High-quality, practical and durable pipes made of synthetic materials replace the less durable, massive and difficult to install metal pipes. Apply plastic pipes for the installation of heating systems and water mains. The main advantage is that high-quality welding of polypropylene pipes with your own hands, if necessary equipment accessible even to non-professionals. The temperature of safe operation of plastic pipes is from -10 to + 90 degrees Celsius.
Content
Advantages of polypropylene pipes
Long operating time, high coolant temperature and no corrosion on the inner walls, light weight and quick method of welding polypropylene pipes are the main advantages of polypropylene (PP) pipes. The cost of a reinforced plastic pipe, which is used, for example, in heating systems, is comparable to the price of a metal pipe, but the durability is much more. Even a novice installation engineer knows how to weld a polypropylene pipe correctly.
The marking code for polypropylene pipes, adopted by manufacturers around the world, is the letter designation PN, which means "polypropylene", and a digital code indicating the maximum operating pressure of the pipe. The marking indicates where the product can be used and how to properly heat the heating from this type of polypropylene pipe.
Mounted pipes for heating must withstand significant pressure, taking into account constant heating.
In the absence of direct heating of the external side of the polypropylene pipe from heat sources - a heating boiler, direct sunlight, industrial equipment - the water supply system will work without failures. The temperature is also important, welding of a polypropylene pipe with one's own hands will be impeccable with exact observance of the mode of heating the parts and the minimum number of parts connected by the butt method.
Methods for connecting PP pipes
In order to mount the system correctly, it is necessary to withstand installation technology of PP pipes. The purpose of the project determines the sequence of assembly of the system and what how to weld (cook) a polypropylene pipe.
Types of docking:
- coupling connection - in this case, the end part of the PP pipe is fused with a continuous outlet using a fitting in the form of a coupling. In this case, such a technique for welding polypropylene pipes is most often used when the outer surfaces of polypropylene pipes and the inner surfaces of the coupling are heated, the so-called "socket" welding. The result is a strong, reliable and tight joint, subject to all stages of welding and the temperature of heating. The method of socket welding of polypropylene pipes is the most common;
- butt joint. Welded surfaces - end sections of the lead branch and the mate of the polypropylene pipeline. Butt welding is most often used when pipe laying large (from 40mm and above) diameter.
- The technology for welding large diameter polypropylene pipes involves the use of special, professional equipment. The compound has high strength. If the temperature and the clamping force are correctly selected, the connection is tight;
- connection using clamping or self-locking fittings. It is rational to use for the main pipelines with a low level of pressure;
- cold welding of a polypropylene pipe.
The use of adhesives and fast-hardening components with high adhesion to create durable and tight joints.
Cold welding allows you to solve the problem of how to weld a polypropylene pipe for heating in places where it is not possible to use electrical equipment.
Important! The quality of the joints depends on the class of welding equipment no less than on the qualifications of the master installer. Pipes must be prepared for welding. The presence of dirt, water, organic substances and poor-quality cut, welding of pipes pp with a temperature lower than the plastic melt lead to fragile seams, and as a result, the tightness of the joints is out of the question.
Manual welding of polypropylene pipes
In order to weld PP pipes, it is necessary to stock up with the necessary equipment and accessories. First of all, a detailed project is drawn up, an assembly option is determined, and a decision is made on how to weld a polypropylene pipe with fittings and a reciprocal of the pipeline. Based on the configuration and geometric shape of the future pipeline, welding for a polypropylene pipe is also determined, which is best suited for a particular project and does not entail an increase in the construction estimate. The number of swivel fittings, branch tees and couplings is calculated and the order mounting, He is the procedure for welding polypropylene pipes.
During installation, it is possible to adjust the piping, but due to the ease of connection, this does not cause special problems.
For manual welding of polypropylene pipes, a large supply of tools and special skills will not be required. Exact adherence to the assembly sequence makes it possible to create a reliable water supply or heating system that is tight throughout.
Tools and equipment:
- scissors or cutter for plastic pipes. More preferable scissors guillotine type, with a powerful blade and gear force transmission unit;
- tool for stripping reinforced PP pipes. It is a special cutter, and in a primitive form - a durable knife with a convenient handle and a short blade;
- it is advisable to use alcohol components for degreasing the surface. Typically, ethyl (isobutyl) alcohol is used. Acetone, which is very common as a degreasing agent for paints and varnishes, is not suitable for PP pipes - it simply destroys the surface, makes it loose and fragile;
- soldering iron for polypropylene pipes represents a surface - mandrel - on which nozzles for pipes and fittings are mounted, heated to a selected temperature (at least 260 degrees Celsius). Soldering irons are tube-shaped and in the form of an elongated hammer. A pipe-shaped soldering iron is more convenient to cook pipes in hard to reach places;
- Conventional building tape measure will help to avoid cost overruns. Correctly measured length of the plot will minimize the number of cuts and adjustments;
- template in the form of a short section of a pipe of larger diameter. The length of the template must exactly match the depth of the pipe in the fitting. It’s better and more convenient to use a template with a bottom.Butt welding does not require the use of templates.
If the technology for welding a polypropylene pipe for heating is correctly observed, then after cooling the weld, an even, neat bead is formed, equal in height throughout its entire length.
Important! Excess molten plastic inside the welded parts will lead to a decrease in the internal section of the pipeline. This leads to an unplanned increase in pressure, and impairs the flow of water or coolant inside the heating system. The more thorough the soldering approach, the better the quality of the welds.
Installation steps and soldering features
Strict adherence to all stages of the creation of the pipeline is necessary, the only way to get a reliable system.
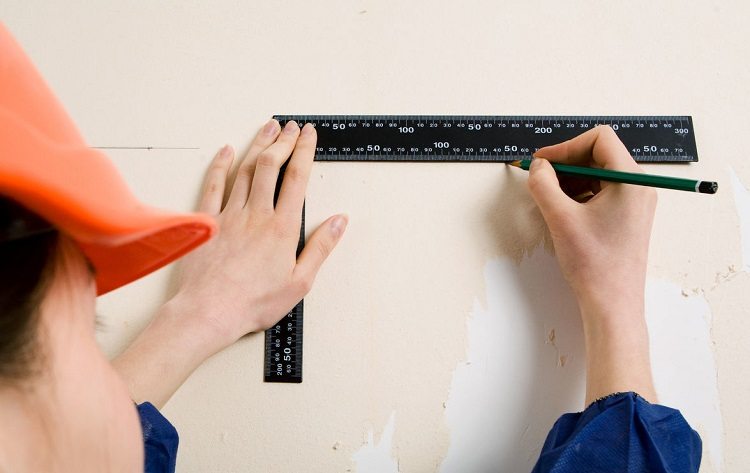
Before installing the pipes, you need to calculate and mark the places for fasteners and designate complex nodes
The procedure is as follows:
- PP pipes are prepared for work. A thorough inspection of the outside will reveal even before the assembly phase those pipes that may have manufacturing defects. This is especially important for pipes from which a hidden heating system is mounted. The temperature of the heating pipes is determined.
- The surface for installation is being prepared. A preliminary calculation is made of the attachment points of the branch piping branch piping, and the problem areas of the future system are identified: the intersection of walls and ceilings, the procedure for connecting to existing utilities. Do-it-yourself welding of a polypropylene pipe directly is not difficult, although sometimes it is necessary to cook system elements alternately.
- Tools are being prepared. The edged blade must be sharpened so as to create an even perpendicular cut without changing the geometry of the pipes.
- The nozzles of the iron for pipes (soldering iron) must be clean, without traces of molten plastic and other contaminants. Soldering iron tips are cleaned during heating with a cotton cloth or wood chips. The manufacturer informs the manufacturer how to properly cook the polypropylene pipe of each specific type - the temperature level and the heating time are indicated in the instructions for the soldering equipment.
- The nozzles are mounted on a soldering iron, heated to the melting point of the polypropylene pipe, welding occurs by softening the outer layer of the pipes or the inner surface of the fitting. Installation is carried out correctly if the heating temperature of the components corresponds to the cross section of the pipe and fitting.
The quality tool has a heating adjustment, and a stable stand. Welding pipes with such a soldering iron is convenient, and with minimal care, it is safe.
Long-distance industrial pipelines, technological systems, and heating systems that use large-diameter pipes are customarily interconnected using special equipment necessary for uniform heating of the connected sections. This is how the welding of polypropylene pipes occurs, the heating temperature is automatically controlled by the machine.
It is customary to cook the pipeline line, and in the presence of a mechanical welded complex, the connection is very strong.
Components of a stationary automatic welding complex:
- supporting frame on which all components are mounted;
- mechanical saw for trimming pipes;
- automatic grips for pp pipes;
- internal self - leveling inserts for reliable fixing of pipes;
- electronic temperature control unit;
- a heating element.
How to cook a pipe from polypropylene using a welding unit
The sequence of operations when working with a mechanical welding machine is slightly different from working with a manual soldering iron.The technology of welding polypropylene pipes in automatic mode is similar to manual soldering, except that the pipe is sheared (trimmed) with a mechanical saw and the pipe clamps at the place of soldering provide mechanical grips. The process is called butt welding of polypropylene pipes.
The control of the heating temperature level during welding of polypropylene pipes and the automatic shutdown of the heating element are provided by the control system unit.
Butt welding of a polypropylene pipe using an automatic unit takes a minimum of time, and is of high quality suture joints. The precise welding temperature of the polypropylene pipe is another advantage of the automatic system. For heating systems, this is important, but the cost of professional equipment is quite high. But this problem is solved simply: you can rent the necessary devices.