A pipe bending machine is a device that is used to bend pipes with various cross-sectional shapes. The section of the part can be: square, rectangular, ovoid, round. Such equipment is considered universal, since it can bend parts from different materials: aluminum, copper, brass, as well as stainless and carbon steel. It is also worth noting that such stationary machines can work with a wide range of diameters.
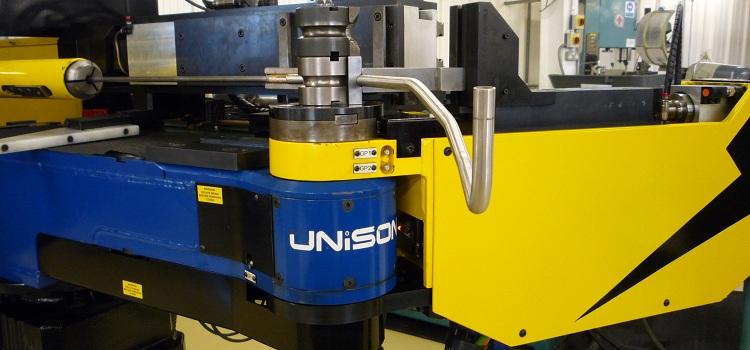
Pipe bending machines come in many different types, the most complex are industrial electronic devices
Content
What is a pipe bending machine for?
Conventional and shaped pipes are used in various fields:
- installation of pipelines of various configurations;
- implementation of frame structures in the construction industry;
- for the organization of fences;
- in the automotive industry;
- in the furniture sector;
- as decorative elements of the interior.
The above options for the use of pipes in most cases require their bending. When installing a pipeline structure, fittings can be used to connect individual communication sections. However, the assembly resulting from the joining of two pipes is considered a problem area and the risk of leakage increases in direct proportion to the number of such assemblies. Therefore, it is much more reliable to bend the pipe at the right angle, without violating its integrity. For bending pipes use special pipe bending equipment.
Helpful information! Pipe benders are used both in special cases and in production enterprises. It is worth saying that these devices bend pipes at an angle of up to 180 °.
The drive system for such equipment may be different:
- hydraulic;
- electromechanical.
Pipe bending machine is a popular and common equipment that is used today in many areas of human activity. If necessary, you can assemble such a machine with your own hands.
Advantages of modern pipe bending machines
Previously, special equipment was used for bending pipes, which was large in size and operated on the principle of induction heating. Induction heating meant raising the temperature of the part at the bend to the desired value (until the metal became plastic enough to bend).
Today, the development of industry allows us to produce more advanced equipment, which differs from old pipe bending machines and has the following advantages:
- more compact dimensions in comparison with old devices. The size of a modern pipe bending machine allows you to do without the organization of a capital foundation for the installation of equipment;
- The minimum loading height of the part is no more than 140 cm from the floor. This indicator is not affected by the diameter of the product;
- reduction in energy consumption in comparison with old pipe benders. New models do not need heating pipes;
- lack of pollution which was observed in old, induction cars;
- the temperature near modern pipe bending equipment is very comfortable;
- in addition, during the operation of such equipment the noise level is reduced, which is also a great advantage;
- high bending speed, which allows you to cope with large volumes of work. For example, a modern pipe bending machine is able to bend a part with a cross-sectional index of 400 mm and a wall thickness of 25 mm in a very short period of time (2-3 minutes).
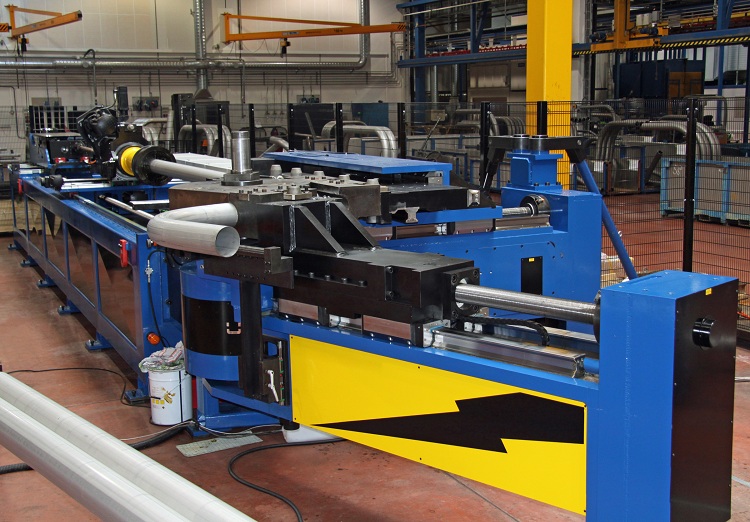
With large volumes of work, a high bending speed is needed, only professional equipment can provide it
Operational areas and service features
Pipe bending machines are most widely used in two sectors:
- construction;
- housing and communal services.
In addition, it is worth noting that bending machines are used less intensively in other areas:
- automotive industry;
- petrochemical industry.
And also such machines are indispensable when performing pneumatic and hydraulic pipeline structures. The operational sphere of this equipment is very wide, therefore it is very popular and in demand everywhere. Let's consider why pipes bent on pipe bending equipment are still used:
- Sports Equipment;
- various design decisions in premises;
- during the installation of fences, railings, stairs, etc .;
- in the manufacture of chairs and other furniture items.
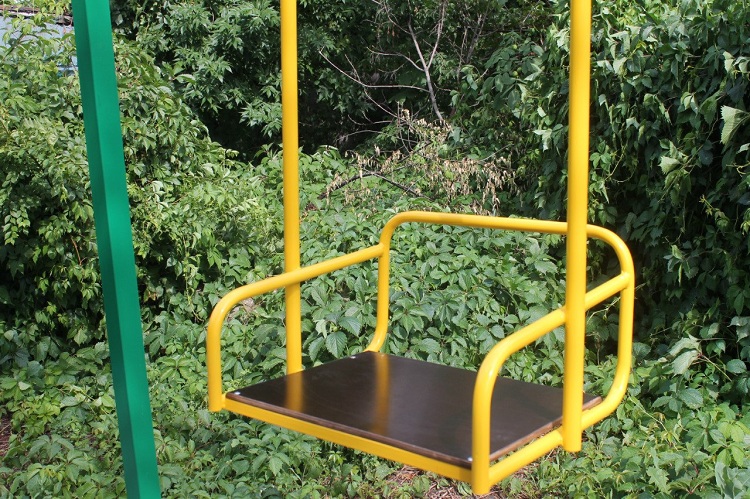
The need for bending pipes may appear in the manufacture of structures of various types and purposes
Important! Before you start bending pipes on a pipe bending machine, you need to read the instructions for its use, and also study all the necessary contraindications, safety rules, etc.
The operator of the pipe bending machine must be trained in all the nuances of bending and, in addition, carry out preventive cleaning of the device (1 time per month), inspection of the main working parts of the device and prevention. The prevention of pipe bending machines include:
- lubrication of work items
- adjustment of working elements;
When preventing the hydraulic model, do not forget about changing the oil in the pump. Pump oil must be high quality. If any functional element of the bending equipment fails, it must be replaced. It is recommended that you buy new parts only from trusted suppliers.
Varieties of pipe bending machines
Today, all pipe bending devices that are used in various enterprises can be classified according to one main indicator - design. Depending on the design features, the following varieties of pipe bending machines are distinguished:
- Tame. Such devices are used in small enterprises and involve the application of physical effort when bending pipes. As a rule, such compact machines are portable and are used in the construction industry. It is worth noting that the mobility of such machines allows you to use them directly on construction sites.
- Hydraulic. Devices that operate from a hydraulic drive are very similar (in design) to manual machines, but can be either portable or stationary. The main difference between such machines from manual models is the presence of a hydraulic booster. This element allows you to process products with cross-sectional indicators up to 20 mm without the use of significant physical effort.
- Electric. They are large in size and function from electricity. When bending parts, such stationary machines provide high angle accuracy. It is also worth noting that an electric industrial pipe bender can bend products with large cross-sectional indicators and thin walls.
All electric pipe bending machines are divided into three main types, depending on how automated they are. Consider these types:
- hand held;
- semi-automatic;
- automatic with a numerical control program (CNC).
Machine tools with a computerized control system are the most functional of all. Thanks to the CNC system, it becomes possible to program the parameters of the angle and bending radius of the part. Such devices can operate in a fully automatic mode, where all processes are controlled by a computer program (including the supply of parts and adjusting the mandrel).
It is worth noting that pipe bending machines for conventional and shaped pipes are different. Manual pipe benders are quite inexpensive, however, they are much less productive than electric models.
Bending methods
Bending pipes on a pipe bending machine may vary depending on the method. Consider 4 options for bending pipes on pipe bending equipment:
- break-in method;
- drawing method;
- rolling method;
- winding method.
The latter method is used for pipes with small cross-sectional indicators (up to 150 mm). The bend itself is quite simple: the part is wound around the roller, thus, by acting on its ends, the desired part is obtained. Previously, this method was different in that it had several disadvantages. The main disadvantage of this method was the deformation of the pipe at the bend (thinning of one wall and the formation of a corrugated surface on the other).
Today this drawback can be avoided if bending is carried out on a pipe bending machine equipped with a special structural element - a mandrel. Dorn is a metal rod that is placed inside the pipe before bending (it eliminates the deformation of its walls).
Note! Dorn pipe bending machines are sold together with a set of mandrels, which have different cross-sectional indicators for certain pipes.
Despite the fact that mandrel equipment is reliable and eliminates the deformation of the walls of products, rootless models are also popular. Due to the limited use, they are used for bending pipes with large cross-sectional parameters and thin walls.
Work principles
The principle of operation of all existing models of pipe bending machines has one common property - the bending of the part is performed in the cold state (unlike old, induction devices). Bending in the cold state is a more reliable option, since the accuracy of bending increases, and also significantly reduces the possibility of deformation of the walls of the part.
Cold bending has its drawbacks (for rootless models). The main disadvantage of cold bending on a bottomless machine is that during the process the load on the part increases, as a result of which the shape of the pipe section is deformed. This is especially true for pipes made of alloy steel. Such deformation, as a rule, appears due to tensile stress that acts on the walls of the product. It is not balanced by the compressive stress appearing on the inner wall of the part.
The movement of the mandrel element during the bending of a conventional pipe excludes its use for the cross section of a shaped article. The pipe bender for the profile pipe is equipped with a mandrel, which is different from ordinary ones. Dorn profile bending occurs in this way: a profiled roller is rolled around a fixed, fixed profile pipe. In this case, fixing the part can be of two types:
- hydraulic;
- mechanical.
It is also worth noting that the same process is carried out in the case of using angle bending equipment. Such equipment is large in size and very functional.
How to make a pipe bending machine with your own hands?
Before proceeding with the implementation of a manual tube bending machine, it is necessary to work out a scheme for its assembly. The pipe bending machine is performed in stages, and during its assembly you need to be very careful. First of all, a scheme is drawn up for its foundation. The frame of the machine is preferably made of profile pipes, which have a rectangular cross-sectional shape. And also do not forget about the strengthening of the walls, as this is necessary for the reliable use of the machine.
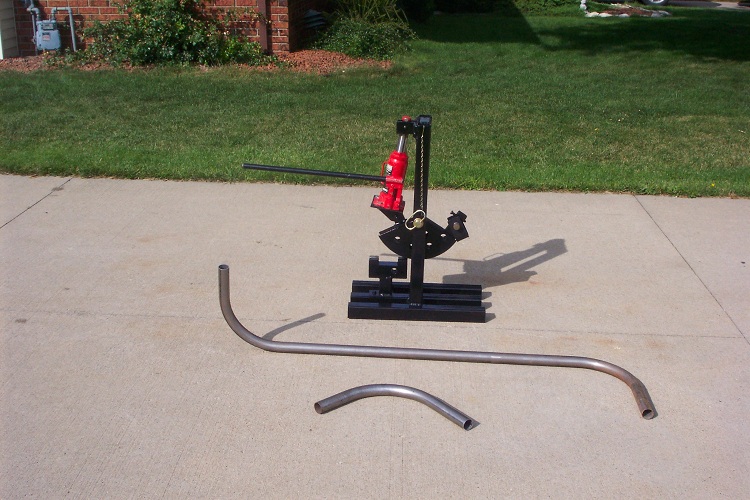
From improvised tools and simple details, you can assemble a homemade pipe bender that will cope with everyday tasks
The handle and clamp for the pipe profile is a stud on which the following elements are fixed on both sides:
- on the one hand, a lock nut with a wing nut is fixed;
- on the other hand, a latch is installed, which has the form of the letter "T".
After the base is made, you can do the execution of the handle of the latch. To do this, you need the following materials:
- two metal plates;
- jumpers.
Let us consider in stages the process of manufacturing such a machine with your own hands (starting with the handle of the clamp):
- Handle plates must be selected with a thickness of approximately 4–5 mm. This is due to the fact that the handle is installed on the body of the axis of the frame, so you should carefully consider the choice of metal plates. It is also worth noting that it is necessary to place these plates on an axis with a margin of approximately 5 mm.
Helpful information! Jumpers are required to achieve the required level of strength and stiffness. They can be made of metal tubes and fixed to the plates using welding equipment.
- The handle pulley can be adjusted to simplify the assembly process of the tube bending machine.
Note! Individual elements, as well as their location, it is desirable to control by means of measuring devices.
- In the third stage, you need to make a hole. The axis itself does not need to be fixed by welding - fixing is done with cotter pins.
- After the handle on the pipe bender is finished, it is necessary to install a pulley on it, which is necessary to impart movement to the drive belt.
- Next, you need to fix the base of the assembled apparatus. For this, as a rule, a vise is used.
- Then, one plate of the bender of the pipe bender is put on the axis of the core.
- The second plate is put on.
- At this stage, the main pulley is installed. Screw the fastener pin into the body of the nut (wide) on the core. The working pulley is fixed to the axis of the base by means of tightening belts.
In this way, the pipe bending machine is assembled with one's own hands. A pipe bender is a useful device with which you can bend a pipe at home. If necessary, you can purchase non-stationary equipment, which costs much less. But if you need a pipe bender more than once, then it is advisable to carefully study the assembly scheme and make it yourself.