snug fit.
If we take as a basis the criterion the type of drive that feeds the ends of the pipes and presses them with the ends, then this equipment happens:
- with a mechanical drive. The apparatus activates the muscular force of the welder applied to the lever or screw. Therefore, this type of machine is not used for welding HDPE pipes whose diameter exceeds 160 mm, because the contractor will require excessive efforts;
- hydraulically driven. It is this equipment that is used to connect pipes with diameters of more than 160 mm.
On a note! The cost of a hydraulic apparatus for butt welding of HDPE pipes is much more than the price of a machine with a mechanical drive.
Socket welder
The main detail of such equipment is the heating head. Two heating elements such as nozzles, mandrel and sleeves are fixed on it.

The welding machine for the socket connection of HDPE pipes is applicable for small diameter products
The mandrel melts the inner surface of the coupling, and the sleeve is designed to melt the outer surface of the end part of the HDPE pipe.
The diameters of these accessories are within 16 ≤ D ≤ 40 mm. To perform the welding connection of PND elements of the pipeline, nozzles are subjected to preliminary heating to a temperature of + 220 ° C. Then, on each of them with effort push the end of the pipe and the coupling. After reaching the required degree of heating, the coupling and the end are removed from the nozzles, and are joined under pressure. Allowing the polyethylene to cool, the same operation must be carried out with the other end.
The socket weld joint is most often used indoors. In this case, the diameter should be no more than 40 mm. To work with large sections, a welding machine equipped with a centering device is used.
Overview of manual devices for electrofusion welding from leading manufacturers
The most popular equipment on the world market for carrying out similar work from companies such as Rothenberger, Ritmo and DYTRON.
The table below shows the most popular models of the above companies.
table 2
The brand | Model | Heater power, W | Weight kg | Diameters of welded pipes, mm | |
Ritmo | Prisma 90 | 1000 | 54 | 20-90 | |
Prisma 125 | 1400 | 100 | 25-125 | ||
Rothenberger | ROVELD P 63 | 800 | 1,8 | 60,53,40,32,25,20 | |
ROVELD P 40 | 650 | 1,0 | 40,32,25 20 | ||
ROVELD P 125 | 1300 | 7,5 | Up to 125 | ||
ROVELD P 110 | 1300 | 2,2 | 110,30,75 | ||
DYTRON
|
POLYS P-4a 850W Trace Weld | 850 | 1,6 | 16-75 | |
POLYS P-4a 650W Trace Weld | 650 | 1,3 | 16-63 | ||
POLYS P-4a 1200W Trace Weld | 1200 | 1,8 | 16-125 | ||
Dytron 500W POLYS P-1b | 500 | 1,3 | 16-40 | ||
Dytron 850W POLYS P-1b | 850 | 1,6 | 16-75 | ||
Dytron 650W POLYS P-1b | 650 | 1,3 | 16-63 |
Rothenberger (Germany). The foundation of this brand dates back to 1949. More than half a century of hard and fruitful work of specialists has brought Rothenberger, at first a small company, into the category of world giants. Representative offices of this brand are open in 25 countries of the world, including those countries in which 14 Rothenberger plants operate. And, according to experts, the logo of this company on products means reliability and the highest quality.
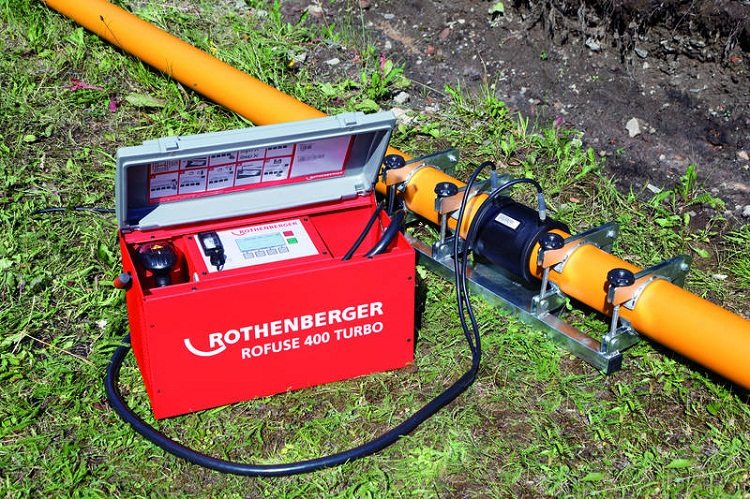
The reliability of the connection and the convenience of work depend on how high-quality equipment is used for welding
Ritmo (Italy). The history of this brand began relatively recently - in 1979. And now he is already one of the world's leading companies specializing in plastics processing technology.Ritmo engineers create high-quality products that comply with strict international and national standards (EEC, ISO, UNI). A high degree of business organization is ensured by a constant analysis by the company's specialists of the situation in this segment of the world market. The Ritmo brand product line includes a full range of equipment and tools for socket, electrofusion and butt welding.
DYTRON (Czech Republic). The company was founded in 1992. The list of its products includes both mobile devices and manual models for the implementation of butt welding of plastic pipes. And every year the range of the company DYTRON replenished with new samples.
Important! One of the significant advantages of this brand is not only that it has an ISO 9001: 2000 quality certificate. In addition, its products also comply with the environmental certificate ISO 14001.
The purchase of any such apparatus will ensure the reliability of the results of manual electrofusion welding.