Welded steel pipes account for more than half of the total volume of similar products made of this metal. Reduction of their production is not observed, despite the massive distribution of polymeric materials. The reason lies in the high demand from many sectors of the economy interested in products with high strength, especially made of stainless steel.
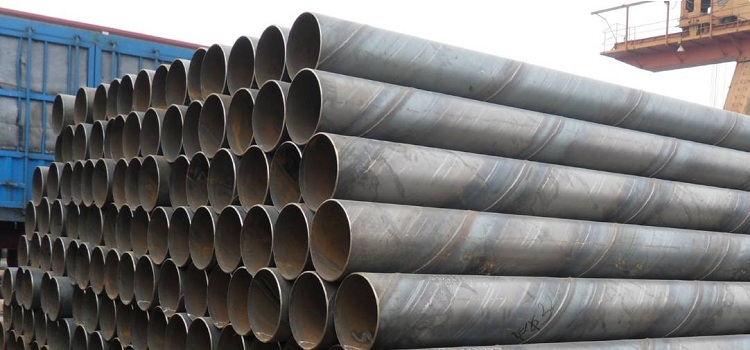
Technical characteristics of pipes manufactured by the welded method vary depending on the type of steel used and the welding method
Content
What materials are welded steel pipes made of?
The material for steel pipes is either sheets whose thickness does not exceed 50 mm, or a tape in rolls. For the manufacture of electric-welded pipes resort to the use of different grades of steel, for the most part:
- carbon. Carbon alloys contain up to 2% carbon with a low content of other impurities. Welded pipes made of carbon steel grades are characterized by strength, hardness and relatively low cost. The increased carbon content makes itself felt in low heat resistance and a tendency to accelerated wear;
- low alloyed. An electric-welded steel pipe made of such materials contains special impurities in an amount not exceeding 2.5% of the total volume.
The presence of certain additives sets the properties of steel, for example, the addition of:
- chromium for the better will affect hardness;
- carbon - on strength, however, elasticity will decrease and fragility will increase during operation at lower temperatures;
- nickel - on strength, ductility and ability to calcine;
- manganese - on hardness and wear resistance, but at the same time plasticity will suffer;
- niobium - on resistance to acidic environments;
- aluminum - on heat resistance and resistance of scale.
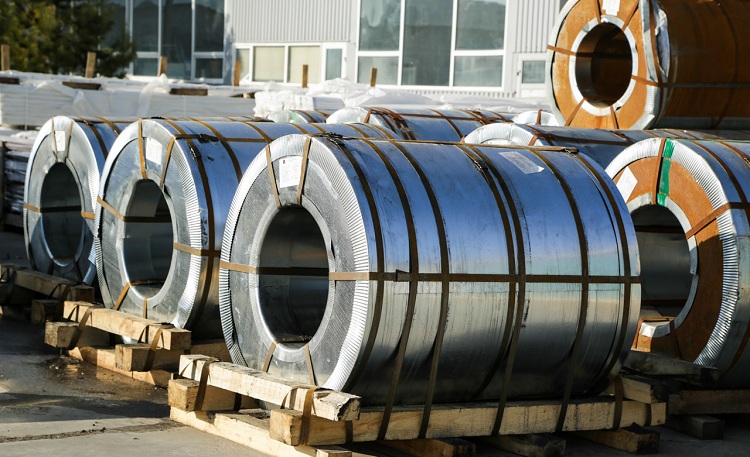
For the manufacture of welded pipes, steel strips are used, which can have different additives - chrome, aluminum, manganese and others
Alloy steels are characterized by increased strength, resistance to corrosion and impact, wear resistance in general, less weight, which redeems a higher cost compared to carbon.
For the manufacture of stainless steel pipes as a starting material, the use of a steel sheet is accepted:
- cold rolled, 0.4-5 mm in thickness;
- hot rolled, 2-50 mm in thickness.
Welded stainless products are made of material that:
- resistant to corrosion;
- relatively easy;
- uncomplicated in processing;
- aesthetically attractive.
Some features of the manufacture of welded pipes
Welded pipes are made:
- straight-seam. The steel sheet (tape) is folded, welding the edges together. The seam (and with a large diameter of the pipe, when one sheet is missing - two seams) runs along the entire length;
- helical. From rolled sheet steel, pipes with a diameter of up to 2520 mm and with a ratio of diameter to wall thickness of more than 100 are obtained.
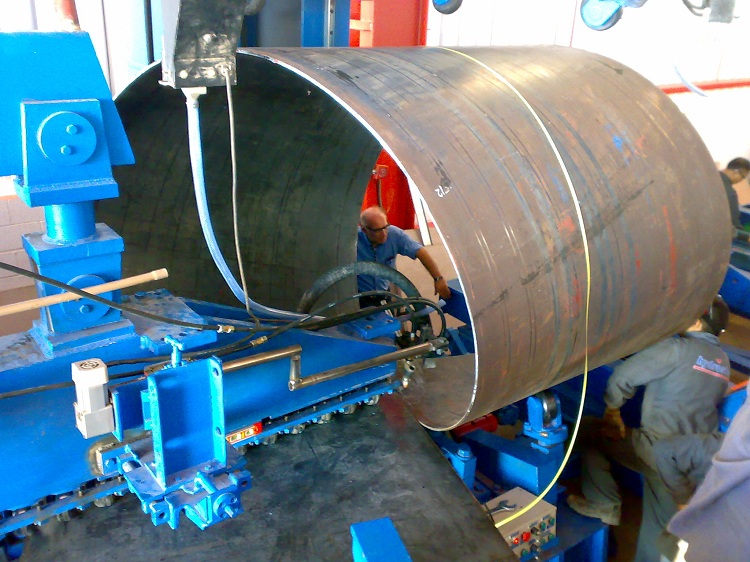
If the strip is folded in a spiral, then the result is a spiral tube, which is characterized by a higher strength compared to straight-seam
The advantages of spiral products include:
- less complexity of the equipment used;
- obstruction of the shape of the seam to the propagation of longitudinal main cracks.
Note! The large length of the spiral seam results in increased welding costs.
For the manufacture of steel pipes, three welding methods are used:
- Stove. The steel strip is heated in a tunnel furnace to 1300º C. When blowing the side edges at the outlet, they are heated to 1400º C, removing the scale. In a forming and welding mill, a hot billet is to be converted into a hot-deformed pipe.
- Electrical are the most common, of which they often use submerged arc. It is electric welding that creates high-quality cold-deformed thin-walled products for trunk pipelines.
- In a protective atmosphere created by an inert gas. Cold-deformed products from stainless and high alloy steels are welded with tungsten electrodes in an environment that excludes contact with atmospheric air to avoid carbidization.
How to get electric welded pipes
As a material for products of small and medium diameter use sheet metal or strips. Joining and righting the workpiece, they get one strip of a certain width, which is paid special attention to ensure accurate convergence of the edges in the future.
As a material for products of small and medium diameter use sheet metal or strips. Joining and righting the workpiece, they get one strip of a certain width, which is paid special attention to ensure accurate convergence of the edges in the future.
- The workpiece is formed on a multi-strand continuous mill using horizontal and vertical rolls.
- Welding HDTV, carried out at a speed of up to 2.5 m / s, creates a seam, to improve the quality of which the burr is removed.
- After calibration, the product turns out to be a regular four-roll stand, where ovality is removed at the same time.
Volatile split and explosive devices of products attached length measured or multiple measured.
For the manufacture of large-diameter pipe rolling on steel sheets fed by a crane to the conveyor line, technological strips are welded to ensure gradual heating of the welding machine. The processing sequence is as follows:
- edges are milled;
- on the edge bending mill, the edges are bent to the desired angle;
- halves of the workpiece are processed on a pipe forming press, the cross section of which is transformed from a hexagonal to a cylindrical one;
- welding begins with the creation of a technological seam, then the future product is welded from the inside and from the outside. Cutting off the technological bars, they perform grinding and dressing, if there is a need;
- after passing the control, which implies the mandatory sending for laboratory testing of several samples from each batch, they proceed to expansion, ensuring the accuracy of a round shape;
- edges are machined;
- After passing through quality control, chamfering and acceptance, anti-corrosion treatment can be carried out, from the inside and from the outside.
A stainless pipe can be made:
- mirror;
- matte;
- polished.
How to get a stainless honed pipe
Often, special demands are made on the surface of steel pipes. As a result of abrasive processing with a special tool, a honed surface, part or element gains higher quality, smoothness and the required microrelief. Using a hone with special abrasive bars, the movement of which is simultaneously rotational and reciprocating, cylindrical surfaces are usually processed.
On a note! Honing process, for example, welded joints of pipelines to improve their aesthetic qualities.
This process can be:
- vibrating. The tool head is given additional vibration;
- flat top. Allows you to eliminate bumps on the surface, aligning the tubercles and dents;
- dry. It is made without the use of cutting fluid;
- electrochemical. Mechanical action is combined with electrochemical.
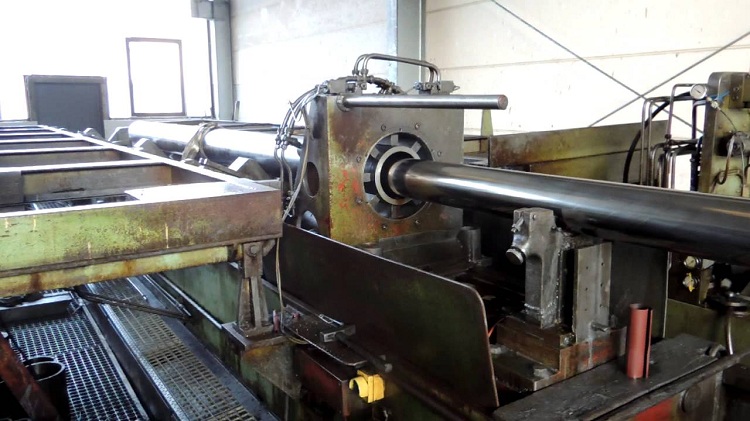
Honing is a type of processing that allows you to remove surface irregularities and improve the quality of the pipes as a whole
For honing multi-bar tools with five to eight cutting elements, a central sliding system equipped with a hydraulic or electromechanical drive is used for their installation. In order for the bar to self-sharpen, that is, for micro-chipping of abrasive grains to occur, it is made of superhard material, diamond or elbor.
The impact of the tool leads to the appearance of micro-cuts on the treated surface, the removal of the thinnest layer of chips, friction and plastic displacement. On a square millimeter of a bar, there can be from twenty to four hundred grains with a size of 20-100 microns. Long primary processing at a speed of up to 4 microns / s eliminates gross errors. In the boundary friction mode, the processing speed increases, and the oscillation frequency of the cutting elements and the pressure produced decrease. In the boundary friction mode, you can achieve:
- greater smoothness;
- specified microrelief parameters;
- increase the strength of the treated surface.
Honing can be done on its own. It is better to use a flexible hon, similar to a brush, which wash bottles. Honing, stocking up:
- a drill;
- honing liquid (or kerosene);
- safety glasses;
- rags.
The surface of the pipe is processed by movements up and down.
It's important to know! The correctness of processing is checked by the pattern that appears on the surface of the workpiece. If it is uniform, with the arrangement of lines between each other at an angle of 60º, then honing is successful.
The hone is removed after the drill stops completely, and the chamfer is carefully removed. The treated element, eliminating traces of abrasive use, is washed using soapy water, dried and, if necessary, anti-corrosion treatment is carried out using a special oil.
The need for welded steel pipes remains in many sectors of the economy. Currently, they serve for laying pipelines for various purposes, act as elements of aggregates and machines, and are used as frames in building structures. Particularly in demand are stainless products, which are used both in industrial production and in design projects. One of the operations that can improve the characteristics of welded steel pipes is honing, which can also be done on its own.